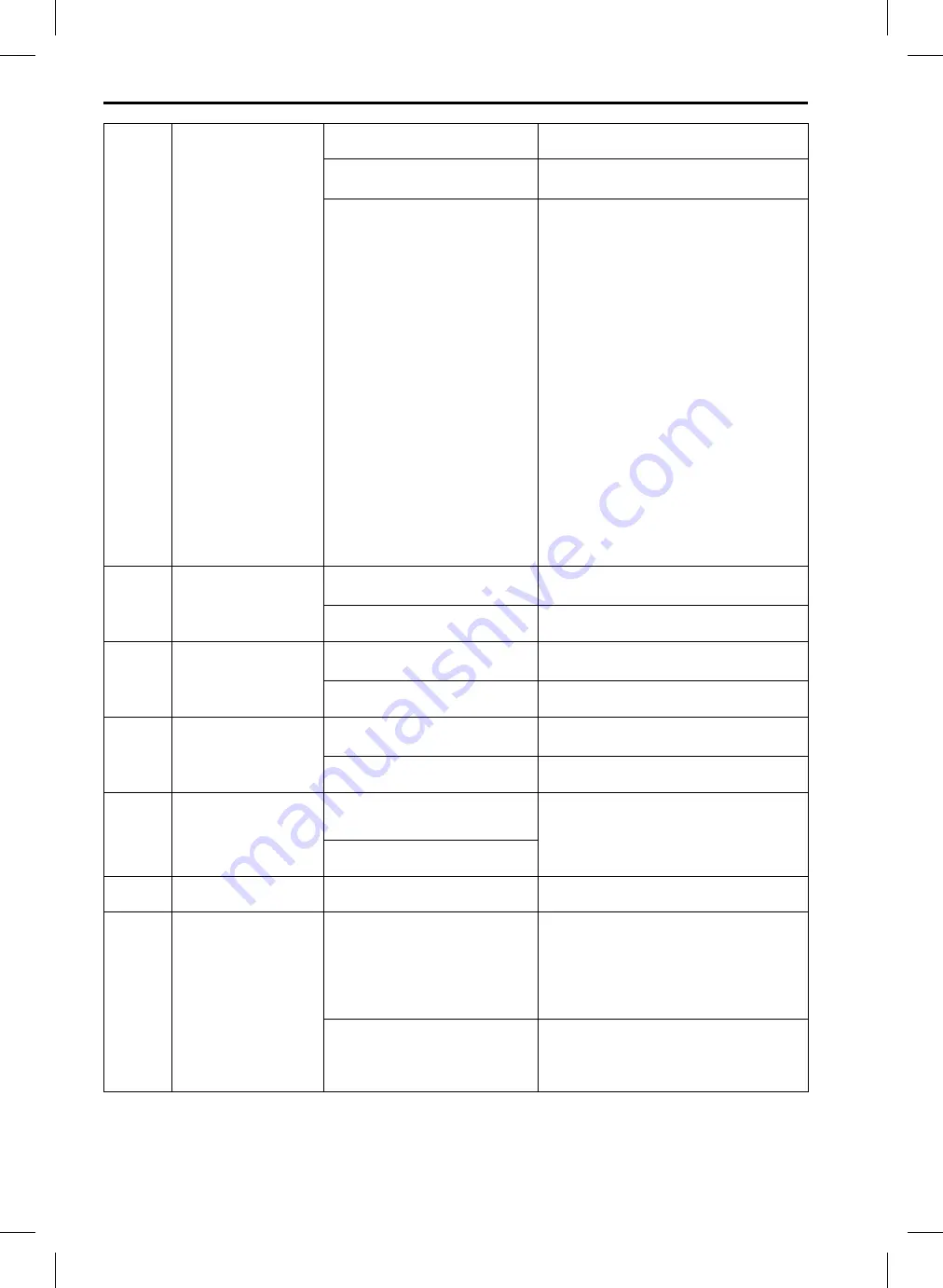
344
YASKAWA ELECTRIC
SIEP C710617 19A YASKAWA AC Drive CR700 Technical Manual
oH3
Motor Overheat (PTC
Input)
The thermistor wiring that detects motor
temperature is defective.
Correct wiring errors.
A fault occurred on the machine.
Example: The machine is locked.
Examine the machine and remove the cause of the
fault.
The motor has overheated.
•
Examine the load level, acceleration/deceleration
times, and motor start/stop frequency (cycle
time).
•
Decrease the load.
•
Increase the values set in
C1-01 to C1-08
[Acceleration/Deceleration Time]
.
•
Set
E2-01 [Motor Rated Current (FLA)]
correctly to the value specified by the motor
nameplate.
•
Make sure that the motor cooling system is
operating correctly, and repair or replace it if it is
damaged.
•
Adjust
E1-xx [V/f Pattern Parameters]
settings.
Decrease the values set in
E1-08 [Mid Point A
Voltage]
and
E1-10 [Minimum Output Voltage]
.
For motor 2, adjust
E3-xx [V/f Pattern for Motor
2]
settings. Decrease the values set in
E3-08
[Motor 2 Mid Point A Voltage]
and
E3-10
[Motor 2 Minimum Output Voltage]
. For motor
3, adjust
E7-xx [V/f Pattern for Motor 3]
settings. Decrease the values set in
E7-08
[Motor 3 Mid Point A Voltage]
and
E7-10
[Motor 3 Minimum Output Voltage]
.
Note:
If
Ex-08
and
Ex-10
are set too low, the overload
tolerance will decrease at low speeds.
oL3
Overtorque 1
A fault occurred on the machine.
Example: The machine is locked.
Examine the machine and remove the cause of the
fault.
The parameters are incorrect for the
load.
Adjust the overtorque detection parameters.
oL4
Overtorque 2
A fault occurred on the machine.
Example: The machine is locked.
Examine the machine and remove the cause of the
fault.
The parameters are incorrect for the
load.
Adjust the overtorque detection parameters.
oL5
Overload Detection (oL5)
A fault occurred on the machine.
Example: Overload occurred.
Examine the machine and remove the cause of the
fault.
The parameters are incorrect for the
load.
Adjust the overload detection parameters.
oL6
Light-load Accel 2 Fault
(oL6)
The setting for hold level and fault
detection level of Light-load 2 functions
are not appropriate.
Output frequency >
S4-08 [Light-load 2
Activation Freq]
.
Adjust
S4-10 [L-L 2 Motoring Hold Level]
,
S4-12
[L-L 2 Regen Hold Level]
, and
S4-15 [L-L 2 Fault
Detection Level]
settings.
oS
Overspeed
Overshoot is occurring.
Decrease
C5-01 [ASR Proportional Gain 1]
and
increase
C5-02 [ASR Integral Time 1]
.
ov
DC Bus Overvoltage
There are surge voltages in the input
power supply.
Connect a DC reactor to the drive.
Note:
If you turn the phase advancing capacitors ON
and OFF and use thyristor converters in the
same power supply system, there can be surge
voltages that irregularly increase the input
voltage.
The drive output cable or motor is
shorted to ground. (The current short to
ground is charging the main circuit
capacitor of the drive through the power
supply.)
1. Examine the motor main circuit cable,
terminals, and motor terminal box, and then
remove ground faults.
2. Re-energize the drive.