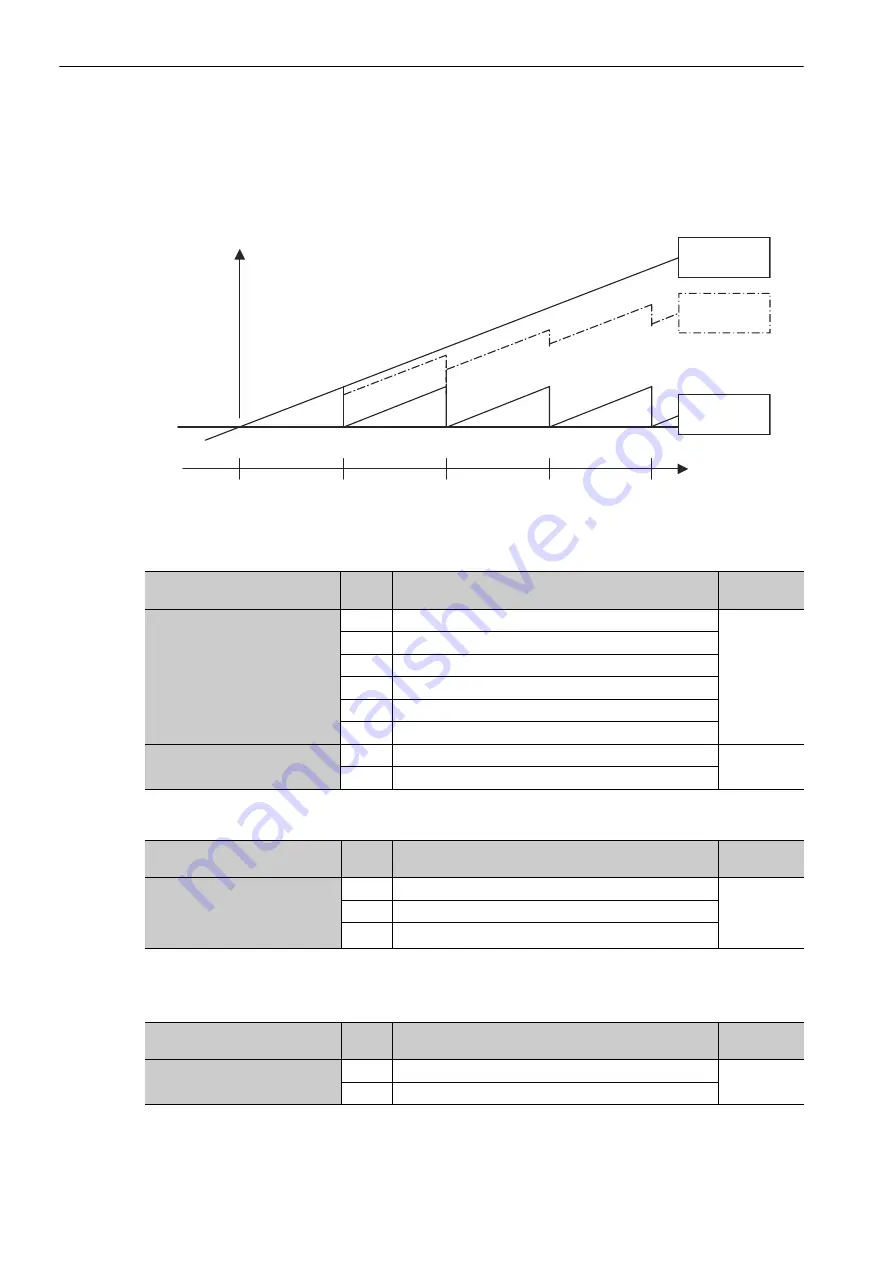
6 Additional Functions
6.1.7 Setting the Motor Type, Application Selection (Pn01E.0), and Winding Selection (Pn01E.1)
6-6
Setting Example
Increase this value if the belt slip ratio or twisting is too high.
Set this value to 0 to read the external encoder value as is.
At the factory setting of 20, the second revolution of the servomotor begins from the point where the deviation
in the first servomotor revolution is multiplied by 0.8.
6.1.7
Setting the Motor Type, Application Selection (Pn01E.0), and Winding
Selection (Pn01E.1)
6.1.8
Setting the Encoder Type (Pn01F.0)
∗
The servomotor constants are stored in the SERVOPACK for serial encoders with no servomotor constants.
6.1.9
Setting Absolute Encoder Usage (Pn002.2)
Note: If an absolute external encoder is used, the external encoder will function as an absolute encoder even if Pn002.2 is
set to 1.
Pn52A = 0
Pn52A = 100
Pn52A = 20
Small
Large
3rd revolution
2nd revolution
1st revolution
0th revolution
Number of Servomotor Revolutions
Deviation between the Servomotor and External Encoder
Parameter No.
Setting
Range
Description
Factory
Setting
Motor Type Setting and
Application Selection
Pn01E.0
0
SPM motor for servo
0
1
SPM motor for spindle axis
2
Induction motor for servo
3
Induction motor for spindle axis
4
IPM motor for servo
5
IPM motor for spindle axis
Winding Selection
Pn01E.1
0
None
0
1
Mechanical winding selection
Parameter No.
Setting
Range
Description
Factory
Setting
Encoder Type
Pn01F.0
0
Serial encoder
0
1
Pulse encoder
2
Serial encoder (no servomotor constants)
*
Parameter No.
Setting
Range
Description
Factory
Setting
Absolute Encoder Usage
Pn002.2
0
Use absolute encoder as an absolute encoder.
0
1
Use absolute encoder as an incremental encoder.