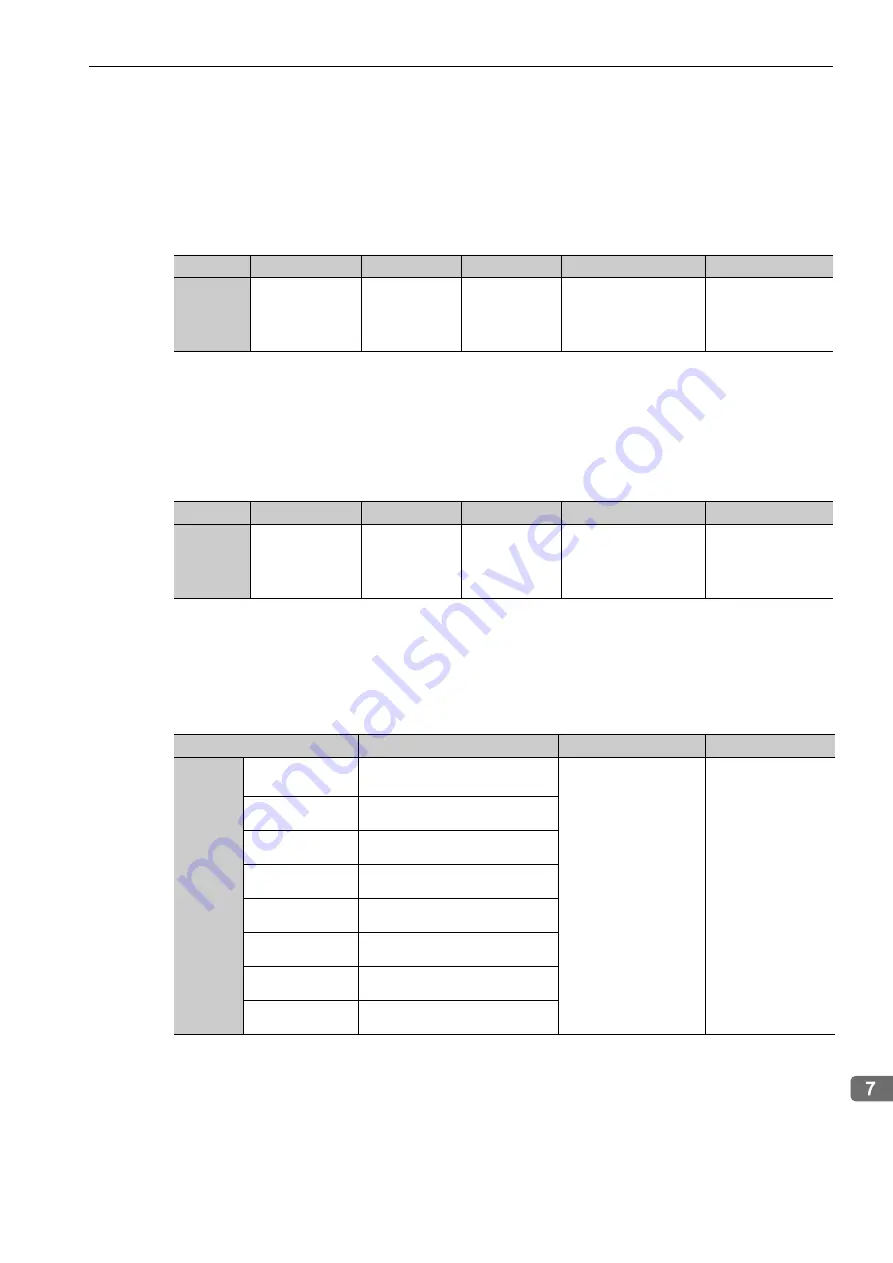
7.6 Emergency Stop Processing
7-15
Alarm and W
arning Processing
(4) Delay from Emergency Stop Signal to Axis Stop Processing
The delay from when the emergency stop signal turns OFF (emergency stop state) until the SERVOPACK
starts emergency stop processing (deceleration to a stop and then base block) is set in parameter Pn630.
Normally, if the emergency stop button is pressed, the axes decelerate to a stop immediately and therefore the
factory setting of 0 for Pn630 is recommended
(5) Delay Until the Main Circuit Turns OFF
The delay from the time the emergency stop signal turns OFF (emergency stop state) until the power regener-
ation converter turns OFF the main circuit magnetic contactor is set in parameter Pn631.
Set the time so that all axes that are connected to the power regeneration converter can completely stop before
the main circuit is turned OFF. If the main circuit magnetic contactor is turned OFF during axis deceleration,
an Undervoltage Alarm (A.410) will occur in the SERVOPACK.
∗
If multiple SERVOPACKs are connected to the power regeneration converter, the highest set value among those SER-
VOPACKs is used as the effective set value.
(6) Emergency Stop Signal Monitor
Assign the emergency stop signal state (ESTP2) with parameter Pn860 to monitor the status of the emergency
stop signal through MECHATROLINK-III communications from the host controller.
Parameter
Setting Range
Setting Unit
Factory Setting
When Enabled
Classification
Pn630
0 to 10000
1 ms
0 ms
Immediately
Setup
Parameter
Setting Range
Setting Unit
Factory Setting
When Enabled
Classification
Pn631*
0 to 10000
1 ms
0 ms
After restart
Setup
Parameter
Meaning
When Enabled
Classification
Pn860
n.
0
(factory setting)
No ESTP2 assignment.
After restart
Setup
n.
1
Assigns ESTP2 to bit 24.
n.
2
Assigns ESTP2 to bit 25.
n.
3
Assigns ESTP2 to bit 26.
n.
4
Assigns ESTP2 to bit 27.
n.
5
Assigns ESTP2 to bit 28.
n.
6
Assigns ESTP2 to bit 29.
n.
7
Assigns ESTP2 to bit 30.