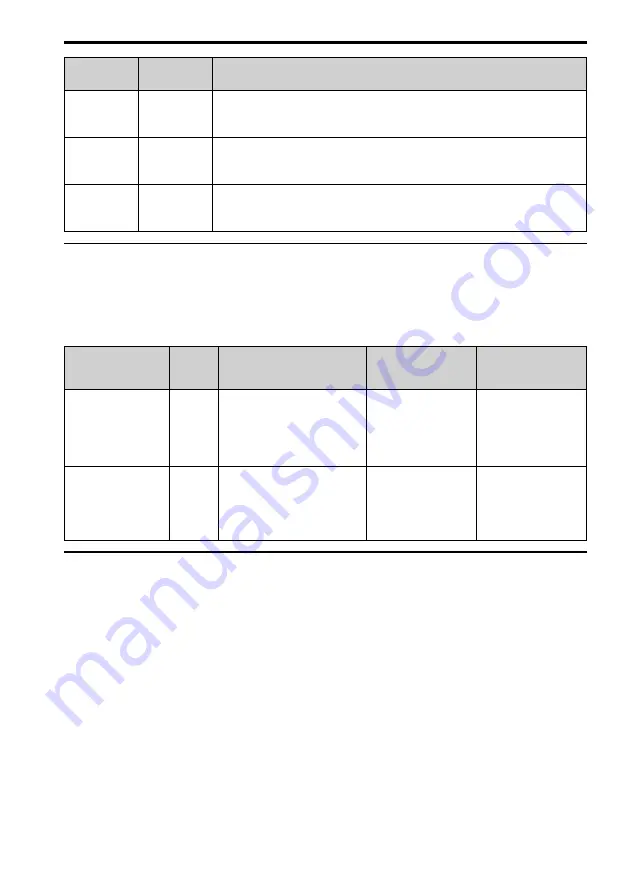
12 Drive Control, Duty Modes, and Programming
YASKAWA
TOEPC71061752B GA500 Drive Installation & Primary Operation
81
Control
Methods
A1-02
Main Applications
V/f
0
•
Use for main variable-speed applications, especially when you operate more than
one motor with one drive.
•
Use also when you do not have sufficient data to set the motor parameters.
OLV
2
(Default)
•
Main Applications of Variable Speed Control
•
Use for applications in which high-precision and high performance are necessary
and you do not use speed feedback.
EZOLV
8
•
Main Applications of Variable Speed Control
•
Use for applications in which high-precision and high performance are not
necessary and you do not use speed feedback.
◆
Drive Duty Modes
The drive has two duty modes from which to select for the application: Heavy Duty (HD) and
Normal Duty (ND).
Refer to
for information about the differences between HD and ND ratings.
Table 12.1 Drive Duty Modes
Duty Rating
C6-01
Setting
Application
Default Carrier
Frequency
Overload Tolerance
(oL2 [Drive
Overload])
Heavy Duty Rating
(HD)
0
•
Extruder
•
Conveyor
•
Cranes
•
Constant torque or high
overload capacity
Determined by o2-04,
A1-02
150% of the rated
output current for 60
seconds The permitted
frequency of overload is
one time each 10
minutes.
Normal Duty Rating
(ND)
1
•
Fan
•
Pump
•
Blower
•
Variable speed control
Determined by o2-04,
A1-02
110% of the rated
output current for 60
seconds The permitted
frequency of overload is
one time each 10
minutes.
◆
Auto-Tuning for Induction Motors
This section gives information about Auto-Tuning for induction motors. Set motor parameters
E1-xx and E2-xx
(or, for motor 2,
E3-xx and E4-xx
) for Auto-Tuning.
Note:
Do Stationary Auto-Tuning if you cannot do Rotational Auto-Tuning. There can be large differences between the
measured results and the motor characteristics when Auto-Tuning is complete. Examine the parameters for the
measured motor characteristics after you do Stationary Auto-Tuning.