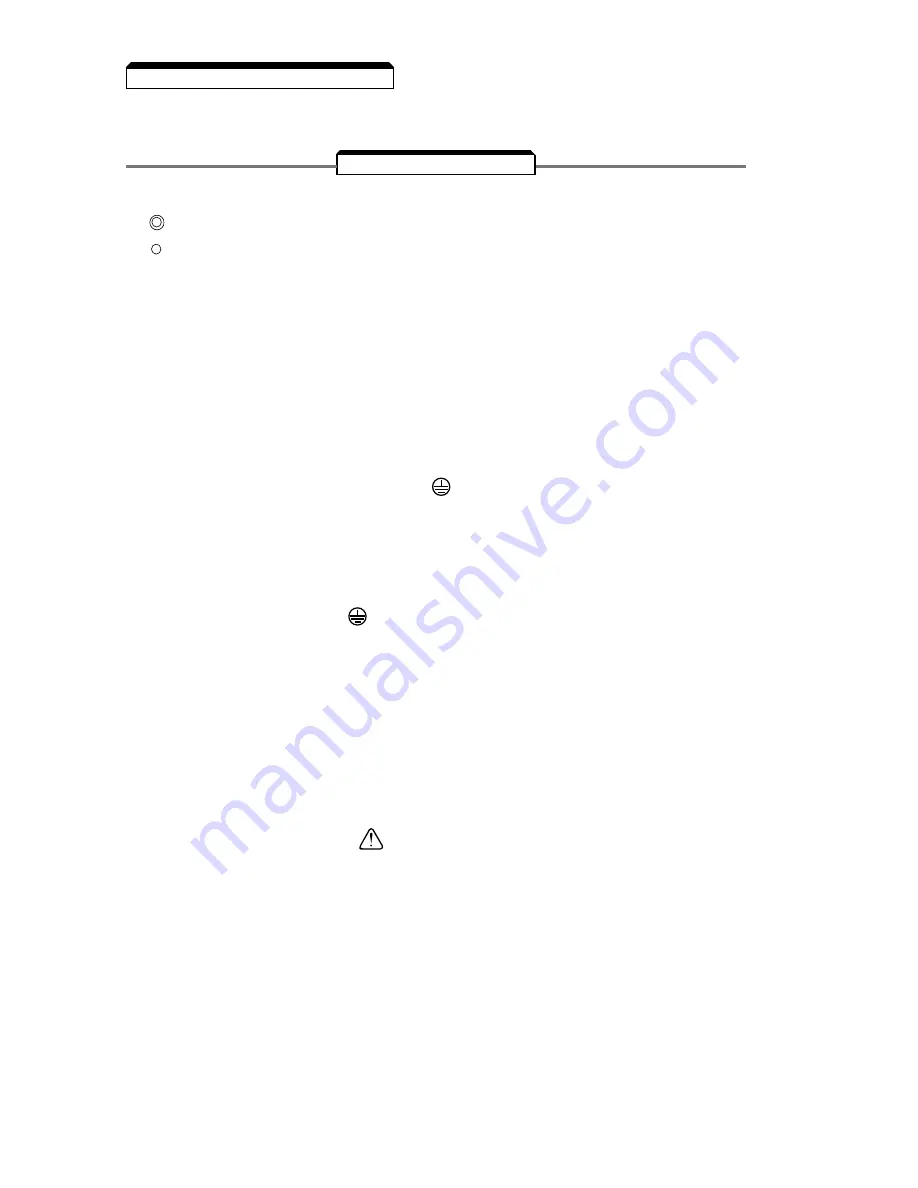
1-16
NOTES FOR FIGURE 1-6
✱
– Indicates components not supplied.
– Main circuit terminal.
– Indicates control circuit terminal.
( ) – Indicates alternate terminal marking, i.e., (R) and L1.
▲
– Function labels shown for these terminals are determined by factory settings of n050
through n056 (see paragraph 5.18).
●
– Function labels shown for these terminals are determined by factory settings of n057 through n059
(see paragraph 5.19).
♦
– Function label shown for this terminal is determined by factory setting of n004 (see paragraph 5.11A).
■
– Function labels shown for these terminals are determined by factory setting of n066 (see paragraph 5.17).
1.
Insulated twisted shielded wire is required.
2-conductor #18 GA. (Belden #8760 or equivalent)
3-conductor #18 GA. (Belden #8770 or equivalent)
Connect shield only at the Drive end (ground terminal ( ) ). Stub and isolate other end.
2.
+12V voltage output current capacity of control terminal FS is 20mA max.
3.
The Drive’s Electronic Thermal Overload function (n036, n037) meets standards set by UL and CUL for motor thermal
overload protection. If local code requires a separate mechanical overload protection, an overload relay should be
installed, interlocked with the Drive as shown. It should be the manual reset type to prevent automatic restart following
a motor fault and subsequent contact reclosure after cool down. For Canadian installations, overload 1OL is to be
provided in accordance with the Canadian Electrical Code, Part 1 and NEC.
4.
Customer to connect ground terminal ( ) to earth ground.
5.
If Digital Operator is used, remote operators which duplicate functions of its command keys (see Figure 4-1) may not
be required.
6.
For installation of Braking Resistor or Braking Resistor Unit, refer to Appendix 6, “Dynamic Braking Option”.
7.
An optional DC reactor may be added for harmonic attenuation, if needed; see separate instruction sheet for wiring.
8.
If application does not allow reverse operation, parameter n006 , Reverse Run Prohibit Selection, should be set to “ 1 ”
(Reverse Run Disabled) and Fwd/Rev input can be eliminated.
Parameter n050 must be set to “ 0 ”, AND parameter
n001 must be set to “ 11 ”. Resetting drive parameter
n001 to “ 10 ” may cause the motor to run in reverse
direction WITHOUT A RUN COMMAND, and possibly
result in equipment damage or personal injury.
G. Interconnection - 3 Wire
Continued
1.4 ELECTRICAL INSTALLATION
CAUTION
Summary of Contents for GPD315/V7-4X
Page 1: ...GPD 315 V7 and V7 4X Technical Manual...
Page 4: ......
Page 20: ...xvi...
Page 22: ......
Page 40: ...1 18...
Page 52: ...3 2...
Page 56: ...4 4...
Page 101: ...5 45 PID Block Diagram...
Page 130: ...A1 8...
Page 134: ...A3 2...
Page 136: ...A4 2...
Page 146: ...A6 6...
Page 150: ...A7 4...
Page 154: ...A8 4...
Page 158: ......
Page 160: ......