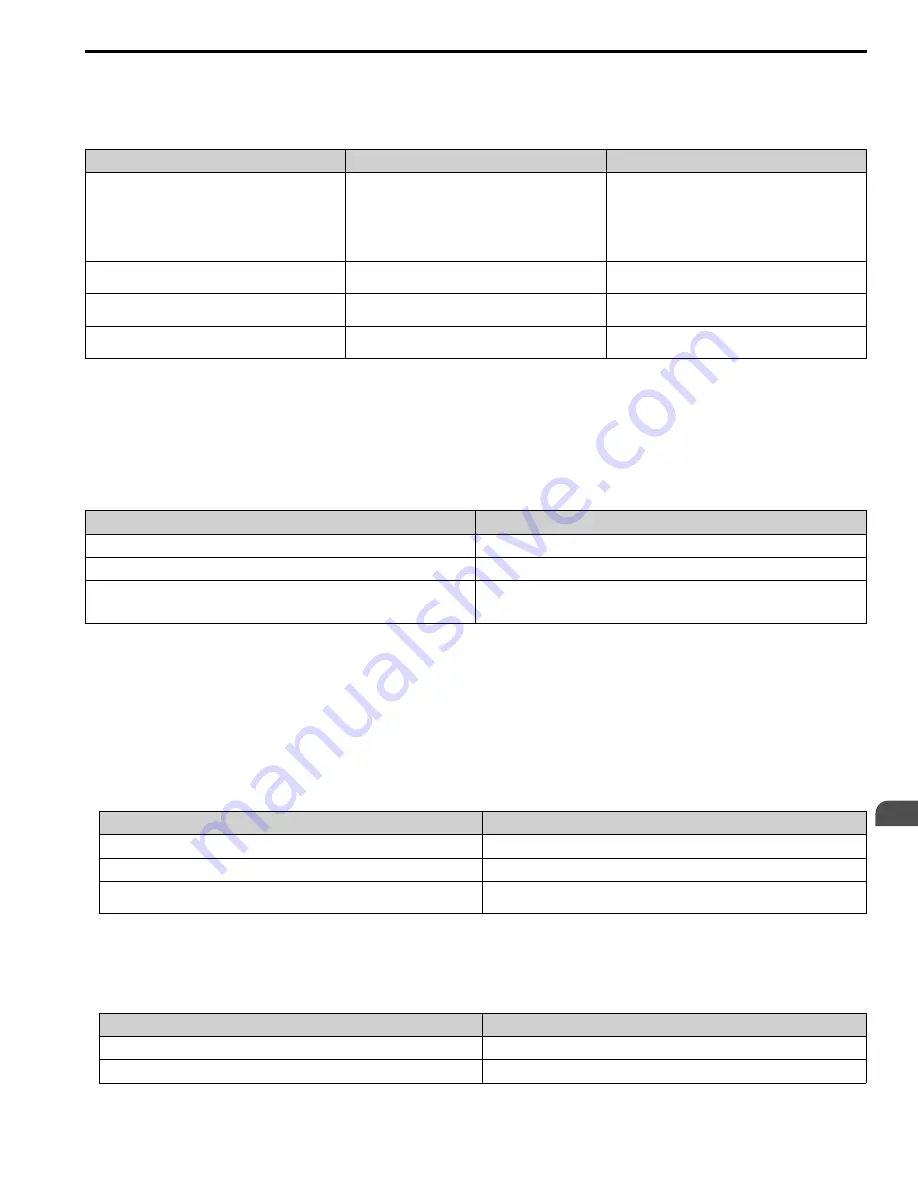
YASKAWA
SIEPYAIH6B01A HV600 AC Drive Bypass Technical Reference
209
■
PID Control Applications
shows applications for PID control.
Table 5.22 PID Control Applications
Application
Control Content
Sensors Used
Speed Control
•
The drive uses a feedback signal for the machine speed,
and adjusts that speed to align with the target value.
•
The drive uses speed data from other machinery as the
target value to do synchronous control. The drive then
adds that target value to the feedback from the machine
it is operating to align its speed with the other
machinery.
Tacho generator
Pressure control
The drive uses feedback from the actual pressure to hold
constant pressure.
Pressure sensor
Flow control
The drive uses feedback from the actual flow to hold
constant flow.
Flow rate sensor
Temperature control
The drive uses feedback from the actual temperature to
control a fan and hold constant temperature.
Thermocoupler, thermistor
■
Input Methods for the PID Setpoint
Use
b5-01 [PID Mode Setting]
to select how the PID setpoint is input to the drive.
When
b5-01 = 1 [Standard]
, the frequency reference set in
b1-01 [Frequency Reference Selection 1]
will be the PID
setpoint, or the one of the values shown in
will be the PID setpoint.
When
b5-01 = 3 [Fref + PID Trim]
, one of the inputs in
will be the PID setpoint.
Table 5.23 Input Methods for the PID Setpoint
Input Methods for the PID Setpoint
Setting Value
MFAI terminal A1
Set
H3-02 = C [Terminal A1 Function Selection = PID Setpoint]
.
MFAI terminal A2
Set
H3-10 [Terminal A2 Function Selection] = C
.
MEMOBUS/Modbus register 0006H
Sets MEMOBUS/Modbus register 000FH (Control Selection Setting) bit 1 to 1 (PID
setpoint input). Enters the PID setpoint to MEMOBUS/Modbus register 0006H (PID
setpoint, 0.01% units, signed).
Note:
If you set two inputs for the PID setpoint, it will trigger operation error
oPE07 [Analog Input Selection Error]
.
■
Entering the PID Feedback Value
You can use two methods to input the PID feedback value to the drive. One method uses a single feedback signal for
usual PID control. The other method uses two signals. The difference between those signals sets the deviation.
•
Use One Feedback Signal
Use
to select how the feedback signal is input to the drive for PID control.
Table 5.24 PID Feedback Input Method
PID Feedback Input Method
Setting Value
MFAI terminal A1
Set
H3-02 = B [PID Feedback]
.
MFAI terminal A2
Set
H3-10 = B
.
MEMOBUS/Modbus register 15FFH
Enters the PID setpoint to MEMOBUS/Modbus register 15FFH (PID setpoint, 0.01%
units, signed).
•
Use Two Feedback Signals and Calculate the Deviation from the Difference Between Those Signals
Use
to select how the second feedback value is input to the drive. The drive calculates the deviation of
the second feedback value. Set
H3-02 or H3-10 = 16 [Terminal A1/A2 Function Selection = Differential PID
Feedback]
to enable the second feedback signal used to calculated the deviation.
Table 5.25 PID Differential Feedback Input Method
PID Differential Feedback Input Method
Setting Value
MFAI terminal A1
Set
H3-02 = 16
.
MFAI terminal A2
Set
H3-10 = 16
.
Summary of Contents for H6B1A002
Page 12: ...12 YASKAWA SIEPYAIH6B01A HV600 AC Drive Bypass Technical Reference...
Page 74: ...Page Intentionally Blank...
Page 76: ...Page Intentionally Blank...
Page 454: ...5 14 Z Bypass Parameters 454 YASKAWA SIEPYAIH6B01A HV600 AC Drive Bypass Technical Reference...
Page 590: ...8 6 Storage Guidelines 590 YASKAWA SIEPYAIH6B01A HV600 AC Drive Bypass Technical Reference...
Page 780: ...11 3 European Standards 780 YASKAWA SIEPYAIH6B01A HV600 AC Drive Bypass Technical Reference...