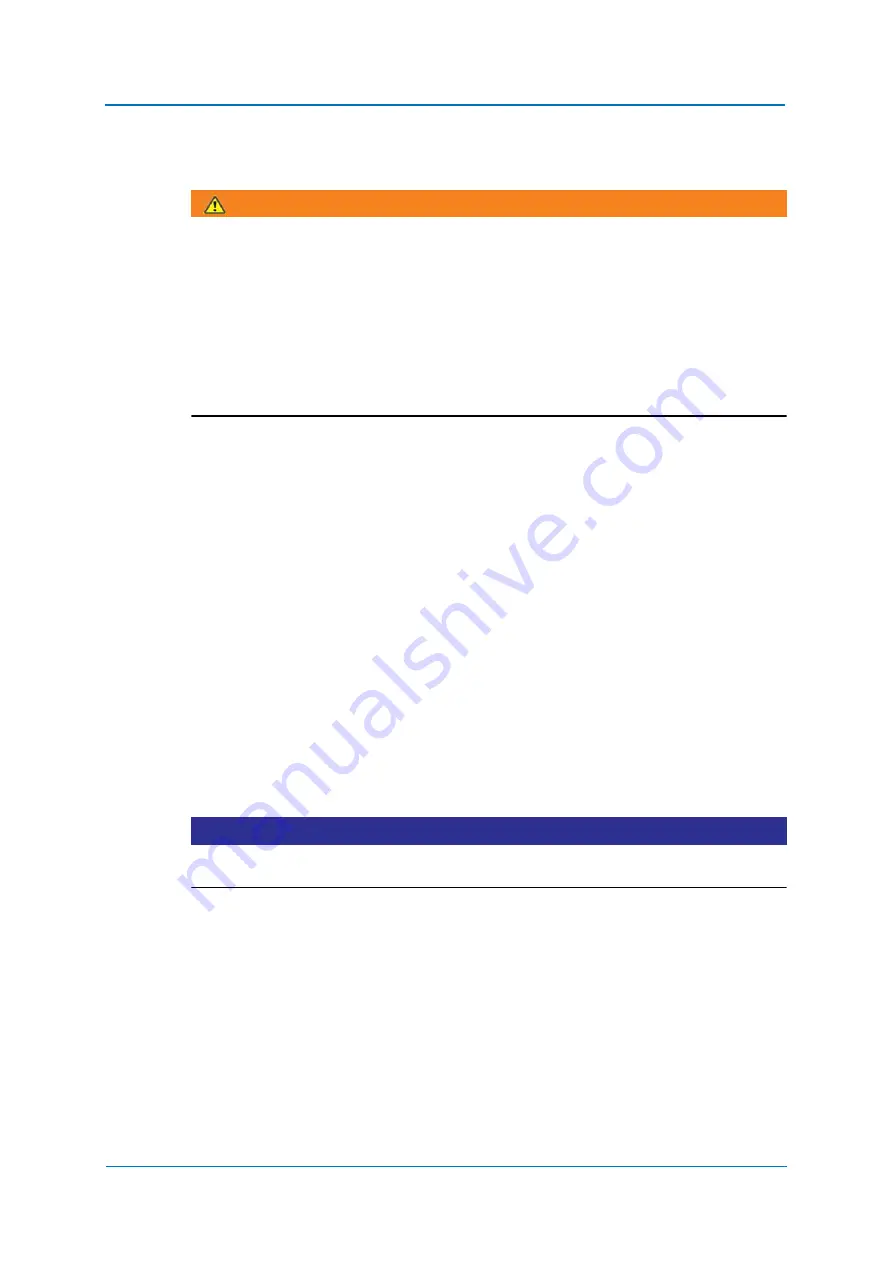
Maintenance and inspection
9
-
71
9.5.4
Gas injecting procedure
Gas injecting procedure
WARNING!
Danger of injury in case of unforeseeable robot motion
Releasing the brake of the L -axis motor will lead to loss of the retaining force. As a result
the compensating cylinder will extend or shorten and will lead to the rotation of the L-arm.
Before you drain or fill the gas from the compensating cylinder, check the brake function
of the L -axis motor.
The robot should be secured for the L- axis should not move unpredictably.
Keep safe distance in the direction of movement of the robot axes.
Keep the appropriate pressure value show in table Tab. 9-2: "Adequate gas pressure
according to the surface temperature of compensating cylinder".
1. Move the robot to the home position and turn off the power of the robot controller.
2. Remove the cover and insert the quick connector to the gas inlet.
3. Connect the gas filling device to the quick connector after confirming that the blowdown
valve, needle valve and gate valve of the gas filling device are firmly closed.
4. Check the temperature of the gas balancer surface.
5. Connect the nitrogen gas cylinder to the gas filling device.
6. Release the valve of the nitrogen gas cylinder and then set the gas pressure slightly
higher than the adequate pressure shown in table Tab. 9-2: .
7. Slowly open the needle valve of the gas filling device.
8. Release the gate valve of the gas filling device to inject gas until the gas pressure
indicated by the digital pressure gauge is slightly higher than the adequate pressure
shown in table Tab. 9-2: .
9. Close the gate valve of the gas filling device, wait for the gas pressure in the gas
balancer to stabilize and then confirm that the gas pressure is the adequate pressure
shown in table Tab. 9-2: .
If the pressure is higher than the adequate pressure, discharge the gas gradually and
stabilize the gas pressure, then confirm that the gas pressure finally reached the
adequate value.
NOTICE
After draining/filling with gas, wait a few minutes to allow for the stabilization of the gas
pressure and then measure the gas pressure.
10. Close needle valve of the gas filling device and the valve of the nitrogen gas cylinder.
11. Disconnect the gas filling device from the quick connector.
12. Remove the quick connector and mount the cover, then tighten the screw M6 with
flange by using a tightening torque shown in table 9.4 "Refill/Replace grease.".
13. Mount the cover and tighten the screws by using the tightening torque shown in table
14. Release the blowdown valve of the gas filling device and regulator and then discharge
the gas in the hose.
15. Disconnect the gas filling device from the nitrogen gas cylinder.
16. Turn on the power to the robot controller.