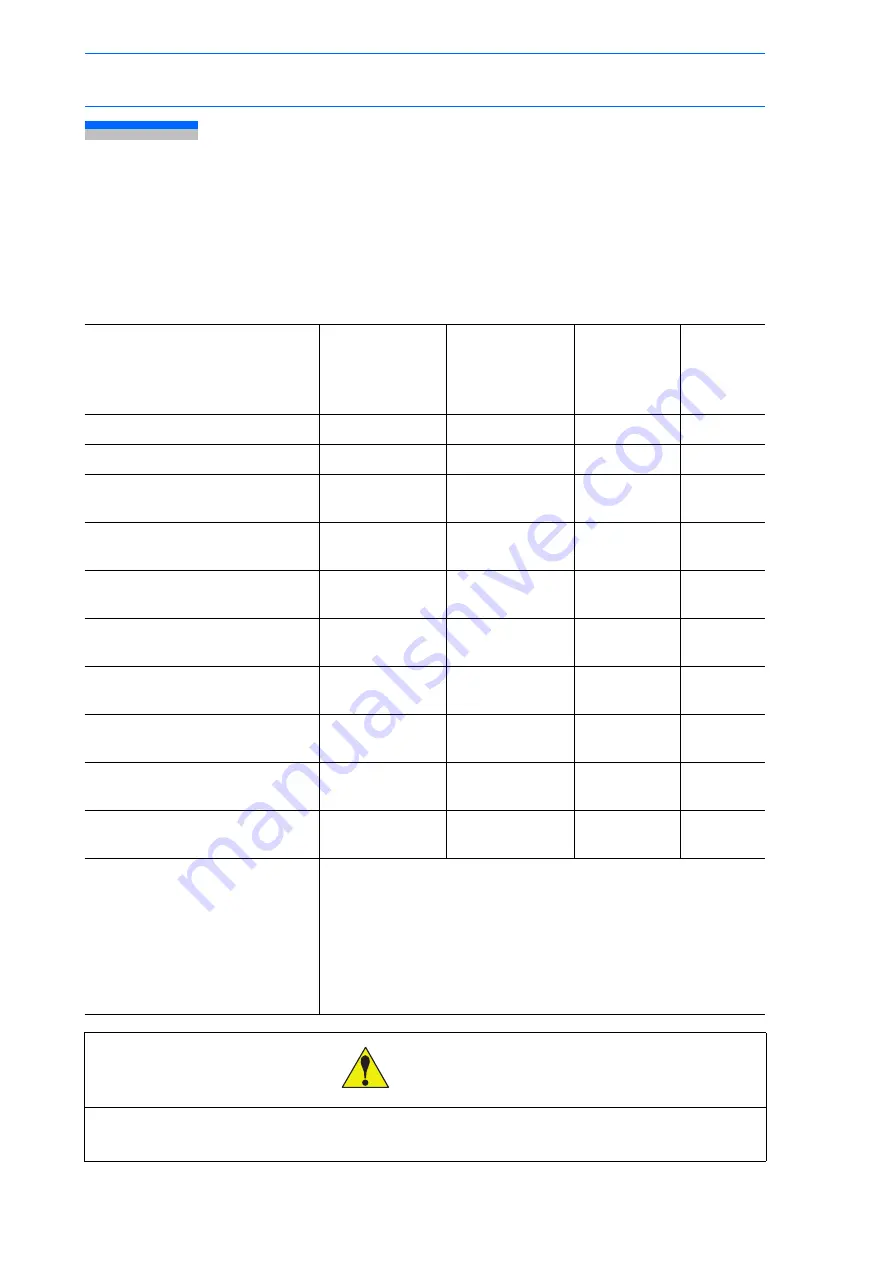
3 Installation
3.2 Installation Site
3-2
154771-1CD
HW0485080
3.2
Installation Site
This section describes the conditions of the installation site for the robot system. Only devices
that are approved as explosion-proof can be installed in hazardous locations. Refer to the
local regulations and safety codes for the definition of a hazardous location. Install the
controller and control panels in a location free from water drops, dust, and dirt.
Table. 3-2 Installation Site
System Components
Hazardous
Location
(Inside Painting
Booth)
Non-hazardous
location
(Outside
Painting Booth)
Ambient
Temperature
Maximum
Ambient
Humidity
Manipulator (explosion-proof)
-
0 to 40
°
C
80 %RH
Controller (not explosion-proof)
×
0 to 45
°
C
90 %RH
Pneumatic unit
(not explosion-proof)
×
0 to 45
°
C
85 %RH
Programming pendant
(not explosion-proof)
×
0 to 40
°
C
85 %RH
Programming pendant
(explosion-proof) (Option)
0 to 40
°
C
85 %RH
Conveyor speed detector
(not explosion-proof)
×
0 to 50
°
C
90 %RH
Conveyor speed detector
(explosion-proof)
-
0 to 50
°
C
90 %RH
Conveyor switch
(explosion-proof)
-
0 to 50
°
C
90 %RH
Workpiece supplier
(explosion-proof)
0 to 50
°
C
85 %RH
Control panel for workpiece
supplier (not explosion-proof)
×
0 to 45
°
C
90 %RH
Safety devices
Box for emergency stop
switches
Safety plugs
Limit switches
Flashing light
Indicator lamps
Photoelectric switches
Selected according to the requirements of the customer. Refer
to the appropriate instruction manual provided separately.
×
: Not acceptable
: Acceptable
Devices that are not explosion-proof must not be installed in hazardous locations. Failure
to observe this warning may result in a fire.
DANGER
19 of 66