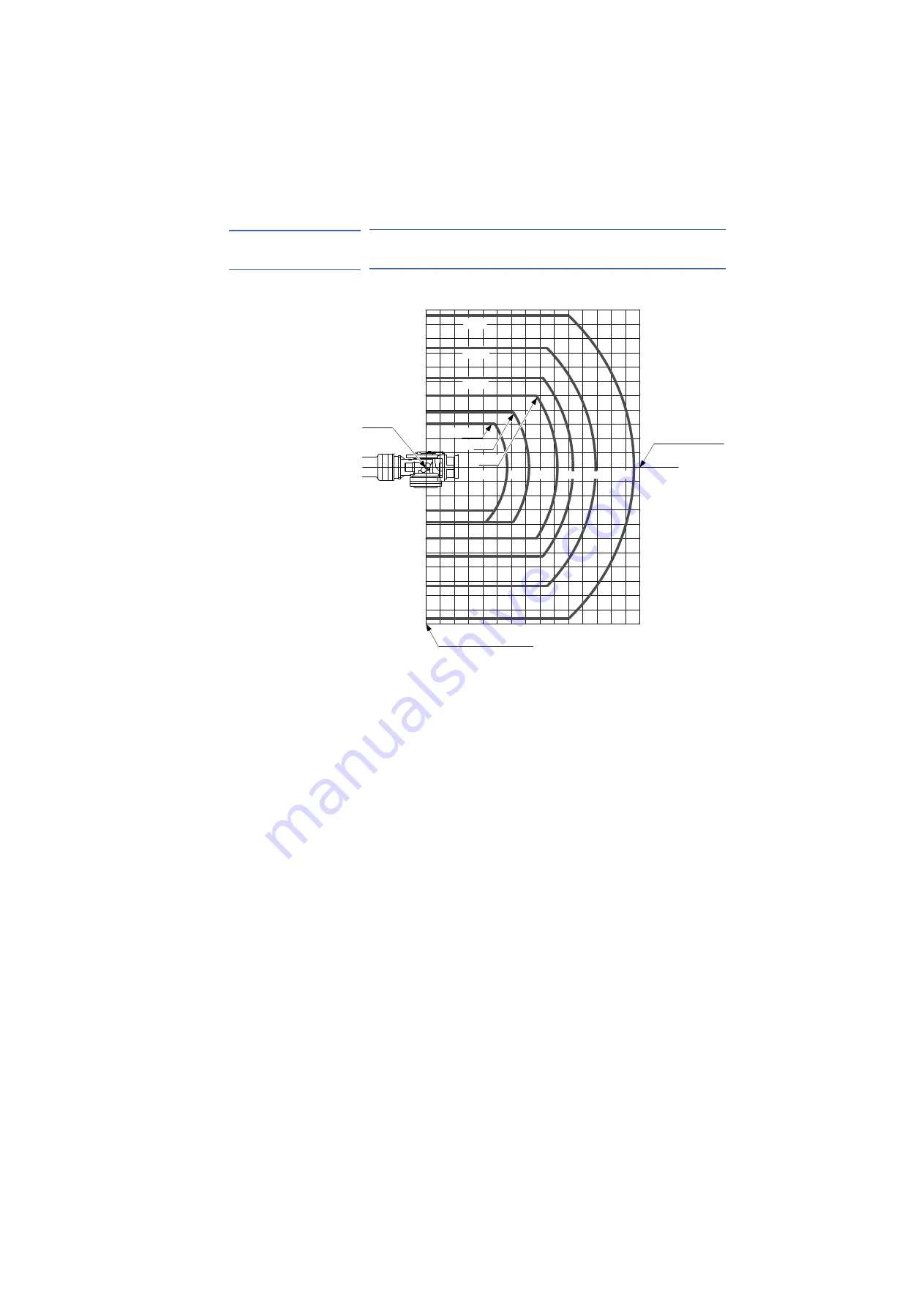
6-2
155976-1CD
HW0485249
ES165D
6 Allowable Load for Wrist Axis and Wrist Flange
6.1 Allowable Wrist Load
Fig. 6-1: Moment Arm Rating
1400
1200
1000
800
800
1000
40kg
60kg
80kg
1000
600
130kg
400
100kg
800
LB(mm)
600
400
LT(mm)
200
200
400
600
LT(mm)
165kg
P-point
T-, R-axis
center of rotation
B-axis center of rotation
43 of 92