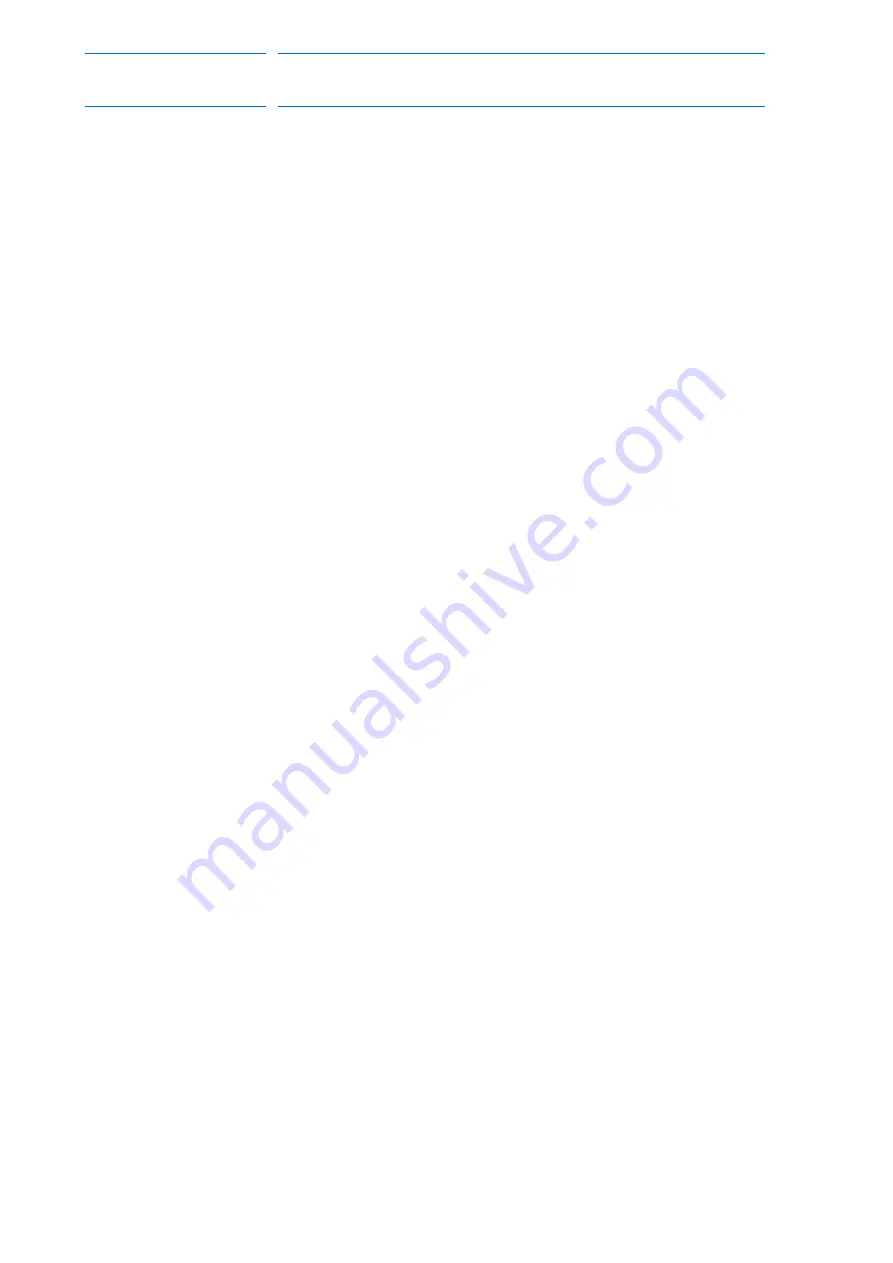
Programming, Operation, and Maintenance Safety
x
163471-1CD
HW1481050
MH50/MH50-35/MH80/
MS80 Zeroing
Programming, Operation, and Maintenance Safety
All operators, programmers, maintenance personnel, supervisors, and
anyone working near the system must become familiar with the operation
of this equipment. Improper operation can result in personal injury and/or
damage to the equipment. Only trained personnel familiar with the
operation, manuals, electrical design, and equipment interconnections of
this equipment should be permitted to program, or maintain the system.
All personnel involved with the operation of the equipment must
understand potential dangers of operation.
• Inspect the equipment to be sure no potentially hazardous conditions
exist. Be sure the area is clean and free of water, oil, debris, etc.
• Be sure that all safeguards are in place. Check all safety equipment
for proper operation. Repair or replace any non-functioning safety
equipment immediately.
• Check the E-Stop button on the operator station for proper operation
before programming. The equipment must be placed in Emergency
Stop (E-Stop) mode whenever it is not in use.
• Back up all programs and jobs onto suitable media before program
changes are made. To avoid loss of information, programs, or jobs, a
backup must always be made before any service procedures are
done and before any changes are made to options, accessories, or
equipment.
• Any modifications to the controller unit can cause severe personal
injury or death, as well as damage to the robot! Do not make any
modifications to the controller unit. Making any changes without the
written permission from YASKAWA will void the warranty.
• Some operations require standard passwords and some require
special passwords.
• The equipment allows modifications of the software for maximum
performance. Care must be taken when making these modifications.
All modifications made to the software will change the way the
equipment operates and can cause severe personal injury or death,
as well as damage parts of the system. Double check all
modifications under every mode of operation to ensure that the
changes have not created hazards or dangerous situations.
• This equipment has multiple sources of electrical supply. Electrical
interconnections are made between the controller and other
equipment. Disconnect and lockout/tagout all electrical circuits
before making any modifications or connections.
• Do not perform any maintenance procedures before reading and
understanding the proper procedures in the appropriate manual.
• Use proper replacement parts.
• Improper connections can damage the equipment. All connections
must be made within the standard voltage and current ratings of the
equipment.
10 of 51