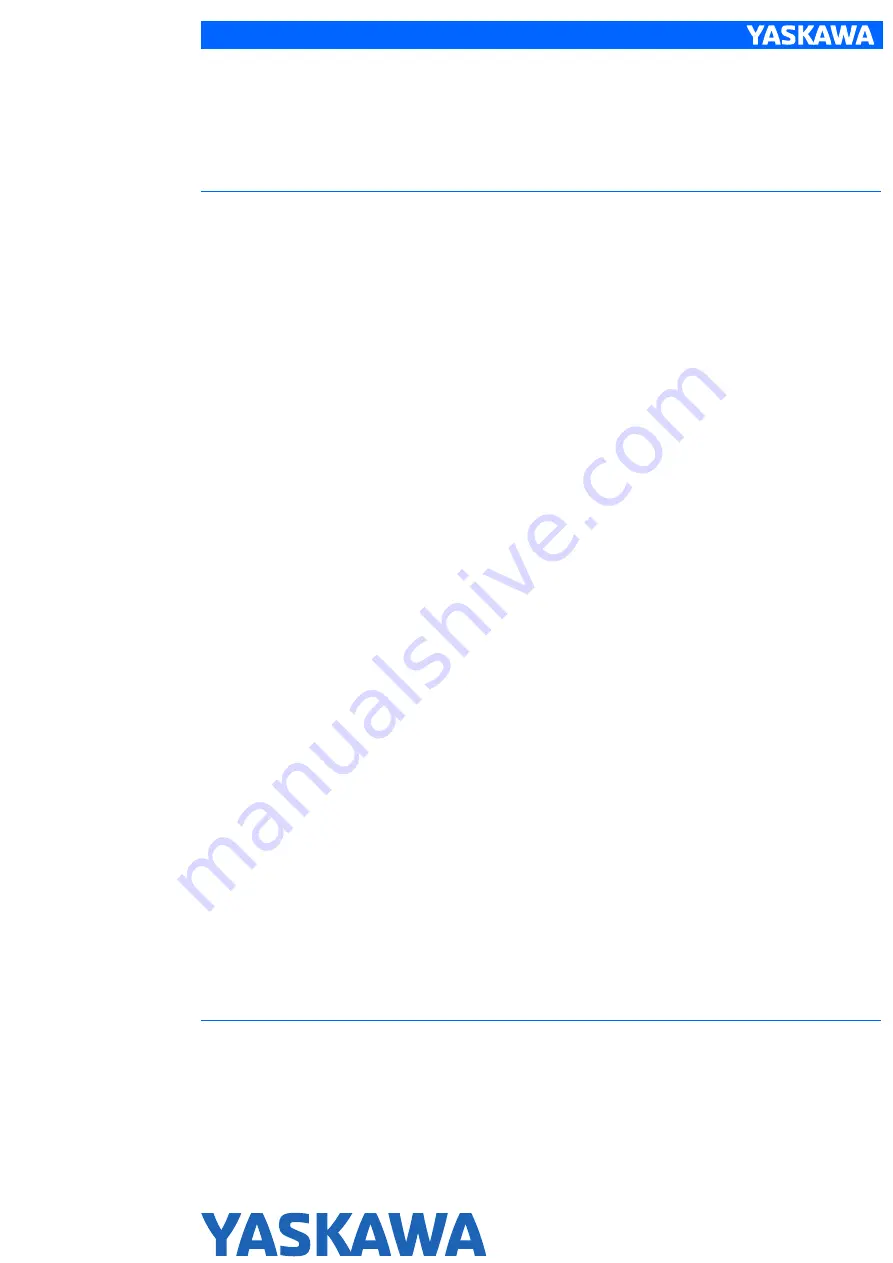
HEAD OFFICE
2-1 Kurosakishiroishi, Yahatanishi-ku, Kitakyushu 806-0004, Japan
Phone +81-93-645-7703
Fax +81-93-645-7802
100 Automation Way, Miamisburg, OH 45342, U.S.A.
Phone +1-937-847-6200
Fax +1-937-847-6277
YASKAWA America Inc. (Motoman Robotics Division)
Bredbandet 1 vån. 3 varvsholmen 392 30 Kalmar, Sweden
Phone +46-480-417-800
Fax +46-480-417-999
YASKAWA Nordic AB
Yaskawastrasse 1, 85391 Allershausen, Germany
Phone +49-8166-90-100
Fax +49-8166-90-103
YASKAWA Europe GmbH
Robotics Divsion )
9F, Kyobo
Securities
Bldg., 26-4, Yeouido-dong,
Yeongdeungpo-gu, Seoul 150-737, Korea
Phone +82-2-784-7844
Fax +82-2-784-8495
YASKAWA Electric Korea Co., Ltd
151 Lorong Chuan, #04-02A, New Tech Park, Singapore 556741
Phone +65-6282-3003
Fax +65-6289-3003
YASKAWA Electric (Singapore) PTE Ltd.
No7 Yongchang North Road, Beijing E&T Development Area
China 100176
Phone +86-10-6788-2858
Fax +86-10-6788-2878
YASKAWA SHOUGANG ROBOT Co. Ltd.
#426, Udyog Vihar, Phase- IV,
Gurgaon, Haryana, India
Fax +91-124-475-8542
Phone +91-124-475-8500
YASKAWA India Private Ltd. (Robotics Division)
YASKAWA Electric (China) Co., Ltd.
22/F One Corporate Avenue No.222, Hubin Road, Huangpu District, Shanghai 200021, China
Phone +86-21-5385-2200 Fax
㸩
86-21-5385-3299
YASKAWA Electric (Thailand) Co., Ltd.
59,1st-5th Floor, Flourish Building, Soi Ratchadapisek 18,Ratchadapisek Road,
Huaykwang, Bangkok 10310, THAILAND
Phone +66-2-017-0099 Fax +66-2-017-0199
12F, No.207, Sec. 3, Beishin Rd., Shindian District, New Taipei City 23143, Taiwan
Fax +886-2-8913-1513
Phone +886-2-8913-1333
YASKAWA Electric Taiwan Corporation
Secure Building-Gedung B Lantai Dasar & Lantai 1 JI. Raya Protokol Halim Perdanakusuma,
Jakarta 13610, Indonesia
Fax +62-21-2982-6741
Phone +62-21-2982-6470
PT. YASKAWA Electric Indonesia
Specifications are subject to change without notice
for ongoing product modifications and improvements.
MANUAL NO.
HW1483299
MOTOMAN-MPL80
II
SUPPLEMENTAL INSTRUCTIONS