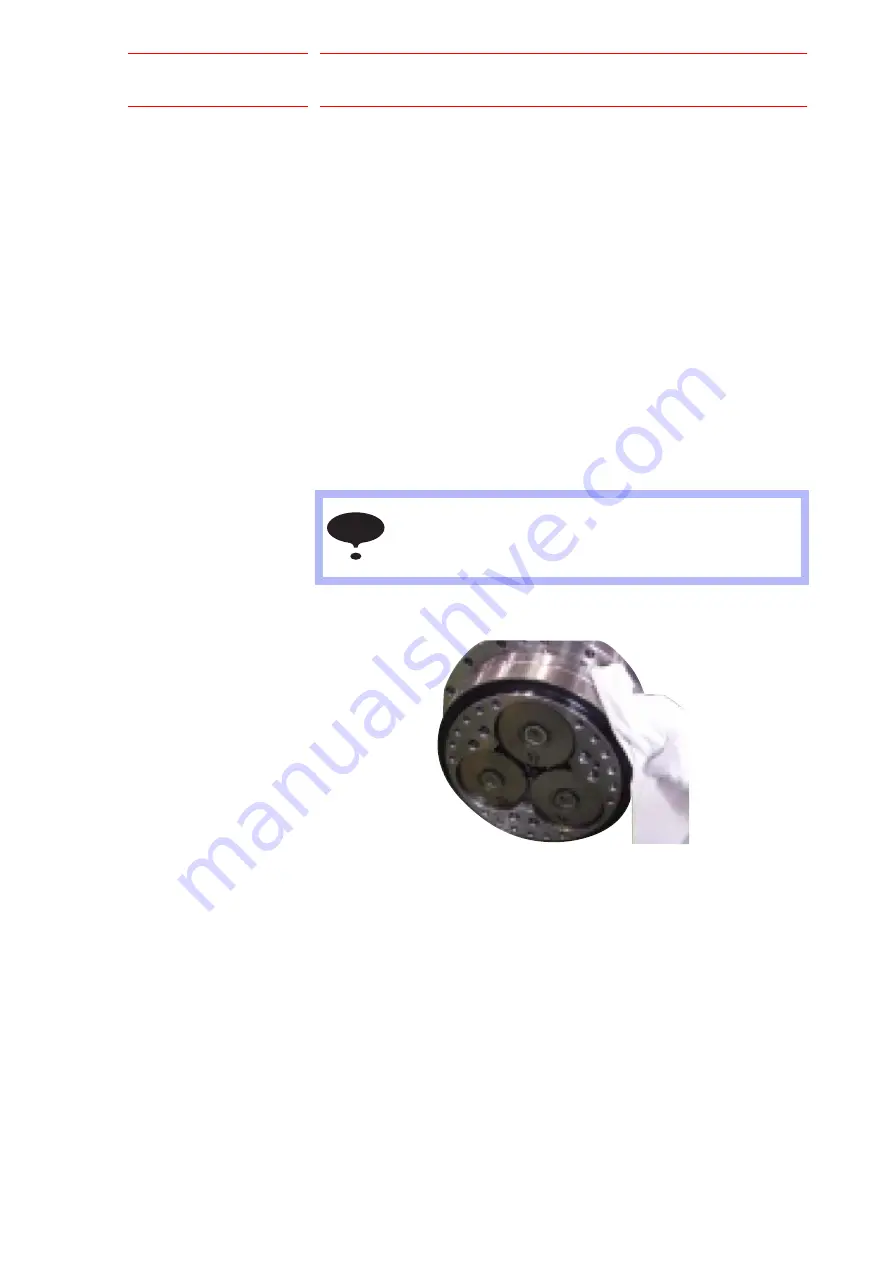
5
Notes on Grease Replenishment/Exchange Procedures
5.2
Removing, Applying, Assembling of Sealing Bond
5-9
HW1485471
HW1485471
5.2
Removing, Applying, Assembling of Sealing Bond
5.2.1 Removing Sealing Bond from Sealing Surface and Cleaning
1. Remove the sealing bond of the sealing surface of the manipulator on
which the speed reducer or the motor was mounted by using a spatula
etc.
2. In order to remove dust, dirt, foreign objects, and oil, wipe whole
surface of the speed reducer or motor for replacement by using a
waste cloth. (Refer to
fig. 5-4 “Wiping Whole Surface of Speed
.)
If not wiping whole surface of the speed reducer, the rust preventive oil
adhered to the speed reducer gradually flows out to the outside of the
manipulator, and a phenomenon considered as oil leakage occurs
(mis-recognition as oil leakage).
3. Saturate a clean cloth with the degreasing and cleaning agent, and
sufficiently degrease the sealing surface of the manipulator side and
the sealing surface of the speed reducer or the motor to be replaced.
Fig. 5-4: Wiping Whole Surface of Speed Reducer
NOTE
Do not pour the degreasing and cleaning agent directly to
the sealing surface. When the agent remains inside and at
the concave part of the speed reducer, the sealing bond
would not be solidified and this may cause grease leakage.
41/134