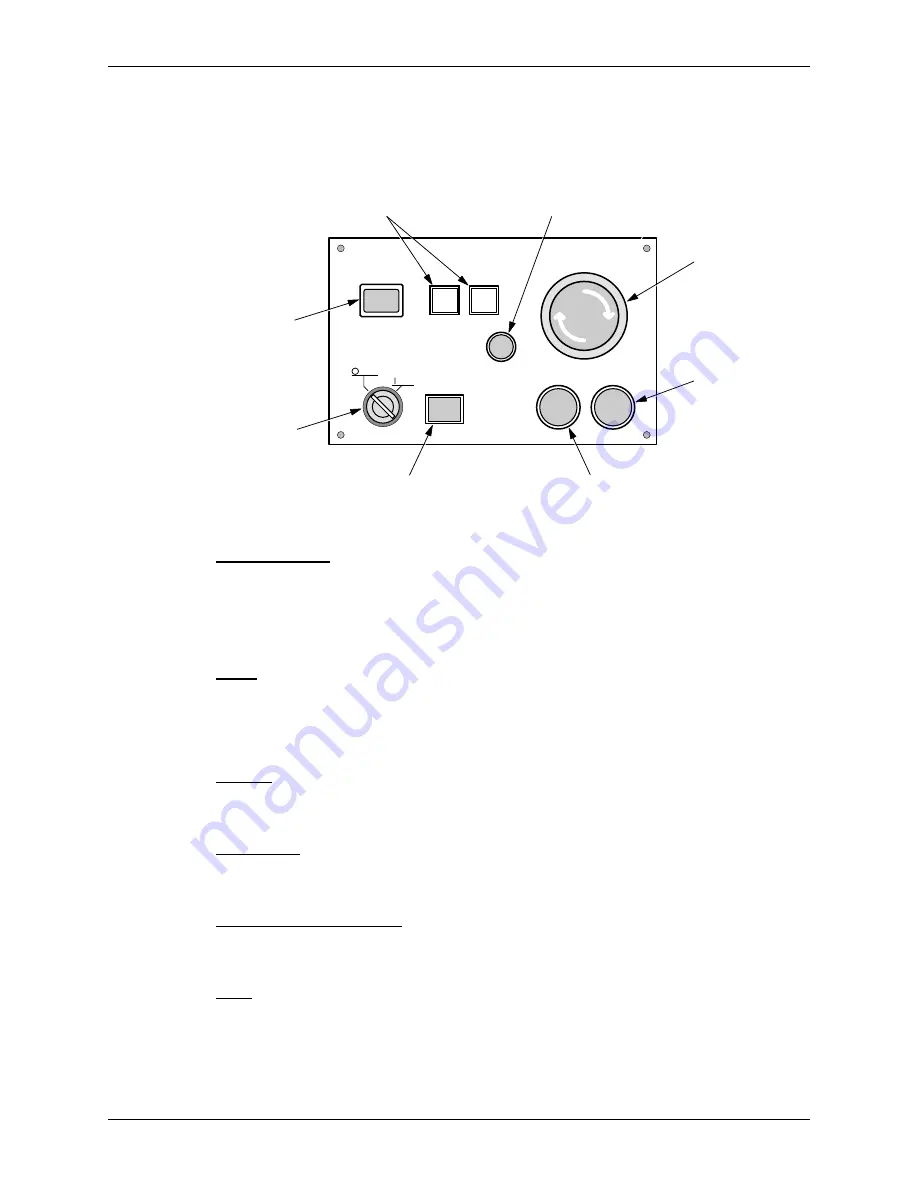
EQUIPMENT DESCRIPTION
Arc-WorldLite 50 System Manual
3-2
MOTO
MAN
3.2.1
Playback Panel
The playback panel (see Figure 3-2) contains the primary system controls and
consists of the features described below. For more information, refer to the
manipulator manual that came with your system.
Figure 3-2 XRC Playback Panel
Servo On Ready
The SERVO ON READY push button turns servo power ON. The switch lights
when servo power is on. In TEACH mode, the SERVO ON READY push button
operates only when the TEACH LOCK button on the programming pendant is ON
and the ENABLE switch on the programming pendant is held in.
Mode
The Mode push buttons (PLAY and TEACH) set the robot's mode of operation.
NOTE:
Changing modes from PLAY to TEACH, during playback, will cause the program to cease
execution (similar to HOLD); to resume operation, press PLAY and then START.
Remote
This push button disables the playback panel and enables servo power to be
applied if play mode is set and positioner door is up.
Alarm/Error
The ALARM/ERROR indicator light turns ON whenever an alarm or error
condition occurs.
Emergency Stop (E-STOP)
The E-STOP button on the playback panel is connected in series with the system
Emergency Stop circuit. Pressing E-STOP ceases all system operation.
Start
Pressing the START button while in PLAY mode with servo power on, causes
playback execution of the current job to begin.
SERVO ON
READY
REMOTE
PLAY
(OFF)
(ON)
TEACH
MODE
EMERGENCY STOP
EDIT LOCK
ALARM
HOLD
START
MODE
BUTTONS
SERVO ON
READY
E-STOP
START
BUTTON
HOLD
BUTTON
REMOTE
MODE
ALARM/ERROR
INDICATOR
EDIT LOCK