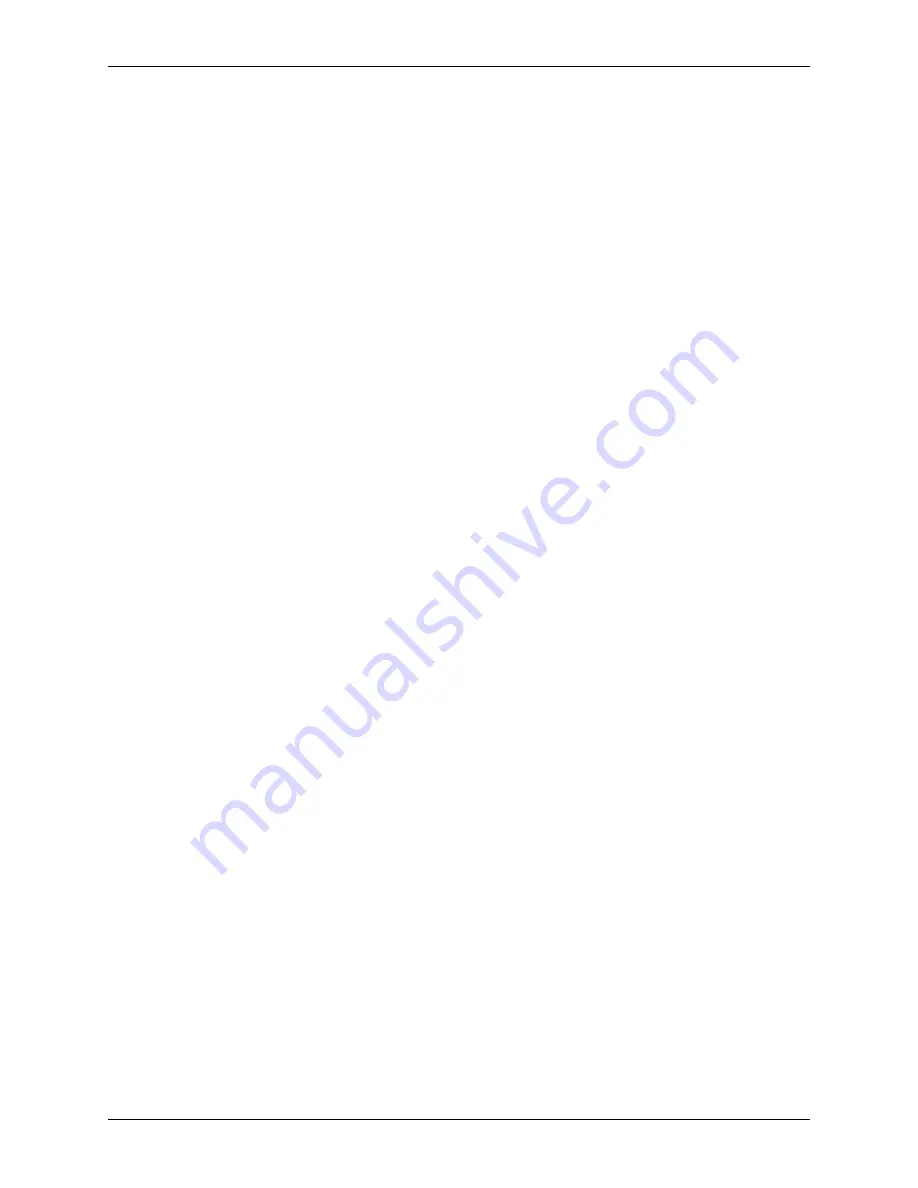
INTRODUCTION
ArcWorld II-200 System Manual
1-4
MOTO
MAN
1.4
Customer Service Information
If you are in need of technical assistance, contact the Motoman service staff at
(937) 847-3200. Please have the following information ready before you call:
•
Robot Type (UP6)
•
System Type (ArcWorld II-200)
•
Software Version (access using TOP KEY/SYSTEM INFO/VERSION/
SYSTEM on the programming pendant)
•
Robot Serial Number (located on the back side of the robot arm)
•
Robot Sales Order Number (located on front side of controller)