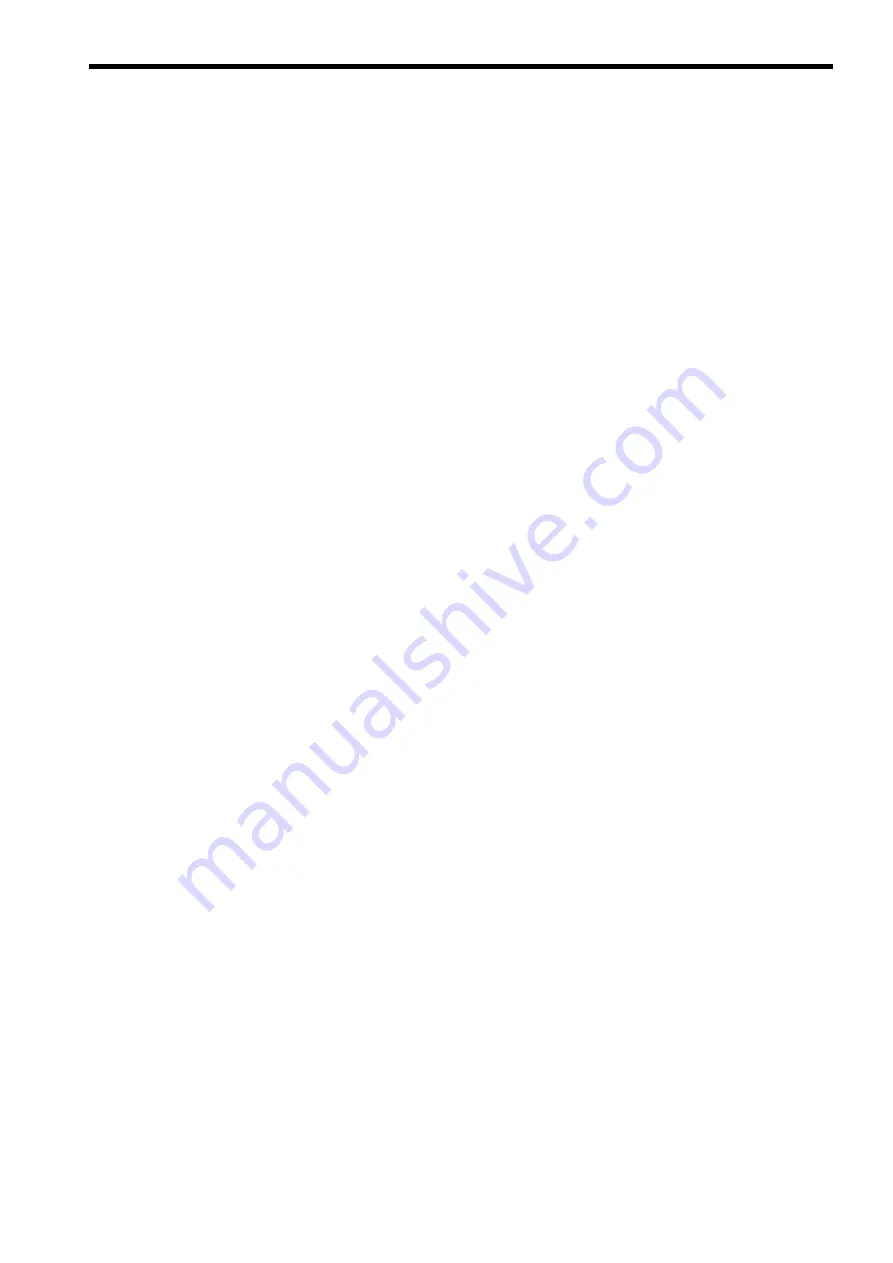
xvii
Appendix A Motion API
A.1 Motion API- - - - - - - - - - - - - - - - - - - - - - - - - - - - - - - - - - - - - - - - - - - - - - - - - - A-2
A.1.1 Common APIs - - - - - - - - - - - - - - - - - - - - - - - - - - - - - - - - - - - - - - - - - - - - - - - - - - - - - - - - A-2
A.1.2 Sequential APIs - - - - - - - - - - - - - - - - - - - - - - - - - - - - - - - - - - - - - - - - - - - - - - - - - - - - - - - A-2
A.1.3 System APIs- - - - - - - - - - - - - - - - - - - - - - - - - - - - - - - - - - - - - - - - - - - - - - - - - - - - - - - - - - A-4
Appendix B Parameters That are Automatically Updated
B.1 Parameters Updated when a Connection is Established
(MP2100/MP2100M to SERVOPACK) - - - - - - - - - - - - - - - - - - - - - - - - - - - - - - B-2
B.2 Parameters Updated when a Setting Parameter is Changed
(MP2100/MP2100M to SERVOPACK) - - - - - - - - - - - - - - - - - - - - - - - - - - - - - - B-3
B.3 Parameters Updated when a Motion Command is Started
(MP2100/MP2100M to SERVOPACK) - - - - - - - - - - - - - - - - - - - - - - - - - - - - - - B-4
B.4 Parameters Updated at Self-configuration
(SERVOPACK to MP2100/MP2100M) - - - - - - - - - - - - - - - - - - - - - - - - - - - - - - B-4
B.5 Parameters Updated at Self-configuration
(MP2100/MP2100M to SERVOPACK) - - - - - - - - - - - - - - - - - - - - - - - - - - - - - - B-5
Appendix C List of System Registers
C.1 System Service Registers - - - - - - - - - - - - - - - - - - - - - - - - - - - - - - - - - - - - - - -C-2
C.1.1 Registers Common to All Drawings - - - - - - - - - - - - - - - - - - - - - - - - - - - - - - - - - - - - - - - - - C-2
C.1.2 Registers Specific to High-speed Scan Drawings - - - - - - - - - - - - - - - - - - - - - - - - - - - - - - - - C-3
C.1.3 Registers Specific to Low-speed Scan Drawings - - - - - - - - - - - - - - - - - - - - - - - - - - - - - - - - C-4
C.2 Scan Execution Status and Calendar - - - - - - - - - - - - - - - - - - - - - - - - - - - - - - -C-5
C.3 Program Software Numbers and Remaining Program Memory Capacity - - - - - -C-5
INDEX
Revision History