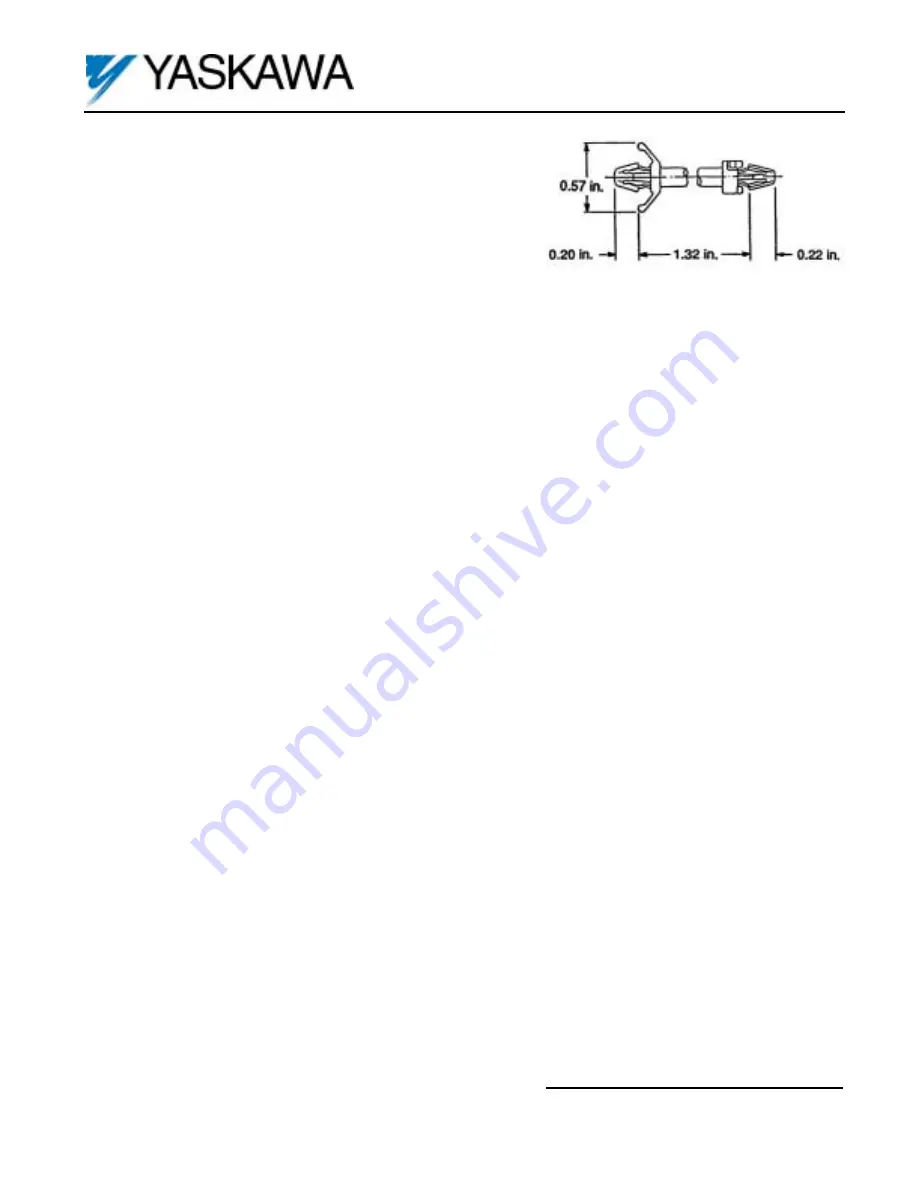
Yaskawa Electric America, Inc. – www.drives.com
IG.AFD.61, Page 2 of 6
Date: 07/01/04, Rev: 04-07
Dual Encoder Feedback Option Card
PG-W2
Figure 3. Mounting Spacer
6. Precautions and Preliminary Installation:
a. Remove contents from package. Verify that a mounting spacer is
included with the card. See Figure 3.
b. Disconnect all electrical power to the drive.
c.
Remove the drive’s front cover.
d. Check that the “CHARGE” indicator lamp inside the drive is off.
e. Use a voltmeter to verify voltage at incoming power terminals
(L1, L2, L3) has been disconnected.
f.
Insert the spacer into the mounting hole in the base of the drive,
just above the top edge of the control board. See Figure 2.
g.
Note:
When re-installing the cover, please take care not to pinch
any of the encoder wires.
h.
Important:
GPD 515/G5 models 20P2 to 22P2 and 40P2 to 41P5 have two closely spaced mounting holes. Insert
the spacer into the hole closest to the control board’s connector 4CN. If inserted in the wrong hole, the spacer WILL
NOT properly align with the PG-W2’s mounting hole.
7. PG-W2 Installation:
See Figure 2.
a. Position the bottom edge of the option card into the mounting bracket on the control board’s terminal block. Align the
two mounting holes in the card with the pins on the bracket.
b. Angle the top edge of the card into place, carefully aligning connector 4CN on the back of the card with connector
4CN on the control card. Gently press the card into place until 4CN and the spacer click into place.
8. Wiring:
Refer to Figure 4 and Tables 1 & 2. Make wire connections between the PG-W2 card and the encoder, the master
drive, and/or external monitoring circuits. Observe the following:
a. The need for the marker Z (C) channel depends on the installed custom (CASE) software. Standard software does
not use the marker pulse.
b. Keep the PG-W2 (i.e. control circuit) wiring separate from main circuit input/output wiring. A separate metallic
grounded conduit with ONLY the PG wiring running through it is preferred.
c.
To prevent erroneous operation caused by noise interference, use shielded cable for control signal wiring, and limit
the distance between the encoder and drive to 50 meters (165 feet) or less.
d. The recommended cable is twisted pair, 22 AWG, with overall shield, such as Belden 9504. Refer to “Electrical
Installation” in the drive technical manual for further information on use of shielded cable. The shielded sheath
connection points on the PG-W2 card are terminals 9, 16, & 23.
e. Strip back insulation for a distance of 0.22 inches on wire leads connected to the PG-W2 terminals.
f.
Connect the option card ground wire (TP1) to the drive’s ground terminal TB3 (12 for G5).
9. Jumper Setting:
The PG-W2 contains a jumper HDR1 (see Figure 1). The correct position of the jumper is software
specific. Please refer to the installed software manual for details.
10. Cover:
Reinstall and secure the drive front’s front cover.
11. Programming:
The programming of the drive will vary depending upon which software is loaded into the drive. The last 5
digits of the software number can be viewed in monitor U1-14.
12. Start-up:
Refer to Section 2 in the drive’s technical manual and the custom software instruction sheet for testing and start-
up information.
13. IG Storage:
Place this installation guide with the drive’s technical manual.