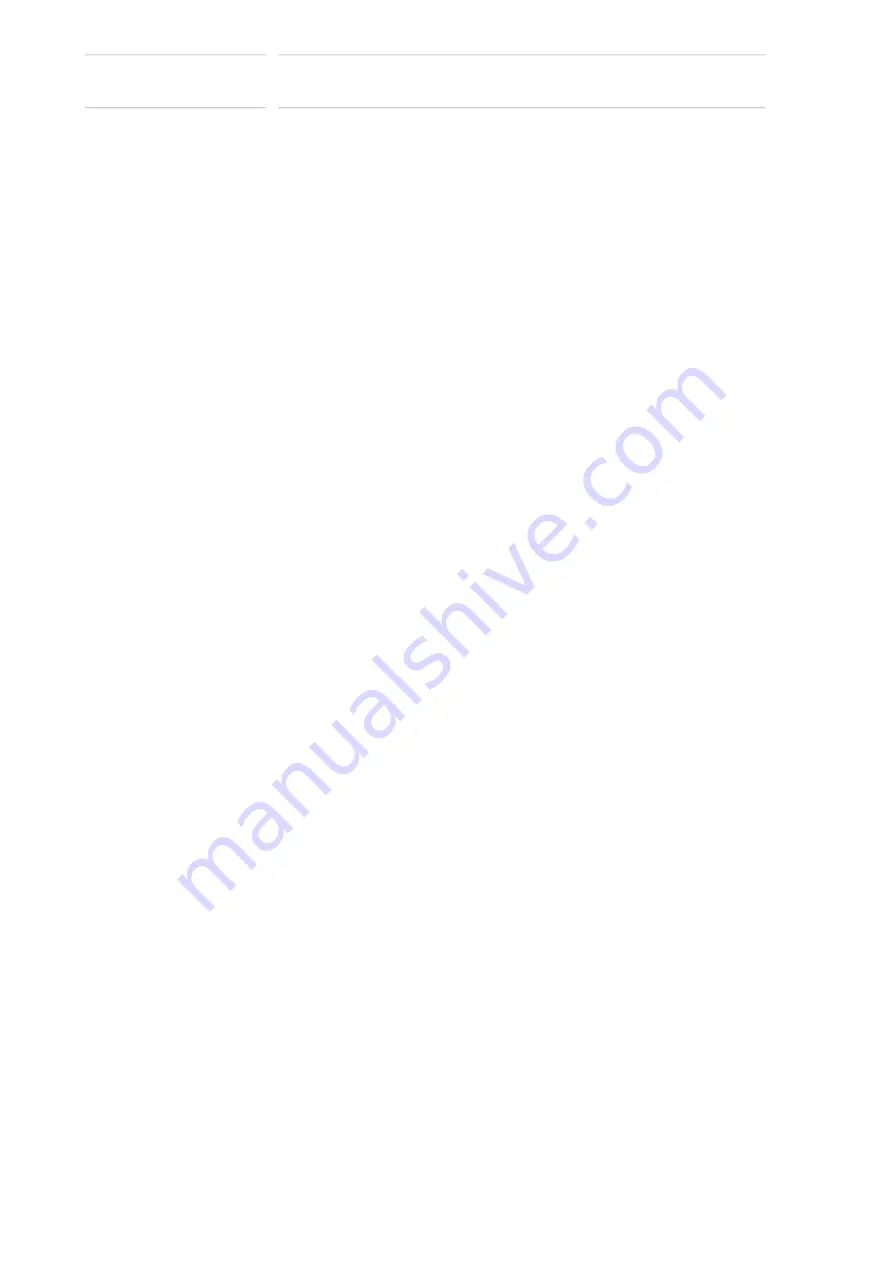
C-23
183523-1CD
183523-1CD
Appendix C
T
RM2-755-RDR Postioner
SLURBT
SLURBT are terms that YASKAWA Motoman uses to describe each axis
of the robot for convenience. The definition of each value is as follows:
S – Swing or Swivel
L – Lower Arm
U – Upper Arm
R – Rotate
B – Bend
T – Twist
Softlimit Setting Function
The Softlimit Setting Function is a function to set the axis travel limit range
of the Manipulator motion in software.
Speed and Separation Monitoring
Collaborative feature that allows both the operator and robot to work in
proximity to one another by ensuring the robot will slow down and stop
before a contact situation occurs. In order for this feature to be safely
implemented, functional safety and additional detection hardware must be
used. A risk assessment shall be used to determine if any additional
safeguarding is necessary to mitigate risks within the robot system.
Spline
A smooth, continuous function used to approximate a set of functions that
are uniquely defined on a set of sub-intervals. The approximating function
and the set of functions being approximated intersect at a sufficient
number of points to insure a high degree of accuracy in the approximation.
The purpose for the smooth function is to allow a robot Manipulator to
complete a task without jerky motion.
Spline Motion Type
A calculated path that the robot executes-that may be parabolic in shape.
A spline motion may also accomplish a free form curve with mixtures of
circular and parabolic shapes.
Standstill Monitoring
Using the Axis Speed Monitor function will activate an emergency stop
condition if a motion occurs.
Stop Position Monitoring
Sweep Axis
Positioner axis that sweeps back and forth
Swing Arm
Casting or weldment attached headstock or tailstock column containing
secondary axes
System Integrator
T
Tailstock
Positioner column containing the driven or idler side.
99 of 104