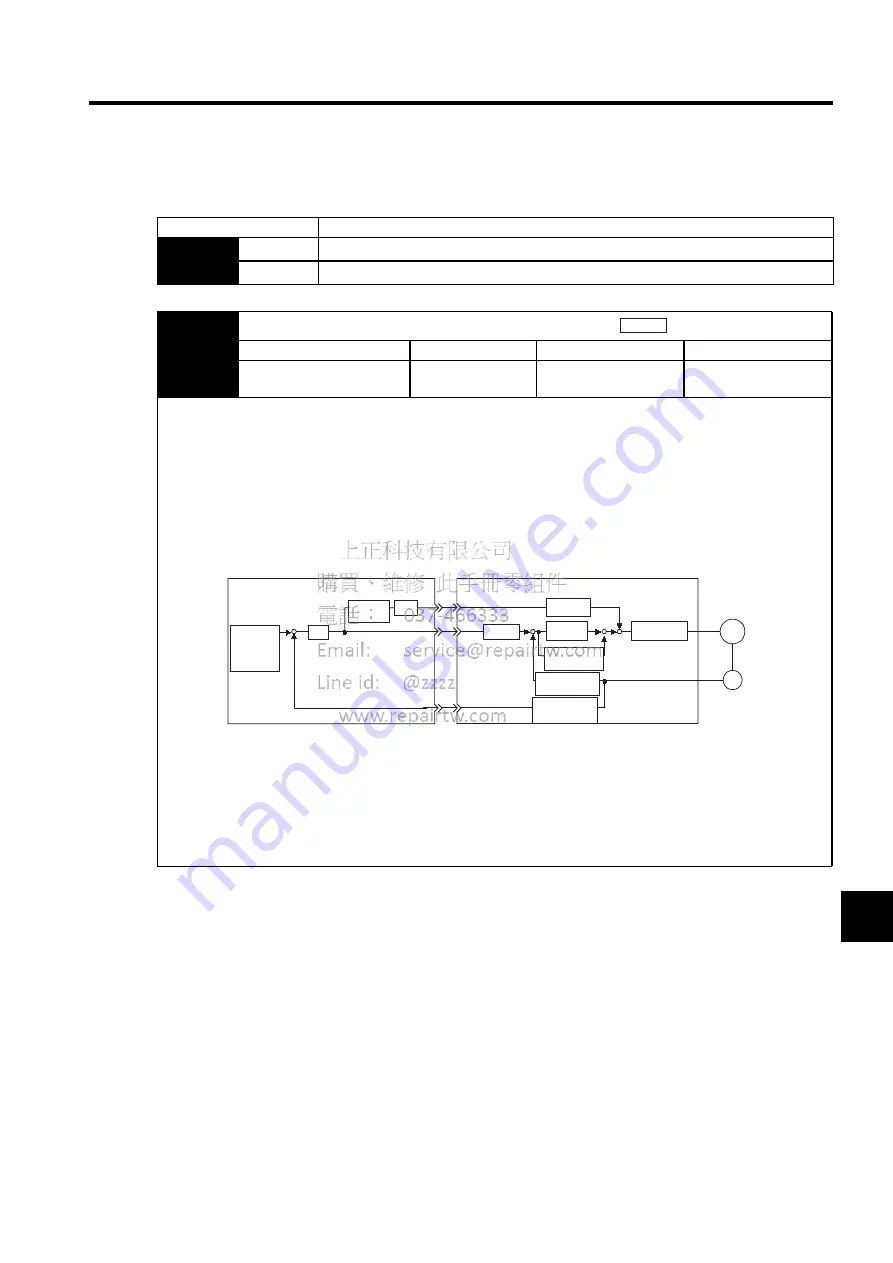
9.4 Servo Gain Adjustment Functions
9-15
9
9.4.2 Torque Feed-forward
Parameter
Meaning
Pn002
n.
0
Disabled
n.
2
Uses T-REF terminal for torque feed-forward input.
Pn400
Torque Reference Input Gain
Setting Range
Setting Unit
Factory Setting
Setting Validation
10 to 100
(1.0 to 10.0 V/rated torque)
0.1 V/rated torque
30
(3.0 V/rated torque)
Immediately
The torque feed-forward function is valid only in speed control (analog reference).
The torque feed-forward function shortens positioning time, differentiates a speed reference at the host controller to gener-
ate a torque feed-forward reference, and inputs the torque feed-forward reference together with the speed reference to the
SERVOPACK.
Too high a torque feed-forward value will result in overshooting or undershooting. To prevent such troubles, set the opti-
mum value while observing the system responsiveness.
Connect a speed reference signal line to V-REF (CN1-3 and -4) and a torque forward-feed reference to T-REF (CN1-1 and
-2) from the host controller.
Torque feed-forward is set using the parameter Pn400.
The factory setting is Pn400 = 30. If, for example, the torque feed-forward value is
±
3V, then, the torque is limited to
±
100% of the rated torque.
The torque feed-forward function cannot be used with torque limiting by analog voltage reference described in
8.9.3
Torque Limiting Using an Analog Voltage Reference
.
Speed
-
V-REF (CN1-3)
Position
reference
Kp
Pn100
Current loop
M
PG
Differ-
ential
K
FF
Speed
calculation
Integration
(Pn101)
+
+
+
+
+
T-REF (CN1-1)
Servomotor
Encoder
Host controller
SERVOPACK
Kp: Position loop gain
K
FF
: Feed-forward gain
+
+
Pn400
Pn300
-
Divider
Summary of Contents for SGDJ Series
Page 19: ...xix INDEX Revision History ...
Page 34: ...2 Selections 2 8 2 4 Selecting Cables CN4 c d e FG ...
Page 176: ...8 3 8 ...