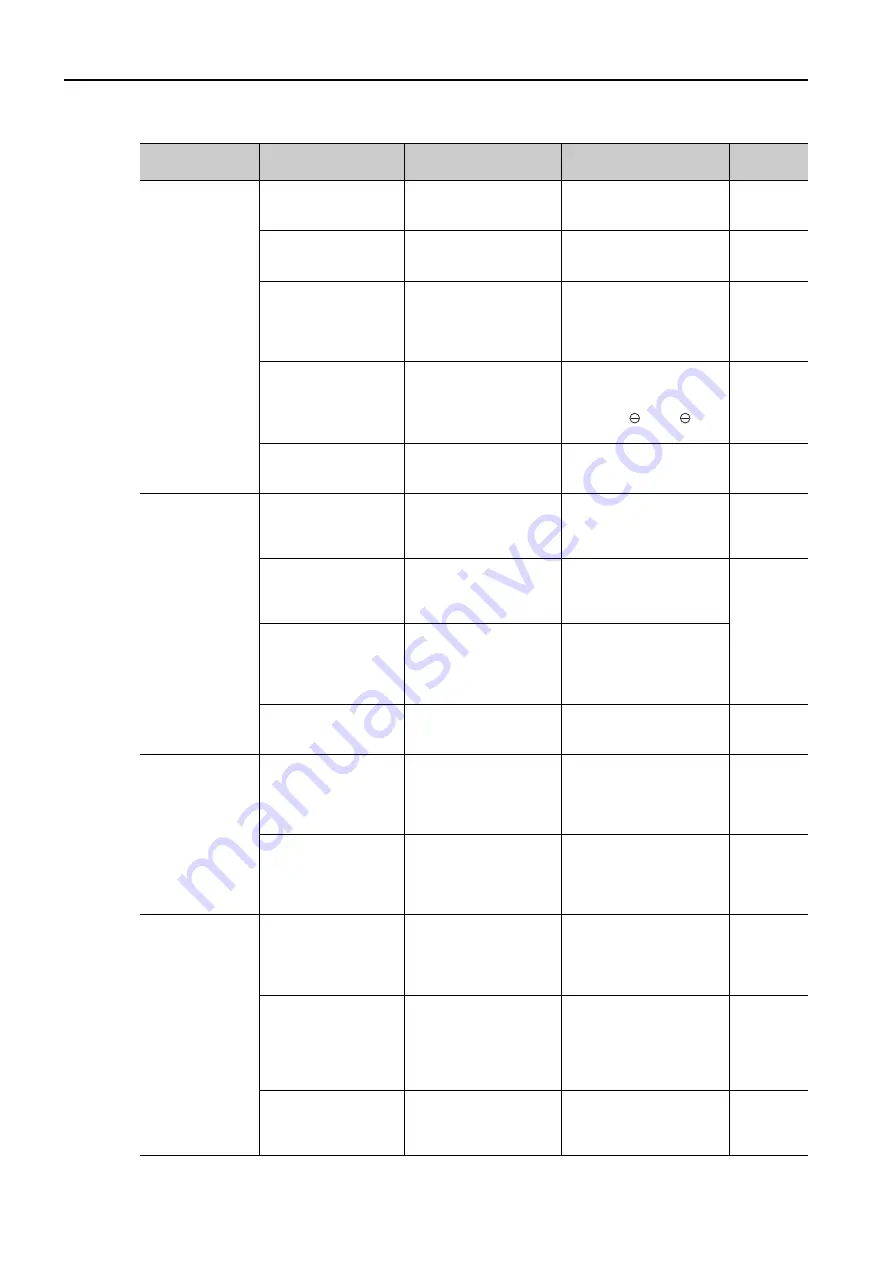
3.5 FT83 SERVOPACKs with Analog Voltage/Pulse Train References
3.5.3 Troubleshooting Alarms
3-218
A.410:
Undervoltage
(Detected in the
main circuit
power supply
section of the
SERVOPACK.)
The power supply
voltage went below
the specified range.
Measure the power
supply voltage.
Set the power supply volt-
age within the specified
range.
–
The power supply
voltage dropped
during operation.
Measure the power
supply voltage.
Increase the power supply
capacity.
–
A momentary power
interruption occurred.
Measure the power
supply voltage.
If you have changed the
setting of Pn509 (Momen-
tary Power Interruption
Hold Time), decrease the
setting.
*1
The SERVOPACK
fuse is blown out.
–
Replace the SERVO-
PACK and connect a
reactor to the DC reactor
terminals (
1 and
2) on
the SERVOPACK.
–
A failure occurred in
the SERVOPACK.
–
The SERVOPACK may be
faulty. Replace the SER-
VOPACK.
–
A.510:
Overspeed
(The motor
exceeded the
maximum speed.)
The order of phases
U, V, and W in the
motor wiring is not
correct.
Check the wiring of the
Servomotor.
Make sure that the Servo-
motor is correctly wired.
–
A reference value that
exceeded the over-
speed detection level
was input.
Check the input refer-
ence.
Reduce the reference
value. Or, adjust the gain.
*1
The motor exceeded
the maximum speed.
Check the waveform of
the motor speed.
Reduce the speed refer-
ence input gain and
adjust the servo gain. Or,
reconsider the operating
conditions.
A failure occurred in
the SERVOPACK.
–
The SERVOPACK may be
faulty. Replace the SER-
VOPACK.
–
A.511:
Encoder Output
Pulse Overspeed
The encoder output
pulse frequency
exceeded the limit.
Check the encoder out-
put pulse setting.
Decrease the setting of
Pn212 (Encoder Output
Pulses) or Pn281
(Encoder Output Resolu-
tion).
*1
The encoder output
pulse frequency
exceeded the limit
because the motor
speed was too high.
Check the encoder out-
put pulse setting and
the motor speed.
Reduce the motor speed.
–
A.520:
Vibration Alarm
Abnormal oscillation
was detected in the
motor speed.
Check for abnormal
motor noise, and check
the speed and torque
waveforms during oper-
ation.
Reduce the motor speed.
Or, reduce the setting of
Pn100 (Speed Loop
Gain).
*1
The setting of Pn103
(Moment of Inertia
Ratio) is greater than
the actual moment of
inertia or was greatly
changed.
Check the moment of
inertia ratio or mass
ratio.
Set Pn103 (Moment of
Inertia Ratio) to an appro-
priate value.
*1
The vibration detec-
tion level (Pn312 or
Pn384) is not suitable.
Check that the vibra-
tion detection level
(Pn312 or Pn384) is
suitable.
Set a suitable vibration
detection level (Pn312 or
Pn384).
*1
Continued on next page.
Continued from previous page.
Alarm Number:
Alarm Name
Possible Cause
Confirmation
Correction
Reference