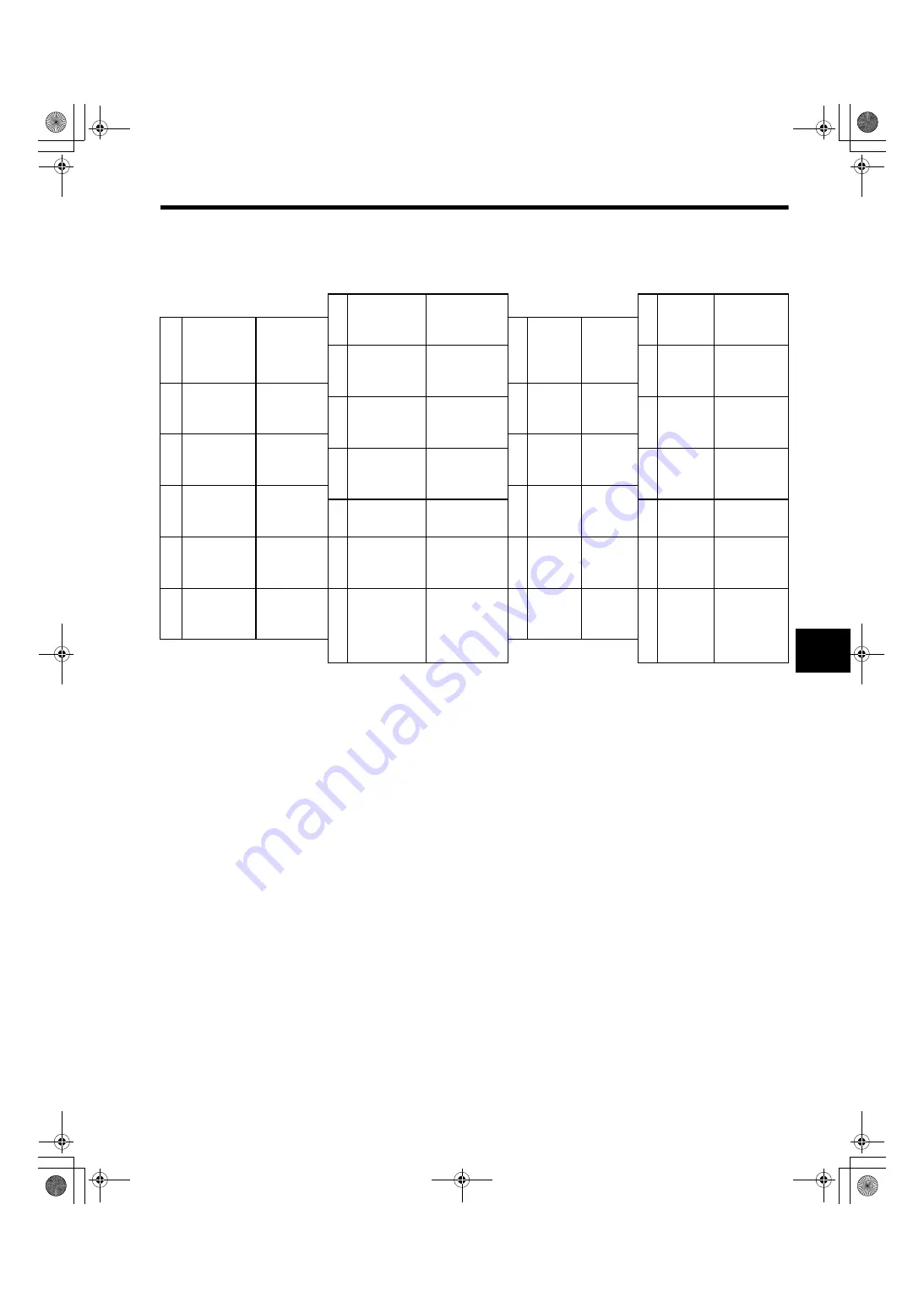
5.3 Examples of I/O Signal Connections
5-9
5
5.3.2 I/O Signal Connector (CN1) Terminal Layout
Note: 1. Do not use unused terminals for relays.
2. Connect the shield of the I/O signal cable to the connector shell.
Connect to the FG (frame ground) at the SERVOPACK-end connector.
1
+24VIN
External input
power supply
14 ALM-
Servo alarm
signal output
-
2
CCW-OT
CCW run
prohibit
signal
15 MS_G
Module
status
output
(green)
3
CW-OT
CW run
prohibit signal
16 MS_R
Module
status output
(red)
4
HOME
Home signal
input
17 MS-COM Module
status
common
5
External stop
signal input +
18 NS_G
Network
status output
(green)
6
EXSTOP-
External
stop signal
input -
19 GND
Ground
7
USER0
User input
signal 0
20 NS_COM Network
status
common
8
USER1
User input
signal 1
21 ENC_A+ External
encoder
A
9
USER+
User signal
22 ENC_A-
External
encoder A
10 USER
User signal
output -
23 ENC_B+ External
encoder
B
11 BRK+
Brake signal
24 ENC_B-
External
encoder B
12 BRK-
Brake signal
output -
25 ENC_C+ External
encoder
C
13 ALM+
Servo alarm
signal
26 ENC_C-
External
encoder C
SIEPS80000025.book 9 ページ 2004年10月25日 月曜日 午前11時57分