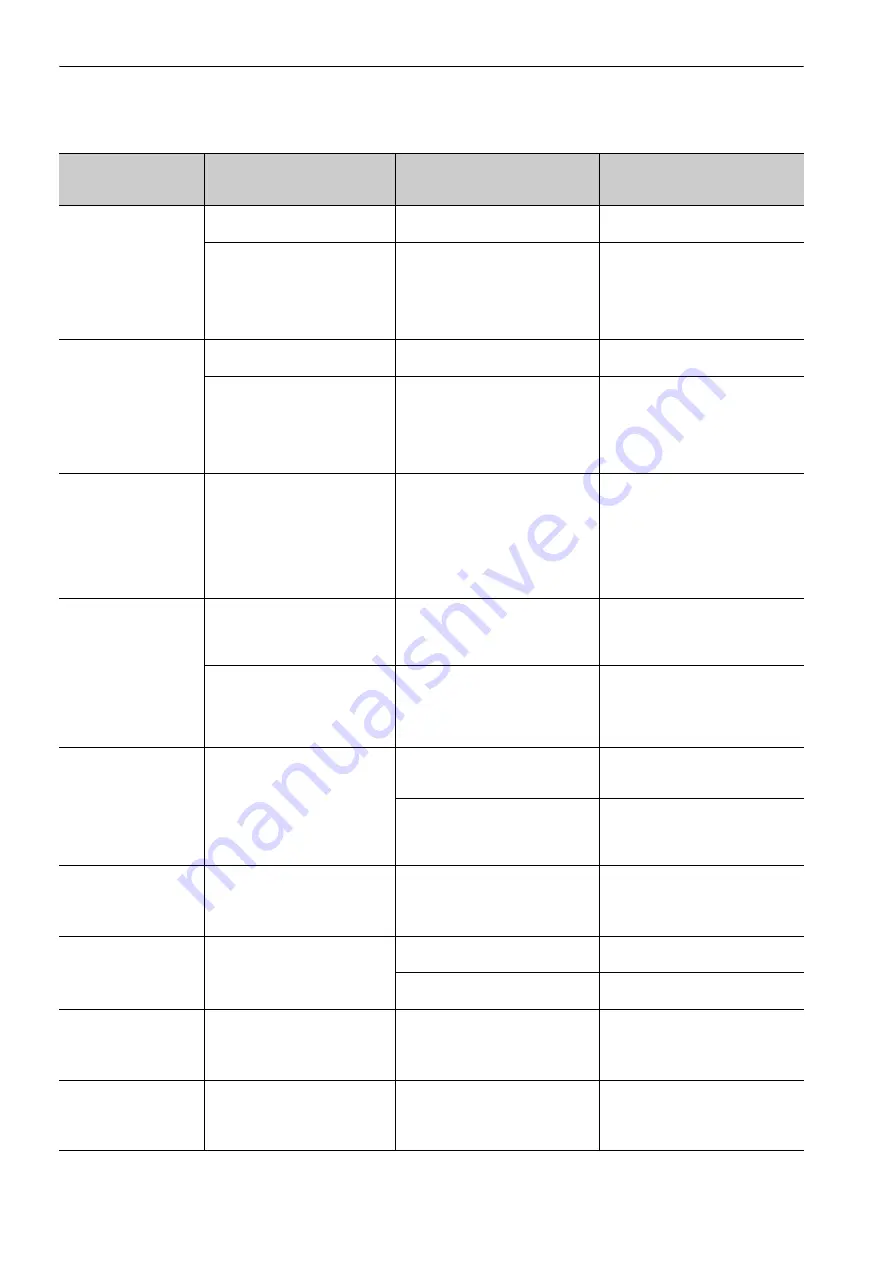
8 Troubleshooting
8.1.2 Troubleshooting of Alarms
8-20
A.E61:
MECHATROLINK
Transmission Cycle
Error
(Synchronization
interval error)
MECHATROLINK transmission
cycle fluctuated.
Check the MECHATROLINK
transmission cycle setting.
Remove the cause of transmission
cycle fluctuation at host controller.
A fault occurred in the multi-
winding drive unit or SERVO-
PACK.
−
Turn the control power supply OFF
and ON again. If the alarm still
occurs, the multi-winding drive unit
or SERVOPACK may be faulty.
Replace the multi-winding drive
unit or SERVOPACK.
A.EA2:
DRV Alarm 2
(SERVOPACK WDT
error)
MECHATROLINK transmission
cycle fluctuated.
Check the MECHATROLINK
transmission cycle setting.
Remove the cause of transmission
cycle fluctuation at host controller.
A fault occurred in the multi-
winding drive unit or SERVO-
PACK.
−
Turn the control power supply OFF
and ON again. If the alarm still
occurs, the multi-winding drive unit
or SERVOPACK may be faulty.
Replace the multi-winding drive
unit or SERVOPACK.
A.Eb1:
Safety Function Signal
Input Timing Error
The lag between activations of
the input signals /HWBB1 and
/HWBB2 for the HWBB function
is ten second or more.
Measure the time lag between the /
HWBB1 and /HWBB2 signals.
The output signal circuits or devices
for /HWBB1 and /HWBB2 or the
multi-winding drive unit input sig-
nal circuits may be faulty. Alterna-
tively, the input signal cables may
be disconnected. Check if any of
these items are faulty or have been
disconnected.
A.Ed0
:
Internal Command
Error
A parameter was edited from a
digital operator or personal com-
puter during MECHATROLINK-
II communications.
Check the procedure for editing
parameters.
Do not edit parameters from a digi-
tal operator or personal computer
during MECHATROLINK-II com-
munications.
A fault occurred in the SERVO-
PACK.
–
Turn the control power supply OFF
and ON again. If the alarm still
occurs, the SERVOPACK may be
faulty. Repair or replace the SER-
VOPACK.
A.Ed1:
Command Execution
Timeout
A timeout error occurred when
using a MECHATROLINK com-
mand.
Check the motor status when the
command is executed.
Execute the SV_ON or SENS_ON
command only when the motor is
not running.
For fully-closed loop control, check
the status of the external encoder
after an output is made to execute
the command.
Execute the SENS_ON command
only when an external encoder is
connected.
A.EE0
:
Local Communica-
tions Servo OFF Oper-
ation Error 1
The servo was not turned OFF for
all axes within 1 second after the
servo OFF request.
–
Perform an alarm reset and restart
operation.
A.EE1
:
Local Communica-
tions Servo ON Oper-
ation Error 1
The servo was not turned ON for
all axes within 1 second after the
servo ON request.
Check to see if the multi-winding
drive unit is in ready status.
Perform an alarm reset and restart
operation.
Check to see if the motor is stopped.
Perform an alarm reset and restart
operation.
A.EE2
:
Local Communica-
tions Servo ON Oper-
ation Error 2
Servo ON status could not be
detected for all axes during servo
ON status.
Check to see if the multi-winding
drive unit is in ready status.
Perform an alarm reset and restart
operation.
A.EE3
:
Local Communica-
tions Servo OFF Oper-
ation Error 2
Servo OFF status could not be
detected for all axes during servo
OFF status.
–
Perform an alarm reset and restart
operation.
(cont’d)
Alarm Number:
Alarm Name
(Alarm Description)
Cause
Investigative Actions
Corrective Actions