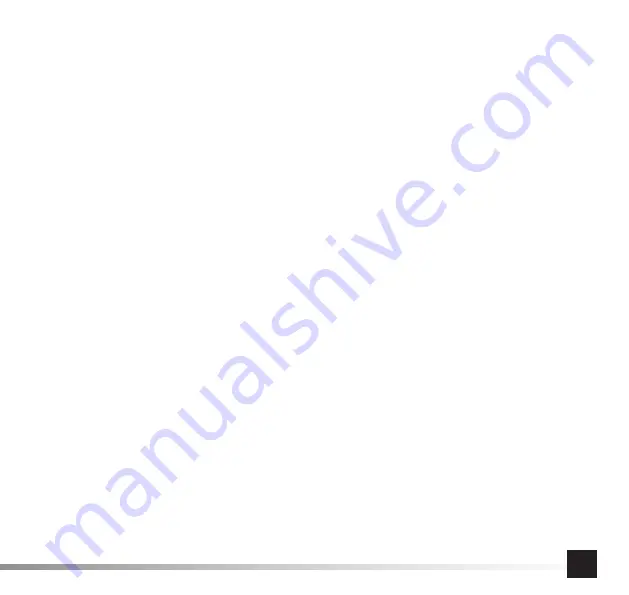
13
GB
O R I G I N A L I N S T R U C T I O N S
During cutting or demolition works, elements of material processed
may be thrown away.
It is forbidden to hold the toll inserted with bare hand. This may be a
cause of injuries due to oscillations.
USING TOOL
Make sure before each use that none element of pneumatic system
is damaged. In case any damages are found, immediately replace
with new defect-free system components.
Before each use of pneumatic system, moisture condensed inside
the tool, compressor and cables should be dried out.
Connecting the tool to pneumatic system
Drawing shows the recommended method of connecting the tool to
pneumatic system. Method presented will ensure the most eff ective
use of tool and also will prolong its service life.
Insert few drops of oil of SAE 10 viscosity, to air inlet.
Screw in to the thread of air inlet the proper tip that allows connect-
ing air supply hose, tightly and securely. (II)
Attach proper tip on the tool driver.
When working with pneumatic
tools use only accessories adjusted to work with impact tools.
Wherever possible, adjust the pressure (torque).
Connect the tool to pneumatic system using a hose with internal
diameter of 10 / 3/8”. Make sure the strength of hose is at least
1.38MPa. (III)
Start the tool for few seconds making sure that no suspicious sounds
or oscillations may be found.
Assembly of accessories (IV)
Attach the selected tool in tool chuck.
Rewound the spring around the thread so that the fl ange on tool
inserted leaned on the wire handle, preventing the tool from sliding
out from the tool chuck. Tighten the spring fi rmly and securely.
Work with hammer
Select the right tool for particular type of work.
Put only such pressure to the tool, which is required for particular
work. Do not put excessive pressure on the object being processed,
this may lead to cracking of tool inserted and serious injuries. When
processing metal sheet pay attention to sharp edges that may
emerge during cutting. Also pay attention to fragments that may be
torn off while processing. Do not let them pose any threat at the
work place.
MAINTENANCE
Never use gasoline, solvent or any other fl ammable liquid for clean-
ing the tool. Vapours may ignite, causing an explosion and serious
injuries.
Solvents used for cleaning the tool chuck and body may cause sof-
tening of sealing. Thoroughly dry the tool before the work.
In case any irregularities in operation of tool are found, disconnect
the tool immediately from the pneumatic system.
All components of pneumatic system must be protected against con-
taminants. Contaminants that penetrate into pneumatic system may
damage the tool and other components of pneumatic system.
Tool maintenance before each use
Disconnect the tool from pneumatic system.
Before each use, insert small quantity of preserving liquid (e.g. WD-
40) through the air slot.
Connect the tool to pneumatic system and start it for approx. 30
seconds. This will allow distributing the preserving fl uid inside the
tool and clean it.
Again disconnect the tool from pneumatic system.
Insert small quantity of SAE 10 oil into the inside of tool, through the
air slot and slots designed for this purpose. It is recommended to use
SAE 10 oil designed for maintenance of pneumatic tools. Connect
the tool and start it for a short period of time.
Note! WD-40 may not be used as the regular lubricating oil.
Wipe the excess of oil that got out through outlet slots. Oil left may
damage the sealing of the tool.
Other maintenance actions
Check before each use, if any traces of damage may be found on
the tool. Drivers, tool chucks and spindles must be kept clean.
Every 6 months or after 100 hours of service deliver the tool to repair
workshop for inspection by qualifi ed staff . If the tool was used with-