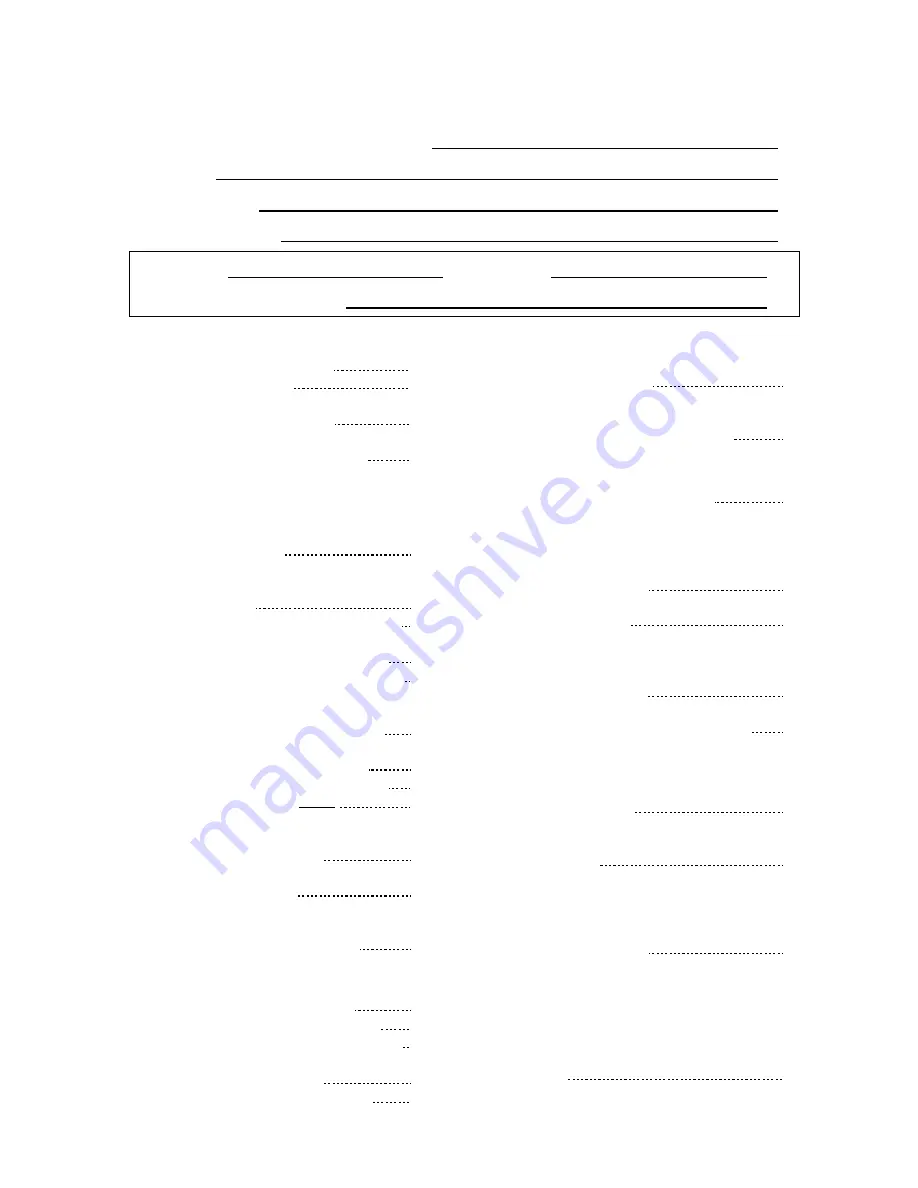
27
YAZAKI CH-MG SERIES CHILLER-HEATER
INSTALLATION CHECK AND REQUEST FOR START-UP
Yazaki Authorized Service Provider:
Address:
Project Name:
Project Address:
A. CHILLER-HEATER
1. Unit placed on foundation
□
2. Unit leveled properly
□
3. Service clearance provided on all
sides and top
(40 in. front)
□
4. Chiller-heater anchored by L-Anchor
plates to foundation
(if required)
□
*Anchors may be required by some state and local codes.
B. WATER PIPING
1. Chilled/hot water piping installed
between chiller-heater, pumps and
air handling unit(s)
□
2. Cooling water piping installed
between chiller-heater, pumps, and
cooling tower
□
3. Water piping leak tested and flushed
□
4. System filled with water and glycol
(if required)
and trapped air vented
□
5. Flow setters installed in water piping
□
6. Test plugs
(Pete’s plugs)
and/or
thermowells installed in the inlet and
outlet piping of each chiller-heater
□
7. Valves installed at each chiller-heater
for flow balancing and isolation
□
8. Air vent valves installed on piping
□
9. Strainers present and clean
□
10. Expansion tank
(properly charged)
and
water make-up piping installed to
chilled/hot water system
□
11. Water make-up and fill lines installed
to the cooling tower
□
12. Pressure relief valves, set at 113.8 psig
(max.)
installed on piping adjacent to
each chiller-heater
(if required)
□
C. GAS PIPING
1. Natural Gas supply is available to unit
between 7” wc and 10.5” wc
□
2. Gas piping installation completed
□
3. Gas cock and sediment trap installed
□
4. Appliance regulator installed at each
chiller- heater
(if required)
□
5. Gas pipe leak tested and purged
□
D. VENTING
1. Factory-provided vent cap installed
(outdoor installation)
□
2. Barometric damper and Type-B vent
extension installed on each chiller-
heater outlet
(indoor installation)
□
E. POWER WIRING
1. Power supply as indicated on the UNIT
NAMEPLATE, is connected
□
2. Wiring completed between the chiller-
heater, motor contactors and/or starters
for the following : Chilled/hot water
pump, cooling water pump and
cooling tower fan
□
3. Rotation of each external pump and fan
motor checked
□
4. Power supply wiring connected
between a fused disconnect and
each chiller-heater. (DO NOT operate
the chiller-heater)
□
5. Power supply available near the
chiller-heater for a vacuum pump
□
F. CONTROL WIRING
1. Motor contactors, starters, and/or
manual controllers installed for all
external motors
□
2. Control wiring installed between
chiller-heater and pump/motor
contactors
□
3. Interlock wiring installed between
chiller-heater and thermal overloads
on the following motors: Chilled/hot
water pump, cooling water pump and
cooling tower fan
□
G. CONDITIONS
1. Personnel available to assist with
start-up who are familiar with the
system and have appropriate tools
(adequate vacuum pump, combustion
analyzer, vacuum gauge, proper hoses,
etc.)
□
Model No: Serial No:
Anticipated Startup Date:
Summary of Contents for AROACE CH-MG150
Page 4: ...4 EQUIPMENT DIMENSIONS Figure 1 MG150 Dimensions ...
Page 5: ...5 EQUIPMENT DIMENSIONS Figure 2 MG200 Dimensions ...
Page 6: ...6 INTERNAL WIRING DIAGRAM ...
Page 7: ...7 ...
Page 8: ...8 Table 2 Internal Wiring Diagram Legend KRCH relay has been replaced by the KCH relay ...
Page 12: ...12 INSTALLATION CLEARANCES Figure 7 Installation and Service Clearances ...