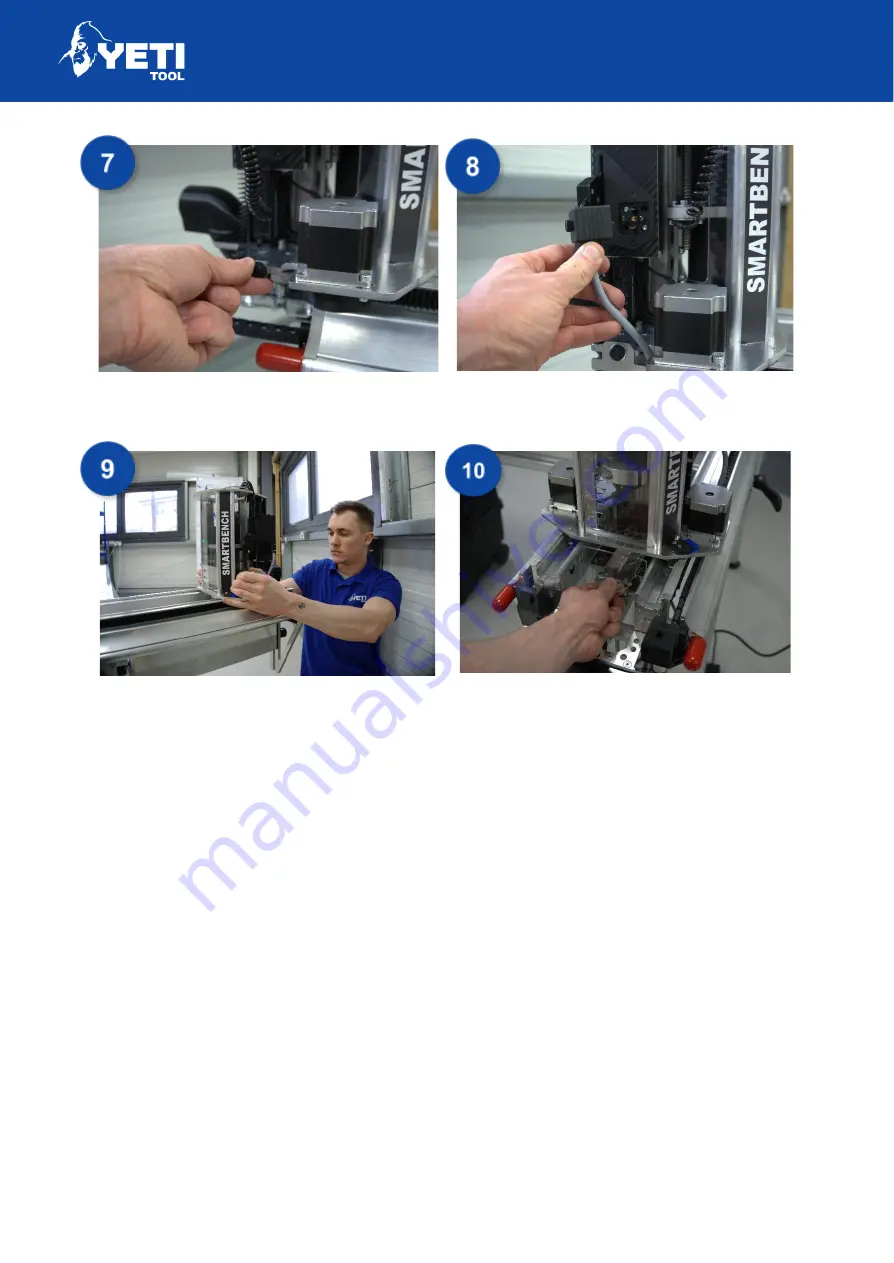
SMARTBENCH V1.3 – STANDARD, PRECISION AND PRECISIONPRO
Secure this in place with the thumbscrew
provided.
Plug in the power cable and secure it with
the thumbscrew.
You can now push the
Z Head
onto the
Upper X Beam
until all wheels are
engaged. If you do not push the Z-Head
further onto the Upper beam the motors
will not be engaged with the rack.
Fit the dust shoe plug into the front of the
dust shoe. This can be made easier when
it is over the bench so you have a flat
surface as a base.
Unit 12 Old Mill Road | Portishead | Bristol | BS20 7BX | UK
14
Summary of Contents for SMARTBENCH V1.3
Page 1: ......