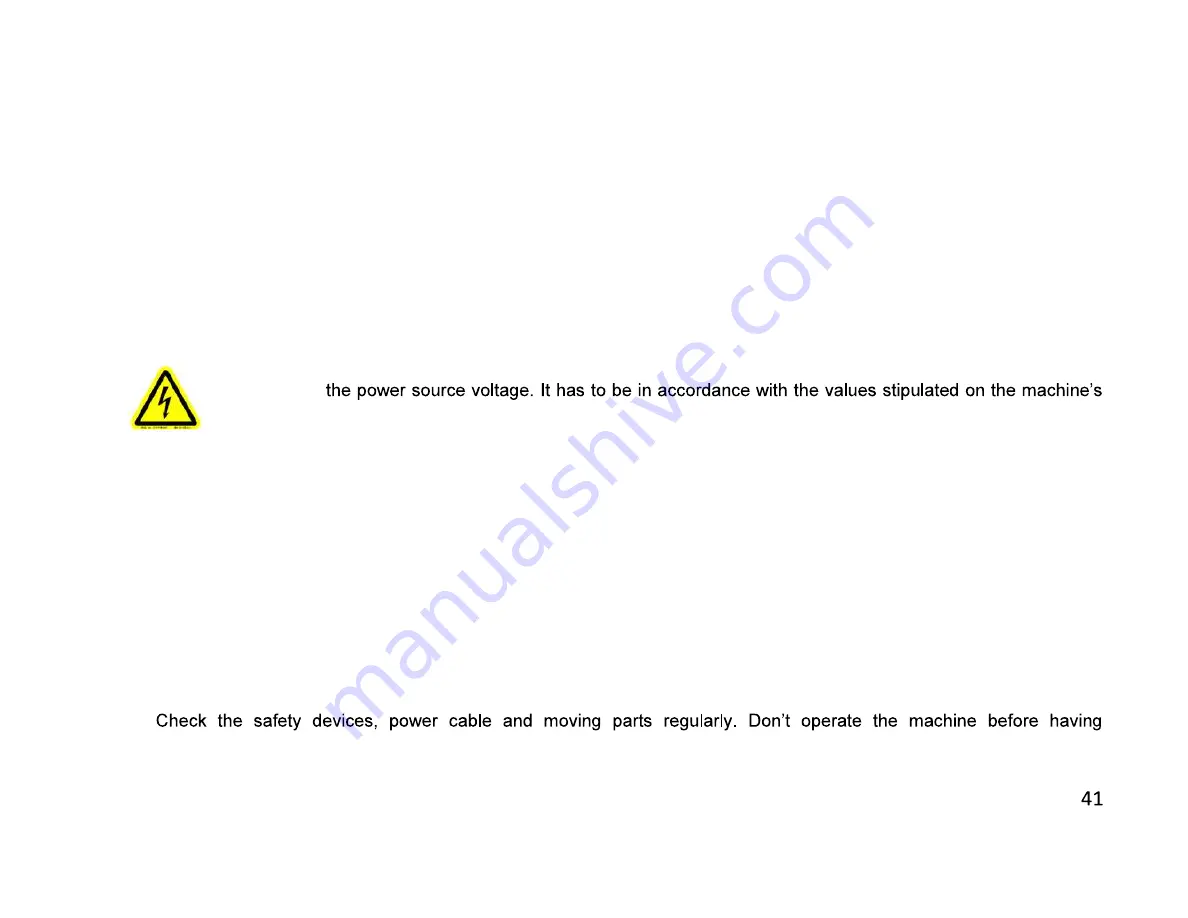
5.2 Connecting to Power Source
5.2.1
The Electrical connection must be made by a licensed electrician
5.2.2
The power outlet socket on the machine should be available.
5.2.3
Plug the machine to a grounded socket.
5.2.4
Main voltage of the machine is optional as 230 V 50 Hz or 400 V 50 Hz.
5.2.5
Check
type label
5.2.6
After electrical connection is made, machine must be operated in idle running and it must be controlled whether
rotation directions of cutting tools are correct or not and if the rotation direction is wrong, appropriate connection
must be made
6. MACHINE SAFETY INFORMATION
6.1
Lifting, installation, electric maintenance of the machine should be carried out by qualified personnel only.
6.2
Routine maintenance and scheduled maintenance should be carried out by qualified personnel after unplugging
the
machine and disconnecting the air supply first.
6.3
Ensure that the machine has been cleaned, tested and maintain before starting to operate.
6.4
replaced defective safety devices or faulty parts.
Summary of Contents for CA 601
Page 4: ...BOYUTLAR DIMENSIONS FIGURE ...
Page 5: ... PART LIST FIGURE FIGURE ...
Page 6: ... FIGURE FIGURE ...
Page 7: ... FIGURE ...
Page 9: ...NO PART NO PICTURE STOK KODU CODE 1 1EL020000 0012 2 3 4 ...
Page 10: ...5 6 7 8 ...
Page 19: ......
Page 20: ......
Page 30: ...ELECTRIC PNEUMATIC ...
Page 31: ...3 PHASE ELECTRICAL DIAGRAM SHEET 1 ...
Page 32: ...3 PHASE ELECTRICAL DIAGRAM SHEET 2 ...
Page 33: ...3 PHASE ELECTRICAL DIAGRAM SHEET 3 ...
Page 34: ...3 PHASE ELECTRICAL DIAGRAM SHEET 4 ...
Page 35: ...PNEUMATIC DIAGRAM SHEET 1 ...