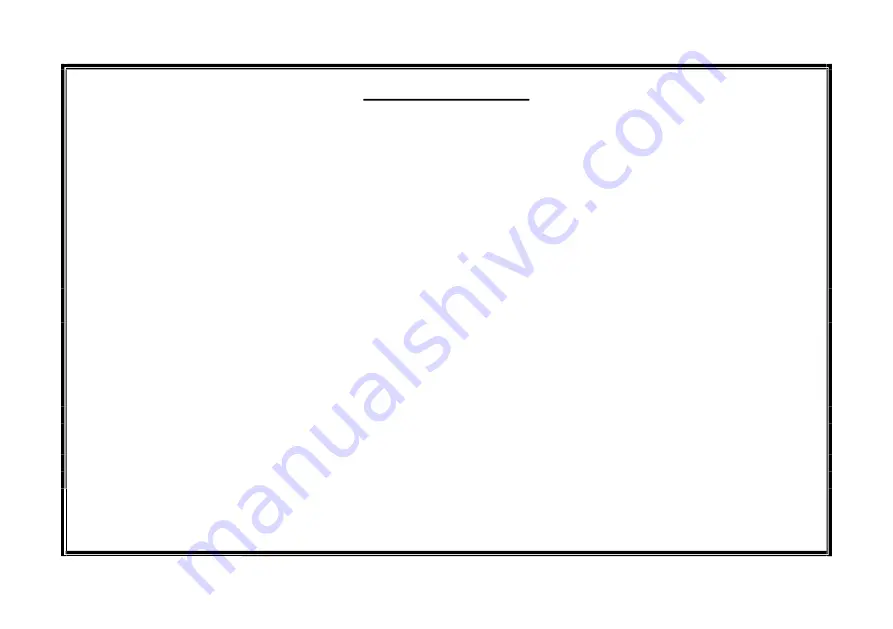
1
GARANTİ BELGESİ
İMALATÇI FİRMA
:
YILMAZ MAKİNE SANAYİ VE TİCARET A.Ş.
ADRES
:
TAŞDELEN MH. ATABEY CD. No 9 34788 ÇEKMEKÖY
İSTANBUL-TÜRKİYE
TELEFON
:
0216.312.28.28 PBX
TELEFAX
:
0216.484.42.88
İMZA-KAŞE
:
ÜRÜNÜN CİNSİ
:
ALÜMİNYUM VE PVC KESME MAKİNESİ
MARKASI
:
YILMAZ
MODEL KODU
:
KD 350 / KD 400 M-D-P
BANDROL/SERİ NO
:
TESLİM TARİHİ
:
GARANTİ SÜRESİ
:
2 YIL
AZAMİ TAMİR SÜRESİ
:
30 İŞ GÜNÜ
YETKİLİ SATICI FİRMA
:
ADRES
:
TELEFON
:
TELEFAX
:
İMZA-KAŞE
:
Summary of Contents for KD 350 M-D-P
Page 2: ...5 KESME DİYAGRAMI CUTTING DIAGRAM ДИАГРАММА ВЫПИЛИВАНИЯ KD 350 M D P ...
Page 3: ...6 KD 400 M D P ...
Page 4: ...7 ELEKTRİK ŞEMASI WIRING DIAGRAM ДИАГРАММА ЭЛЕКТРОПРОВОДКИ 230V 1P ...
Page 5: ...8 400V 3P ...
Page 6: ...9 BOYUTLAR DIMENSIONS РАЗМЕРЫ ...
Page 7: ...10 PARÇA LİSTESİ PART LIST ПЕРЕЧЕНЬ ДЕТАЛЕЙ RESİM FIGURE РИСУНОК 1 ...
Page 8: ...11 RESİM FIGURE РИСУНОК 2 ...
Page 33: ...74 ELECTRIC PNEUMATIC DİAGRAM ...
Page 34: ...75 3 PHASE ELECTRICAL DIAGRAM SHEET 1 ...
Page 35: ...76 1 PHASE ELECTRICAL DIAGRAM SHEET 1 ...
Page 36: ...77 PNEUMATIC DIAGRAM SHEET 1 ...