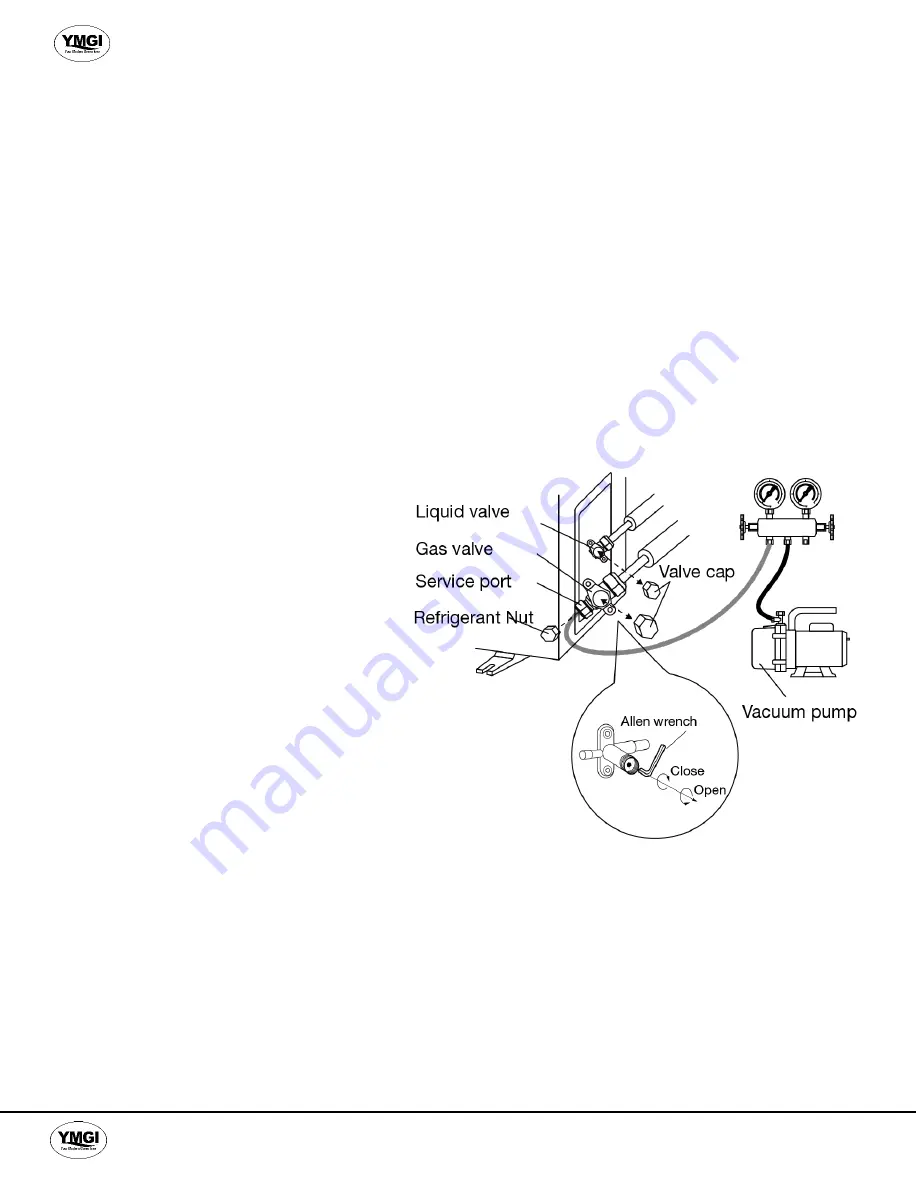
YMGI: Your Modern Green Idea
YMGI, Engineered Comfort Products for A Sustainable and Efficient Green World!
39
TESTING AND INSPECTION
Vacuum Procedure
Important:
Use a quality Micron Gauge to measure and validate the proper system vacuum level achieved. Do not rely on the scale
of a
“bourbon tube” type gauge set to validate the depth and quality of the vacuum.
1. Remove the caps of the liquid valve, gas valve and service port.
2. Connect gauge manifold and micron gauge to the service ports provided at the liquid and suction service valves.
3. Connect a vacuum pump to the manifold gauge.
4. Open the lower pressure side of the manifold valve assembly and start the vacuum pump.
The switch at the high pressure side of the manifold valve assembly should be kept closed, or evacuation does
not fail.
5. Operate vacuum pump until a vacuum of 500 microns or less is achieved.
The evacuation
duration depends on the vacuum pump size and unit’s capacity, generally 20 minutes for the
9,000 Btu/H units, to 1 hour for a larger 36,000 Btu/H unit.
6. Close the manifold valves and shut off the
pump.
a. If vacuum holds below 700 microns for
15 minutes, the system can be
considered dry and leak free. Go to
step 5.
b. If vacuum increases to 800 microns or
greater, this is an indication of moisture
in system or a leak exists. Identify leak
and repair as necessary, after which
repeat steps 4 and 5.
If moisture is suspect, purge system
use triple evacuation method using dry
nitrogen.
8.
Confirm that manifold valves are closed and
disconnect the vacuum pump.
9.
Open the service valves to the
fully ‘back-
seat’ position to let the refrigerant flow to
the indoor unit and balance the pressure in
system.
Note:
Do not allow air to enter the connection pipe when removing the hose.
10.
Replace service valve caps and tighten.