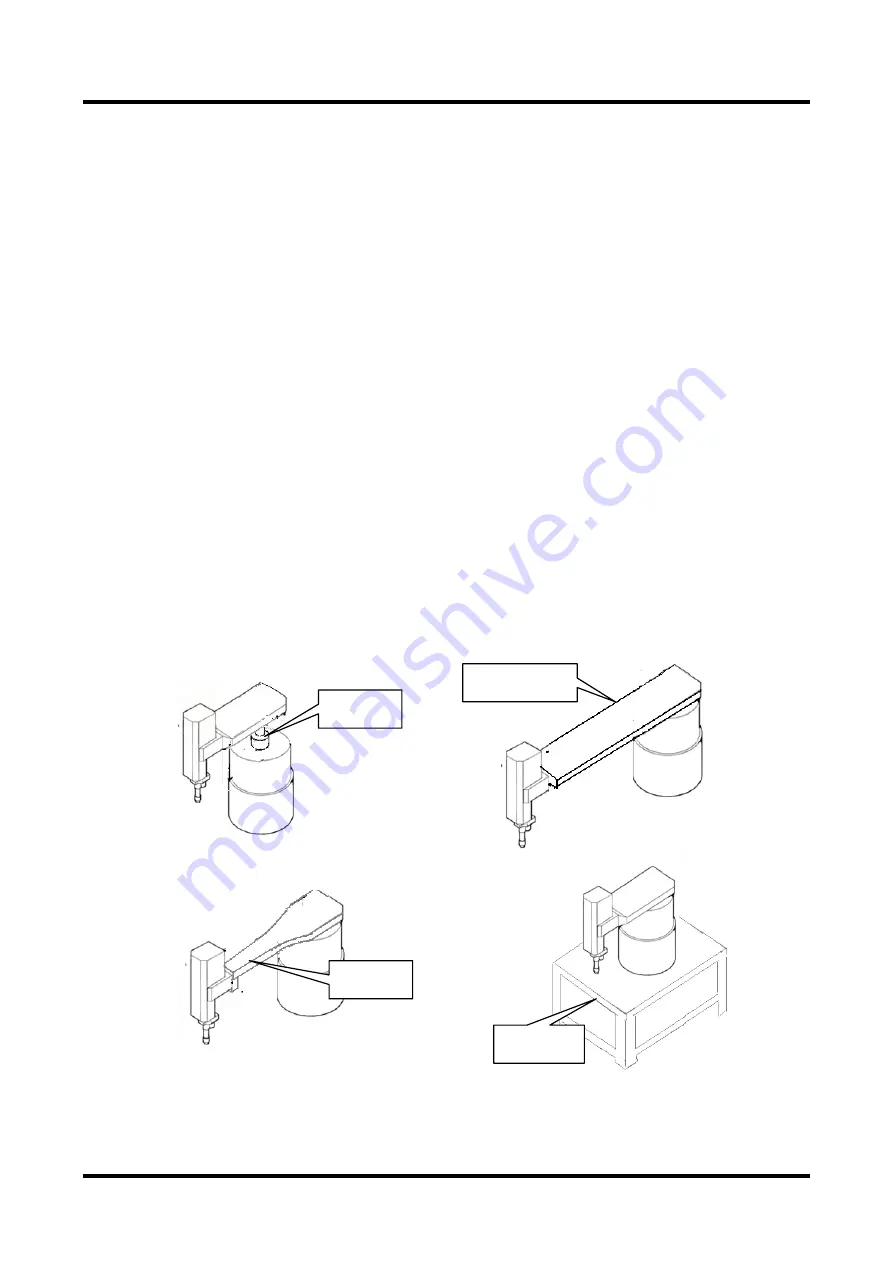
7-3
TI71M01D06-01EN 3rd Edition: 2012.12.01
7.2 Resonance
Prevention
7.2.1 Prevention of Mechanical Resonance
The DYNASERV drives the load directly without using reduction gears. Mechanical
resonance characteristics of the load and the mounting surface may cause disturbances to
the velocity control loop, causing the velocity control system to resonate.
In general, resonance phenomena can be prevented by the following three countermeasures.
(1)
Increase the rigidity of the mechanical system and the resonance frequency and
decrease the peak gain value at the resonance points.
(2)
Lower the servo rigidity (position control bandwidth and velocity control bandwidth).
(3)
Insert a filter (first-order lag compensator, notch filter, velocity feedback filter) and
lower the peak gain value of the resonance.
Each countermeasure has the following effects.
(1)
If the rigidity of the mechanical system is increased, the servo rigidity becomes higher
and the control system stabilizes.
(2)
If the servo rigidity is lowered, the resonance is improved, but the response becomes
slower. Settling takes longer in the case of the position control mode.
(3)
If a filter is inserted, the servo rigidity can be set high with countermeasure (2) and the
response is likely to be improved. However, the usage of the filter causes an extra
phase shift, and the control system may become unstable. Use this countermeasure
with care.
Increase the mechanical rigidity as much as possible first, and then perform the
countermeasures involving the servo rigidity and filter.
Example of structure with low mechanical rigidity
Slim/long
shaft
Long arm
Slim/thin arm
Low stiffness
motor fixture