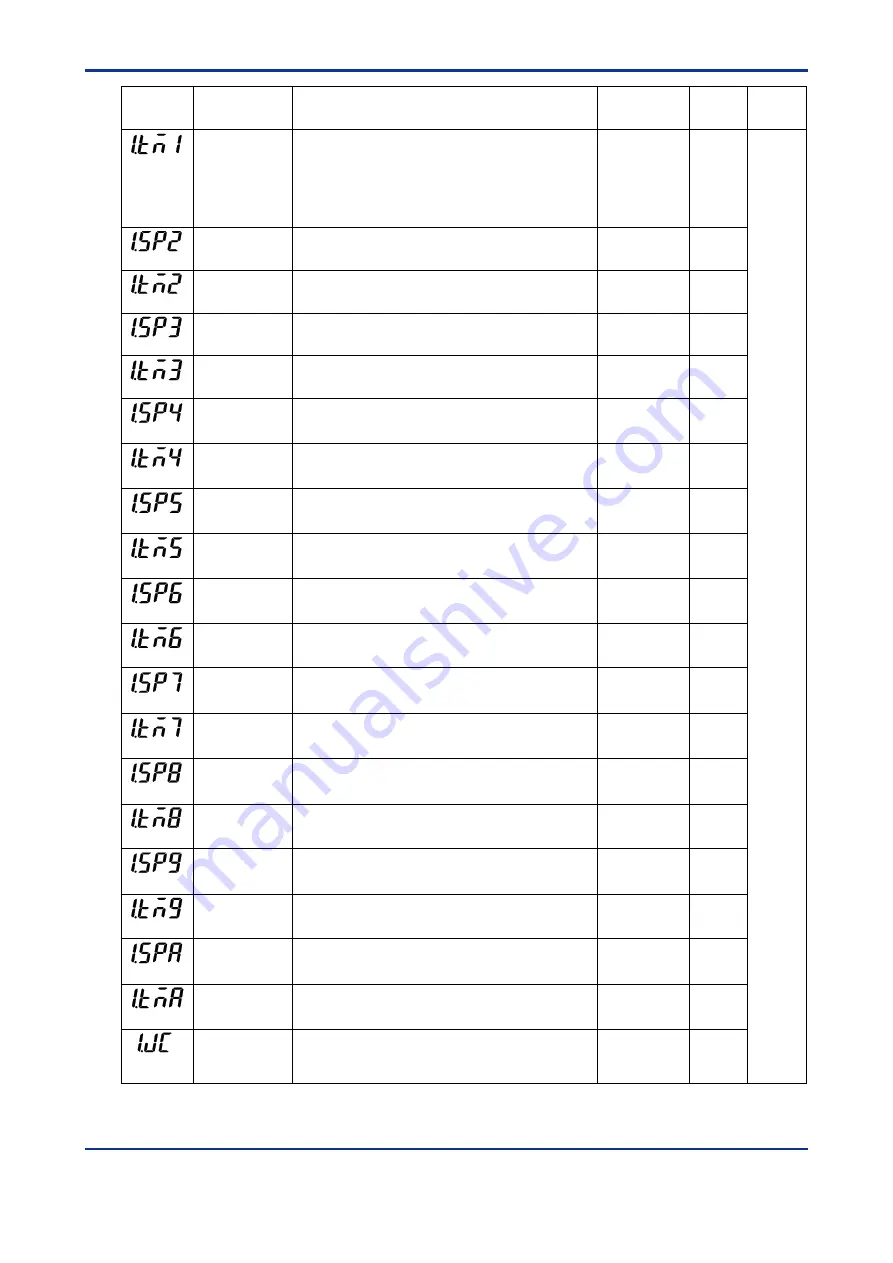
3-12
<Toc>
<3. Programming>
IM 05E01D02-41E
1st Edition : May 31,2000-00
0.0% of PV
input range
0.0% of PV
input range
0.0% of PV
input range
0.0% of PV
input range
0.0% of PV
input range
0.0% of PV
input range
0.0% of PV
input range
0.0% of PV
input range
0.0% of PV
input range
Segment-1
segment time
OFF, 0.00 to 99.59 (hour and minute or minute and second)
Ramp setting: OFF, 0.0 to 100.0% of PV input range span
(1 hr or 1 min.)
Use the TMU setup parameter to set the time unit.
The “hour and minute” option in ramp setting means “per hour”
and the “minute and second” option means “per minute.”
OFF
Segment-2
target setpoint
0.0 to 100.0% of PV input range
0.0 to 100.0% of PV input range
Segment-2
segment time
Segment-3
segment time
Segment-4
segment time
Segment-5
segment time
Segment-6
segment time
Segment-7
segment time
Segment-8
segment time
Segment-9
segment time
Segment-10
segment time
OFF, 0.00 to 99.59 (hour and minute or minute and second)
Ramp setting: OFF, 0.0 to 100.0% of PV input range span
(1 hr or 1 min.)
0.0 to 100.0% of PV input range
0.0 to 100.0% of PV input range
0.0 to 100.0% of PV input range
0.0 to 100.0% of PV input range
0.0 to 100.0% of PV input range
0.0 to 100.0% of PV input range
0.0 to 100.0% of PV input range
OFF, 0.00 to 99.59 (hour and minute or minute and second)
Ramp setting: OFF, 0.0 to 100.0% of PV input range span
(1 hr or 1 min.)
OFF, 0.00 to 99.59 (hour and minute or minute and second)
Ramp setting: OFF, 0.0 to 100.0% of PV input range span
(1 hr or 1 min.)
OFF, 0.00 to 99.59 (hour and minute or minute and second)
Ramp setting: OFF, 0.0 to 100.0% of PV input range span
(1 hr or 1 min.)
OFF, 0.00 to 99.59 (hour and minute or minute and second)
Ramp setting: OFF, 0.0 to 100.0% of PV input range span
(1 hr or 1 min.)
OFF, 0.00 to 99.59 (hour and minute or minute and second)
Ramp setting: OFF, 0.0 to 100.0% of PV input range span
(1 hr or 1 min.)
OFF, 0.00 to 99.59 (hour and minute or minute and second)
Ramp setting: OFF, 0.0 to 100.0% of PV input range span
(1 hr or 1 min.)
OFF, 0.00 to 99.59 (hour and minute or minute and second)
Ramp setting: OFF, 0.0 to 100.0% of PV input range span
(1 hr or 1 min.)
OFF, 0.00 to 99.59 (hour and minute or minute and second)
Ramp setting: OFF, 0.0 to 100.0% of PV input range span
(1 hr or 1 min.)
OFF
Segment-3
target setpoint
OFF
Segment-4
target setpoint
OFF
Segment-5
target setpoint
OFF
Ref.5.1(1)
Segment-6
target setpoint
OFF
Segment-7
target setpoint
OFF
Segment-8
target setpoint
OFF
Segment-9
target setpoint
OFF
Segment-10
target setpoint
OFF
Junction code
0: End of resetting
1: End of hold
2: Pattern 1 startup
3: Pattern 2 startup
0
Parameter
Symbol
Name of
Parameter
Setting Range and Description
Initial Value
Target Item
in CD-ROM
User
Setting
(1.TM1)
(1.SP2)
(1.TM2)
(1.TM3)
(1.TM4)
(1.TM5)
(1.TM6)
(1.TM7)
(1.TM8)
(1.TM9)
(1.SPA)
(1.TMA)
(1.JC)
(1.SP3)
(1.SP4)
(1.SP5)
(1.SP6)
(1.SP7)
(1.SP8)
(1.SP9)
Summary of Contents for UP350
Page 2: ...Blank Page ...
Page 52: ...Blank Page ...
Page 62: ...Blank Page ...
Page 72: ...Blank Page ...
Page 94: ...Blank Page ...
Page 96: ...Blank Page ...