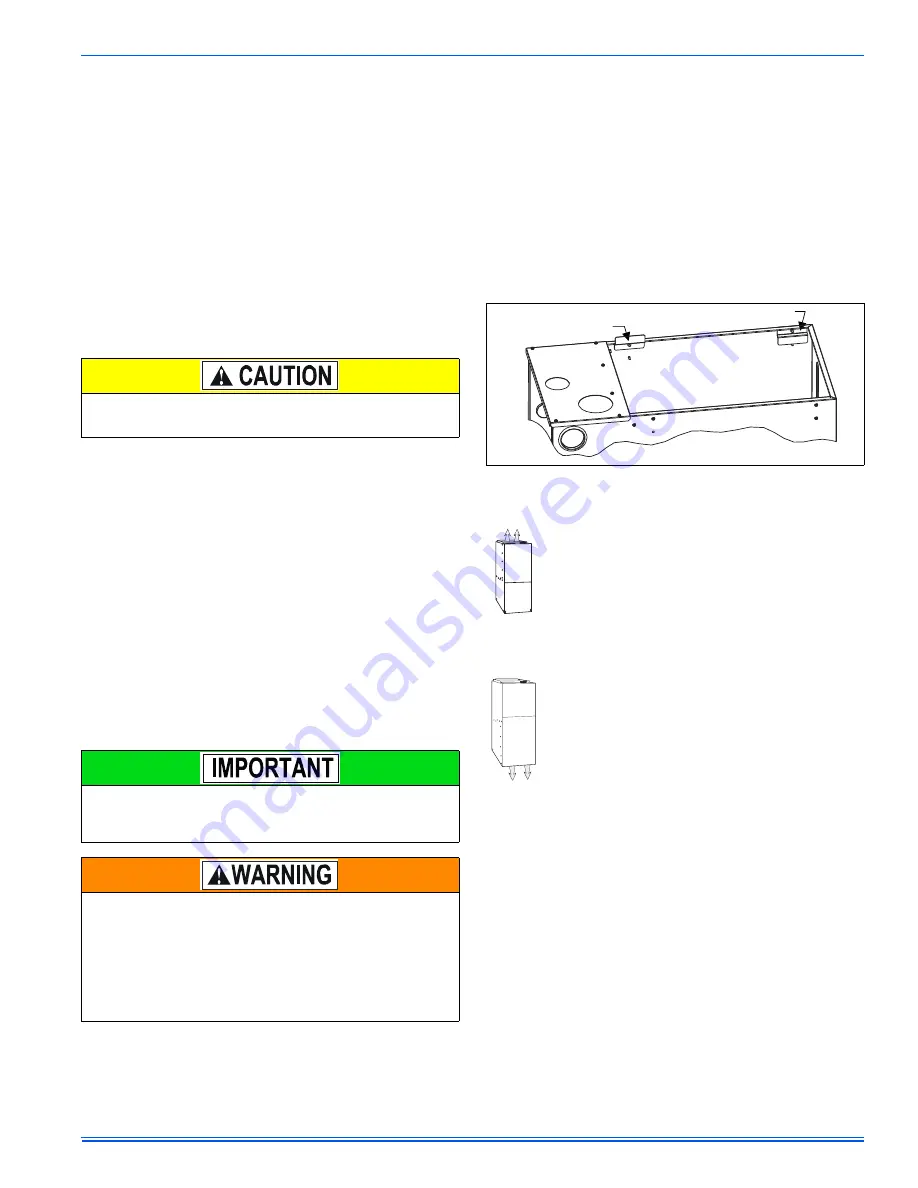
1083292-UIM-A-0114
Johnson Controls Unitary Products
5
SECTION II: DUCTWORK
DUCTWORK GENERAL INFORMATION
The duct system’s design and installation must:
1.
Handle an air volume appropriate for the served space and within
the operating parameters of the furnace specifications.
2.
Be installed in accordance of National Fire Protection Association
as outlined in NFPA standard 90B (latest editions) or applicable
national, provincial, state, and local fire and safety codes.
3.
Create a closed duct system. For residential and non-HUD Modu-
lar Home installations, when a furnace is installed so that the sup-
ply ducts carry air circulated by the furnace to areas outside the
space containing the furnace, the return air shall also be handled
by a duct(s) sealed to the furnace casing and terminating outside
the space containing the furnace.
4.
Complete a path for heated or cooled air to circulate through the
air conditioning and heating equipment and to and from the condi-
tioned space.
When the furnace is used with an indoor coil, the coil must be installed
parallel with, or in the supply air side of the furnace to avoid condensa-
tion in the primary heat exchanger. When a parallel flow arrangement is
used, dampers or other means used to control airflow must be ade-
quate to prevent chilled air from entering the furnace. If manually oper-
ated, the damper must be equipped with means to prevent the furnace
or the air conditioner from operating unless the damper is in full heat or
cool position.
When replacing an existing furnace, if the existing plenum is not the
same size as the new furnace then the existing plenum must be
removed and a new plenum installed that is the proper size for the new
furnace. If the plenum is shorter than 12” (30.5 cm) the turbulent air flow
may cause the limit controls not to operate as designed, or the limit con-
trols may not operate at all.
The duct system is a very important part of the installation.
If the duct
system is improperly sized the furnace will not operate properly.
The ducts attached to the furnace plenum, should be of sufficient size
so that the furnace operates at the specified external static pressure
and within the air temperature rise specified on the nameplate.
If a matching indoor coil is used, it may be placed directly on the fur-
nace outlet and sealed to prevent leakage. If an uncased indoor coil
with a thermoplastic drain pan is to be installed in the upflow/horizontal
configuration, then extra 2” (5.1 cm) minimum spacing may be needed
to ensure against drain pan distortion.
On all installations without a coil, a removable access panel is recom-
mended in the outlet duct such that smoke or reflected light would be
observable inside the casing to indicate the presence of leaks in the
heat exchanger. This access cover shall be attached in such a manner
as to prevent leaks.
DUCT FLANGES
Four flanges are provided to attach ductwork to the furnace. These
flanges are rotated down for shipment. In order to use the flanges,
remove the screw holding an individual flange, rotate the flange so it is
in the upward position and reinstall the screw then repeat this for all 4
flanges.
If the flanges are not used, they must remain in the rotated down posi-
tion as shipped.
DUCTWORK INSTALLATION AND SUPPLY PLENUM
CONNECTION - UPFLOW/HORIZONTAL
Attach the supply plenum to the furnace outlet. The use of
an approved flexible duct connector is recommended on all
installations. This connection should be sealed to prevent
air leakage. The sheet metal should be crosshatched to
eliminate any popping of the sheet metal when the indoor
fan is energized.
FLOOR BASE AND DUCTWORK INSTALLATION -
DOWNFLOW
Installations on combustible material or directly on any
floors must use a combustible floor base shown in Figure 2.
Follow the instructions supplied with the combustible floor
base accessory. This combustible floor base can be
replaced with a matching indoor coil, properly sealed to pre-
vent leaks. Follow the instructions supplied with the indoor
coil cabinet for installing the cabinet to the duct connector.
Plug intake and vent pipe holes in bottom panel and move
grommet to desired vent side exit.
Downflow Air - Indoor Coil Cabinet
The furnace should be installed with coil cabinet part number specifi-
cally intended for downflow application. If a matching indoor coil is
used, it may be placed directly on the furnace outlet and sealed to pre-
vent leakage. For details of the coil cabinet dimensions and installation
requirements, refer to the installation instructions supplied with the coil
cabinet.
Attach the indoor coil cabinet to the duct connector, and then position
the furnace on top of the coil cabinet. The connection to the furnace, air
conditioning coil cabinet, duct connector, and supply air duct must be
sealed to prevent air leakage.
DOWNFLOW DUCT CONNECTORS
All downflow installations must use a suitable duct connector approved
by the furnace manufacturer for use with this furnace. The duct connec-
tors are designed to be connected to the rectangular duct under the
floor and sealed. Refer to the instructions supplied with the duct con-
nector for proper installation.
The indoor coil must be installed in the supply air duct, downstream
of the furnace. Cooled air may not be passed over the heat
exchanger.
The minimum plenum height is 12” (30.5 cm). The furnace will not
operate properly on a shorter plenum height. The minimum recom-
mended rectangular duct height is 4” (10.2 cm) attached to the ple-
num.
The duct system must be properly sized to obtain the correct airflow
for the furnace size that is being installed.
Refer to the furnace rating plate for the correct rise range and static
pressures or to Table 6 for the correct rise range.
If the ducts are undersized, the result will be high duct static pres-
sures and/or high temperature rises which can result in a heat
exchanger OVERHEATING CONDITION. This condition can result
in premature heat exchanger failure, which can result in personal
injury, property damage, or death.
FIGURE 1:
Duct Attachment
Factory Installed
For duct attachment,
if needed