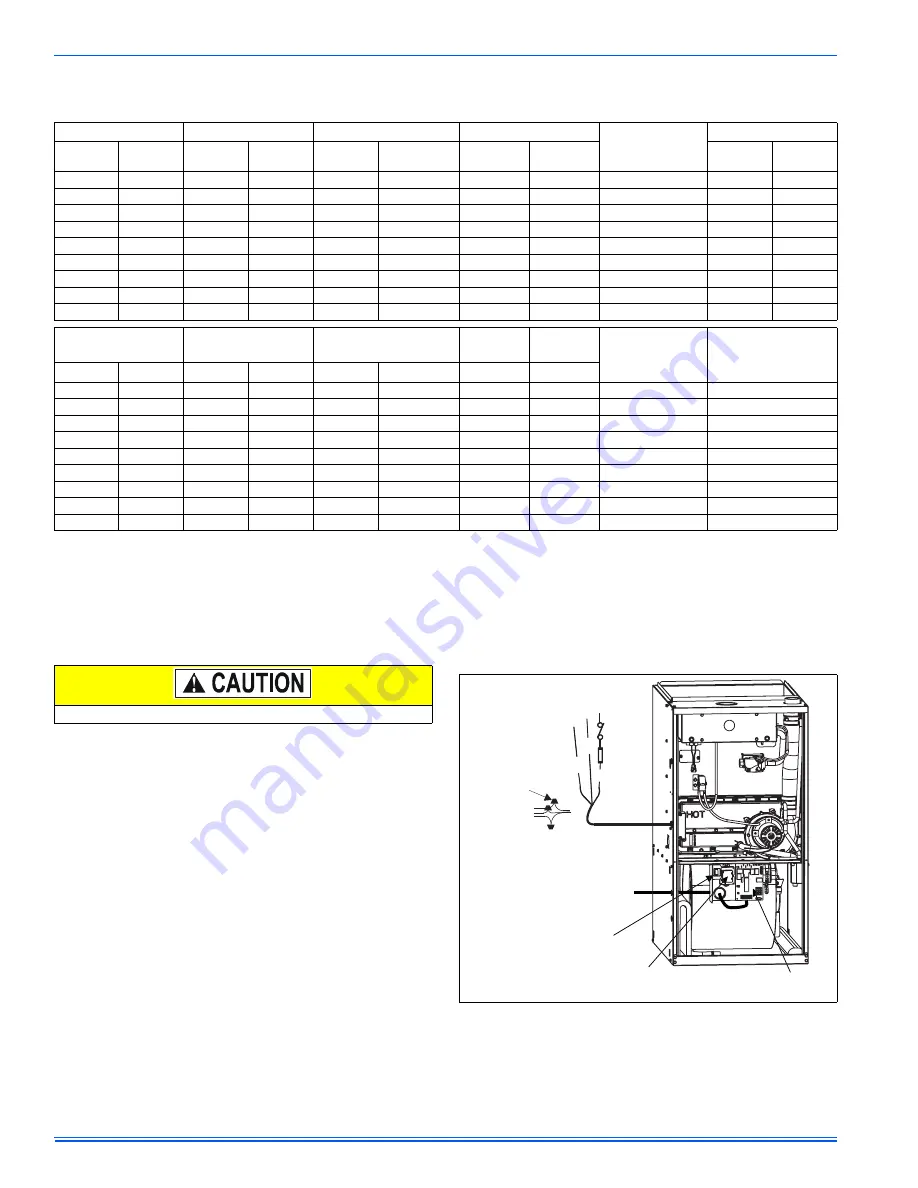
105561-UIM-B-0605
8
Unitary Products Group
SECTION V: ELECTRICAL POWER
Annual Fuel Utilization Efficiency (AFUE) numbers are determined in accordance with DOE Test procedures.
Wire size and over current protection must comply with the National Electrical Code (NFPA-70-latest edition) and all local codes.
The furnace shall be installed so that the electrical components are protected from water.
ELECTRICAL POWER CONNECTIONS
Field wiring to the unit must be grounded. Electric wires that are field
installed shall conform to the temperature limitation for 63°F (35°C) rise
wire when installed in accordance with instructions. Refer to Table 7 in
these instructions for specific furnace electrical data.
SUPPLY VOLTAGE CONNECTIONS
IMPORTANT: The power connection leads and wiring box may be relo-
cated to the left side of the furnace. Remove the screws and cut wire tie
holding excess wiring. Reposition on the left side of the furnace and fas-
ten using holes provided.
1.
Provide a power supply separate from all other circuits. Install
overcurrent protection and disconnect switch per local/national
electrical codes. The switch should be close to the unit for conve-
nience in servicing. With the disconnect or fused switch in the OFF
position, check all wiring against the unit wiring label. Refer to the
wiring diagram shown in Figure 27.
2.
Remove the screws retaining the junction box cover. Route the
power wiring through the opening in the unit into the junction box
with a conduit connector or other proper connection. In the junc-
tion box there will be three wires, a Black Wire, a White Wire and a
Green Wire. Connect the power supply as shown on the unit-wir-
ing label on the inside of the blower compartment door or Figure 6.
The black furnace lead must be connected to the L1 (hot) wire
from the power supply. The white furnace lead must be connected
to neutral. Connect the green furnace lead (equipment ground) to
the power supply ground. An alternate wiring method is to use a
field provided 2” (5.08 cm) x 4” (10.2 cm) box and cover on the
outside of the furnace. Route the furnace leads into the box using
a protective bushing where the wires pass through the furnace
panel. After making the wiring connections replace the wiring box
cover and screws.
3.
The furnace's control system requires correct polarity of the power
supply and a proper ground connection. If the power supply polar-
ity is reversed, the control board will flash 9 times. The furnace will
not operate until the polarity is corrected. Refer to “Furnace Diag-
nostics” section of the “User’s Information, Maintenance, & Ser-
vice Manual provided with this furnace.
TABLE 7: Electrical and Performance Data
Input/Cabinet
Output
Blower Size
Blower
Max.
Over-current
Protect
Air Temp. Rise
MBH
kW
MBH
kW
In.
cm
HP
Amps
°F
°C
40/A
11.7
38
11.1
11 x 8
27.9 x 20.3
1/2
7.0
20
35 - 65
19 - 36
60/B
17.6
56
16.1
11 x 8
27.9 x 20.3
1/2
7.0
20
40 - 70
22 - 39
80/B
23.4
74
21.9
11 x 8
27.9 x 20.3
1/2
7.0
20
45 - 75
25 - 42
80/C
23.4
75
22.0
11 x 10
27.9 x 25.4
3/4
10.2
20
45 - 75
25 - 42
80/C
23.4
75
22.0
11 x 11
27.9 x 27.9
1
12.7
20
40 - 70
22 - 39
100/C
29.3
93
27.8
11 x 10
25.4 x 25.4
3/4
10.2
20
45 - 75
25 - 42
100/C
29.3
93
27.8
11 x 11
27.9 x 27.9
1
12.7
20
40 - 70
22 - 39
120/D
35.2
112
32.8
11 x 11
27.9 x 27.9
1
12.7
20
40 - 70
22 - 39
135/D
39.6
127
36.9
11 x 11
27.9 x 27.9
1
12.7
20
45 - 75
23 - 42
Max. Outlet
Air Temp.
Nominal Airflow
Cabinet Width
Total Unit
AFUE
Min. Wire Size
(awg) @ 75 ft.
One Way
Approximate
Operating Weight
°F
°C
CFM
m
3
/min
In.
cm
Amps
%
165
73.9
1200
34.0
14-1/2
36.8
9
94.0
14
119
170
76.7
1200
34.0
17-1/2
44.4
9
92.0
14
133
175
79.4
1200
34.0
17-1/2
44.4
9
92.0
14
140
175
79.4
1600
45.3
21
53.3
12
92.0
14
155
170
7607
2000
56.6
21
53.3
14
92.0
12
157
175
79.4
1600
45.3
21
53.3
12
92.0
14
160
170
76.7
2000
56.6
21
53.3
14
92.0
12
162
170
76.7
2000
56.6
24-1/2
62.2
14
92.0
12
178
175
79.4
2000
56.6
24-1/2
62.2
14
92.0
12
178
Use copper conductors only.
FIGURE 5: Electrical Wiring
N
GND
L1
HOT
WHT
GRN
BLK
BLK/BLK
WHT/WHT
GRN/GRN
CLASS 2 SYSTEM
CONTROL WIRING
TO THERMOSTAT
BLOWER
COMPARTMENT
DOOR SWITCH
TRANSFORMER
IGNITION
MODULE