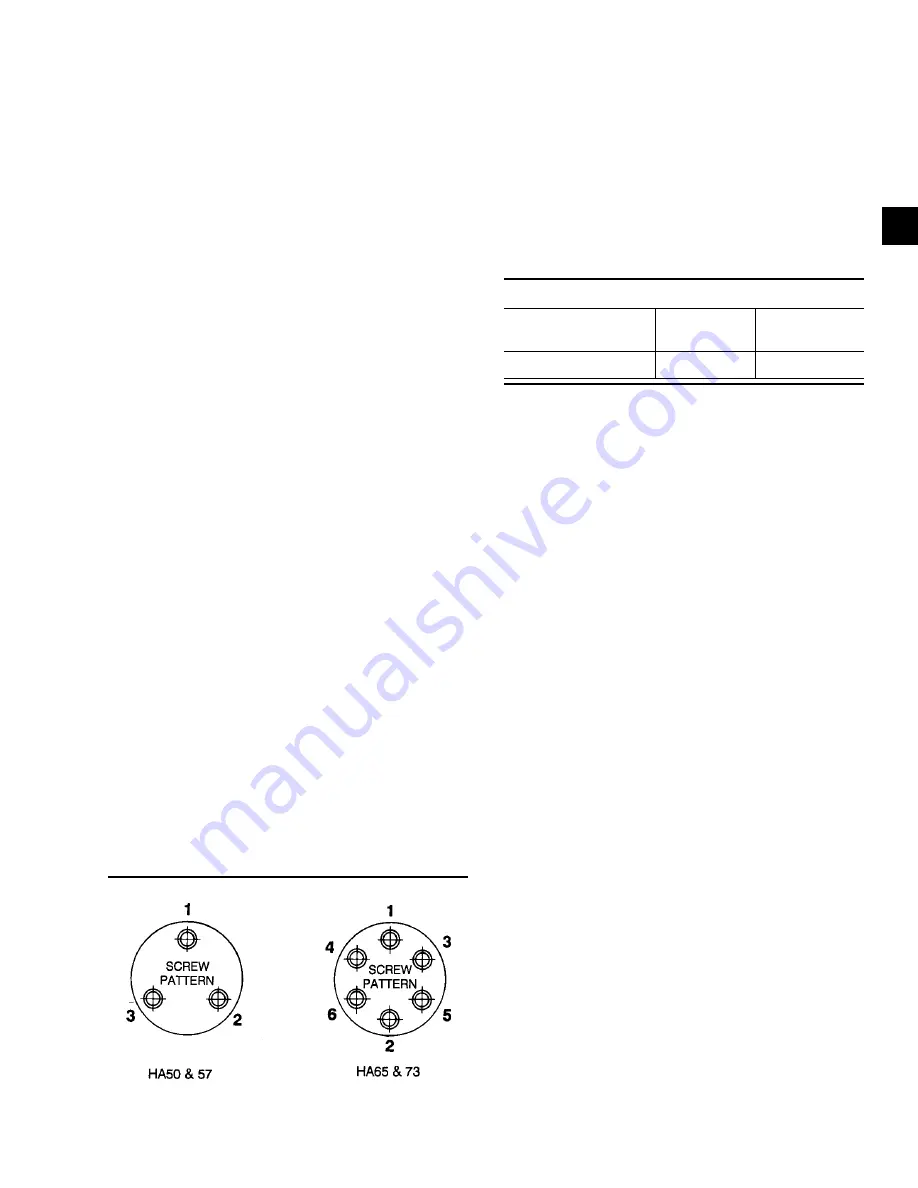
FORM 160.49-M1
31
YORK INTERNATIONAL
INSTALLING BALANCE PISTON AND
DIFFUSER PLATE
1. Install a new O-ring on the diffuser plate.
2. Insert (2) ¼" diameter guide pins into the rotor sup-
port.
3. Using proper rigging methods, slide the diffuser plate
over the guide pins and into position against the ro-
tor support. (See Fig. 34)
4. Insert (4) of the bolts before removing rigging and
guide pins; then insert remaining bolts and tighten.
5. On the HF style compressor, install that flat spring
onto the balance piston seal. On all other style com-
pressors, install the (8) or (16) helical springs, large
end first, into the balance piston seal. Rotate each
spring to lock it into place. (See Fig. 33)
6. Apply Loctite and insert the (3) cap screws and
fasten the balance piston seal and balance piston
retainer to the diffuser plate.
7. After tightening the (3) cap screw, check that the
balance piston seal is free to “float”.
INSTALLING THE IMPELLER
Impeller Sizes 46 and Larger
1. Re-install the shaft locking tool.
2. Apply a light coating of oil and Molykote to the in-
side diameter of the balance piston seal.
3. Slide impeller into position on the high-speed shaft
using care not to damage the balance piston seal.
4. Install the impeller clamping collar and the (3) or
(6) cap screws onto the high speed shaft.
5. Torque cap screws to 120 ft. lbs. in (2) equal steps.
Refer to Fig. 62 for sequence of tightening screws.
6. Remove the shaft locking tool and check rim and
eye radial runout using a dial indicator. (See Fig.
27). Maximum runout on rim is .003" and runout on
eye is .002". If T.I.R. deviates from specification,
increase torque to 150 ft. lbs. Maximum to the bolts
opposite to the high side. Repeat as necessary until
allowable T.I.R. is achieved.
7. Check high-speed thrust clearance. Acceptable
thrust tolerance is between .008" to .021".
8. Check low-speed thrust clearance. Acceptable
thrust tolerance is between .011" to .019" Note that
this measurement must be taken with the shaft seal
installed.
Impeller for HA36 and HA41
1. Re-install the shaft locking tool.
2. Apply a light coating of oil and Molykote to the in-
side diameter of the balance piston seal.
3. Install O-ring in impeller and install on the high-speed
shaft using care not to damage the balance piston
seal.
4. Install O-ring on impeller clamping collar and install
in impeller bore over high-speed shaft.
MAKE
ABSOLUTELY CERTAIN THAT O-RINGS
ARE IN PLACE PRIOR TO INSTALLING
AND TORQUING CAP SCREW
.
5. Torque cap screw to 120 ft. lbs.
6. Remove the shaft locking tool and check rim and
eye radial runout using a dial indicator. (See Fig.
27). Maximum runout on rim is .003" and runout on
eye is .002".
7. Check high-speed thrust clearance. Acceptable
thrust tolerance is between .008" to .021".
8. Check low-speed thrust clearance. Acceptable
thrust tolerance is between .011" to .019". Note that
this measurement must be taken with the shaft seal
installed.
Impeller for HF Compressors
1. Re-install the shaft locking tool.
2. Apply a light coating of oil and Molykote to the in-
side diameter of the balance piston seal.
3. Install impeller and clamping collar on high-speed
shaft.
4. Torque cap screw to 90 ft. lbs.
FIG. 62 –
IMPELLER MOUNTING SCREWS
TIGHTENING SEQUENCE
LD05188
PERMISSIBLE RUNOUT OF IMPELLER
IMPELLER DIA.
RIM
EYE
(INCHES)
RADIAL
RADIAL
11.30, 10.00
.003
.002
2