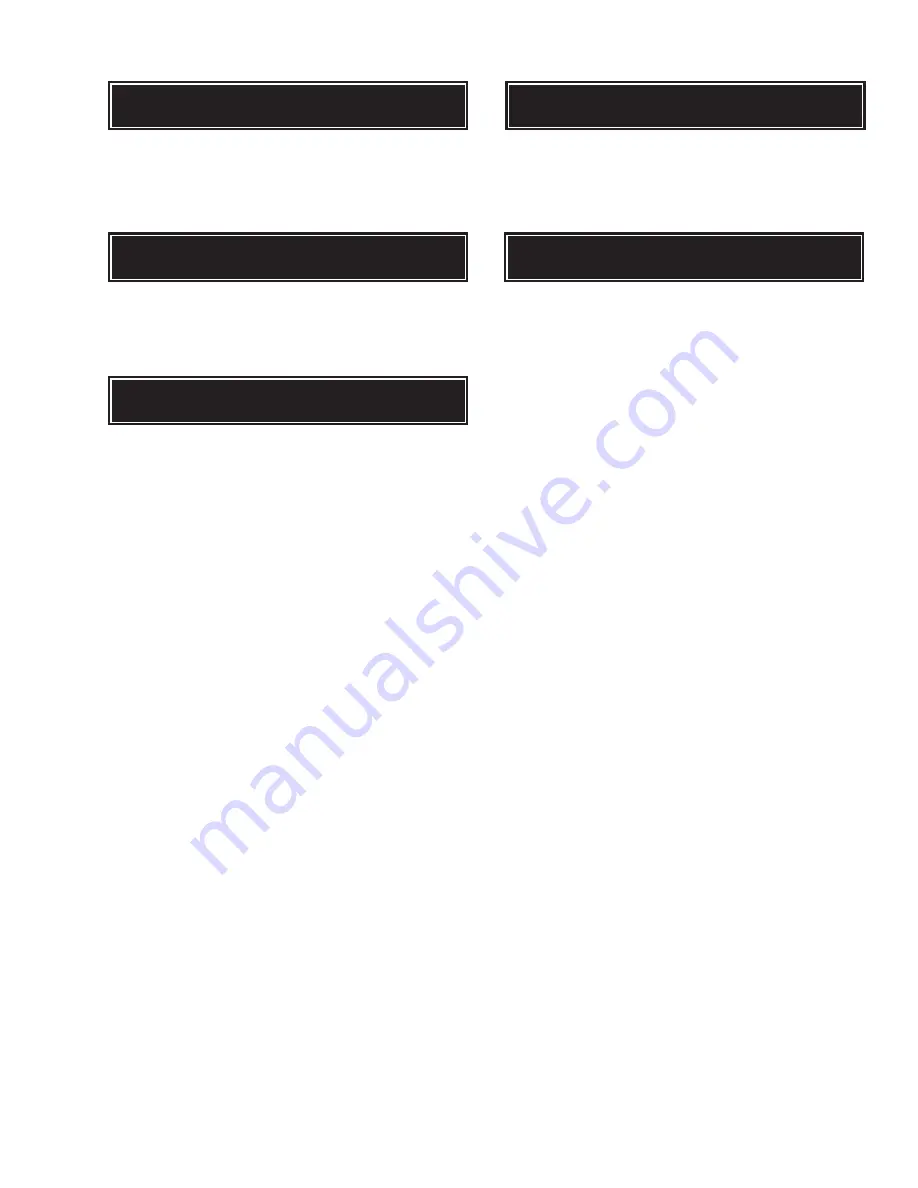
FORM 201.10-NM1
121
YORK INTERNATIONAL
This message indicates that the Liquid Injection Sole-
noid Valve of SYS 2 was either energized (ON) or de-
energized (OFF) at the time of the fault.
This display indicates the number of pairs of fans on
SYS 2 which were running in the forward direction at the
time of the fault.
This message indicates whether a pair of fans on SYS 2
were running in the reverse direction at the time of the
fault.
S Y S
2
L I Q U I D
I N J E C T I O N
V A L V E
O F F
S Y S
2
F O R W A R D
F A N S
O N
S Y S
2
R E V E R S E
F A N S
O F F
This display informs the operator whether SYS 2 liquid
line solenoid valve was energized (ON) or de-energized
(OFF) at the time of the fault.
This message informs the operator if SYS 1 Run Per-
missive (flow switch, remote START/STOP) was in the
“RUN” mode (ON/closed) or “STOP” mode (OFF/open).
S Y S
2
L I Q
L I N E
O N
S Y S
2
R U N
P E R M I S S I V E
O N
Summary of Contents for Millennium YCAS 216X
Page 11: ...FORM 201 10 NM1 11 YORK INTERNATIONAL YCAS 140 246 DIMENSIONS English LD01444 LD01446...
Page 13: ...FORM 201 10 NM1 13 YORK INTERNATIONAL YCAS 140 246 DIMENSIONS SI LD01440 LD01442...
Page 15: ...FORM 201 10 NM1 15 YORK INTERNATIONAL YCAS 216X 266X DIMENSIONS English LD01454 LD01454...
Page 17: ...FORM 201 10 NM1 17 YORK INTERNATIONAL YCAS 216X 266X DIMENSIONS SI LD01450 LD01448...
Page 33: ...FORM 201 10 NM1 33 YORK INTERNATIONAL 28514A FILTER DRYER LIQUID STOP VALVE...
Page 37: ...FORM 201 10 NM1 37 YORK INTERNATIONAL LD01285 FIG 3 SCREW CHILLER REFIGERANT FLOW DIAGRAM...
Page 59: ...FORM 201 10 NM1 59 YORK INTERNATIONAL FIG 11 CONTINUED LD01465 D...
Page 61: ...FORM 201 10 NM1 61 YORK INTERNATIONAL FIG 12 CONTINUED LD01458 D...
Page 69: ...FORM 201 10 NM1 69 YORK INTERNATIONAL FIG 16 CONTINUED LD01206 D...
Page 71: ...FORM 201 10 NM1 71 YORK INTERNATIONAL FIG 17 CONTINUED LD01202 D...