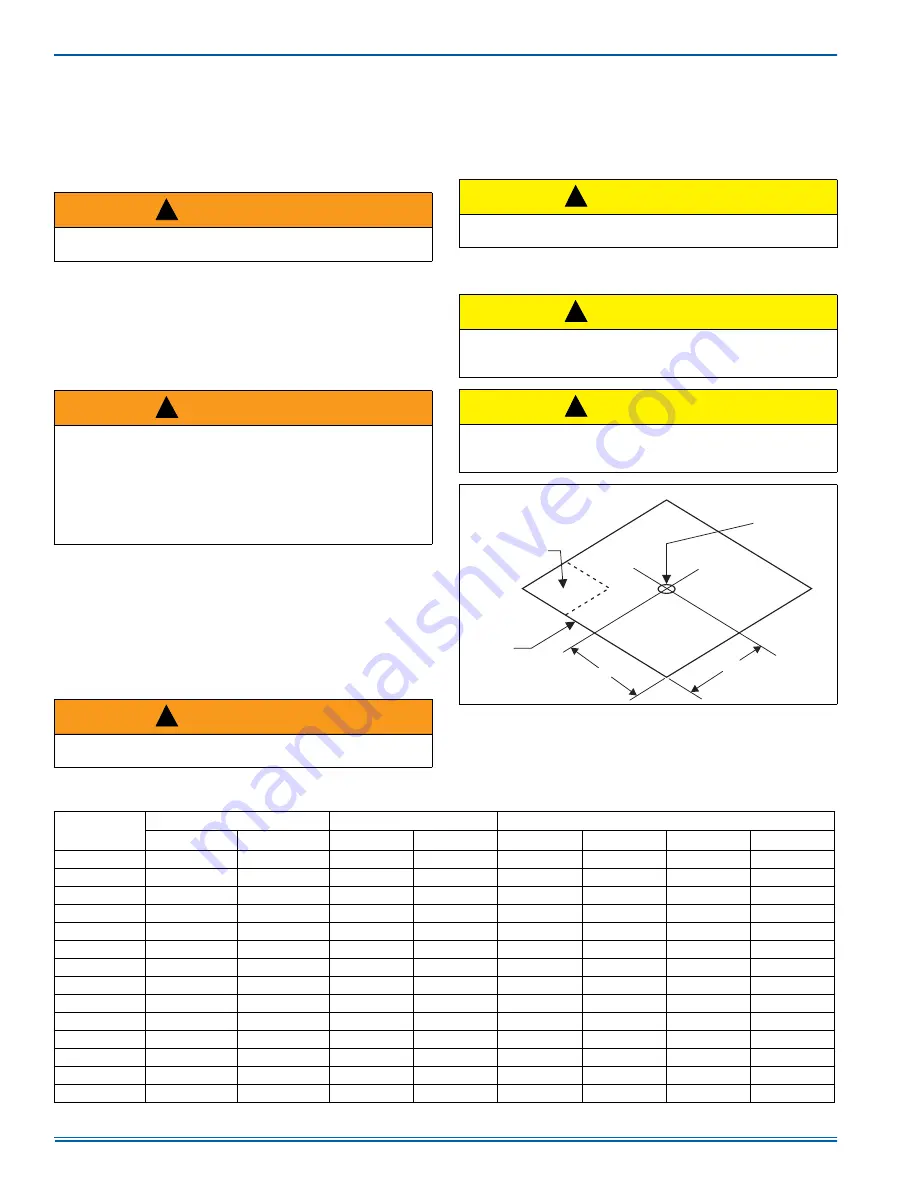
5132210-UIM-H-0916
4
Johnson Controls Unitary Products
LOCATION
Use the following guidelines to select a suitable location for these units:
1.
Unit is designed for
outdoor installation
only.
2.
Condenser coils must have an unlimited supply of air. Where a
choice of location is possible, position the unit on either north or
east side of building.
3.
Suitable for mounting on roof curb.
4.
For ground level installation, a level pad or slab should be used.
The thickness and size of the pad or slab used should meet local
codes and unit weight. Do not tie the slab to the building foundation.
5.
Roof structures must be able to support the weight of the unit and
its options/accessories. Unit must be installed on a solid, level roof
curb or appropriate angle iron frame.
6.
Maintain level tolerance to 1/8” across the entire width and length of
unit.
CLEARANCES
All units require particular clearances for proper operation and service.
Installer must make provisions for adequate combustion and ventilation
air in accordance with section 5.3 of Air for Combustion and Ventilation
of the National Fuel Gas Code, ANSI Z223.1 – Latest Edition (in
U.S.A.), or Sections 7.2, 7.3, or 7.4 of Gas Installation Codes, CSA-
B149.1 (in Canada) - Latest Edition, and/or applicable provisions of the
local building codes. Refer to Table 4 for clearances required for com-
bustible construction, servicing, and proper unit operation.
RIGGING AND HANDLING
Exercise care when moving the unit. Do not remove any packaging until
the unit is near the place of installation. Rig the unit by attaching chain
or cable slings to the lifting holes provided in the base rails. Spreader
bars, whose length exceeds the largest dimension across the unit,
MUST
be used across the top of the unit.
Units may be moved or lifted with a forklift. Slotted openings in the base
rails are provided for this purpose.
WARNING
Do not attach supply and return duct work to the bottom of the unit
base pan as the drain pan could be compromised.
WARNING
Excessive exposure of this furnace to contaminated combustion air
may result in equipment damage or personal injury. Typical contami-
nates include: permanent wave solution, chlorinated waxes and
cleaners, chlorine based swimming pool chemicals, water softening
chemicals, carbon tetrachloride, Halogen type refrigerants, cleaning
solvents (e.g. perchloroethylene), printing inks, paint removers, var-
nishes, hydrochloric acid, cements and glues, antistatic fabric soften-
ers for clothes dryers, masonry acid washing materials.
WARNING
Do not permit overhanging structures or shrubs to obstruct con-
denser air discharge outlet, combustion air inlet or vent outlets.
!
!
!
CAUTION
Before lifting, make sure the unit weight is distributed equally on the
rigging cables so it will lift evenly.
CAUTION
If a unit is to be installed on a roof curb other than a Unitary Products
roof curb, gasket or sealant must be applied to all surfaces that come
in contact with the unit underside.
CAUTION
All panels must be secured in place when the unit is lifted.
The condenser coils should be protected from rigging cable damage
with plywood or other suitable material.
FIGURE 2:
Unit 4 Point Load Weight
!
!
!
X
CENTER OF
GRAVITY
FRONT
OF UNIT
Y
"D"
"C"
"B"
"A"
A0295-001
COMPRESSOR
Table 2:
Weights and Dimensions
Model
Weight (lbs.)
Center of Gravity
4 Point Load Location (lbs.)
Shipping
Operating
X
Y
A
B
C
D
24050
399
394
28
15
131
101
86
76
24075
409
404
28
15
135
103
86
80
30050
454
449
28
15
155
108
96
90
30075
458
453
28
15
161
102
90
100
36065
503
498
29
14
176
122
104
96
36100
510
505
29
14
178
123
109
95
42065
537
532
29
14
190
132
112
98
42100
539
534
29
14
191
133
109
101
48065
556
551
28
14
199
137
106
109
48100
564
559
28
14
194
141
117
107
48125
569
564
29
14
193
146
126
99
60065
582
577
29
14
199
151
127
100
60100
586
581
28
14
201
152
123
105
60125
593
588
27
15
202
151
125
110