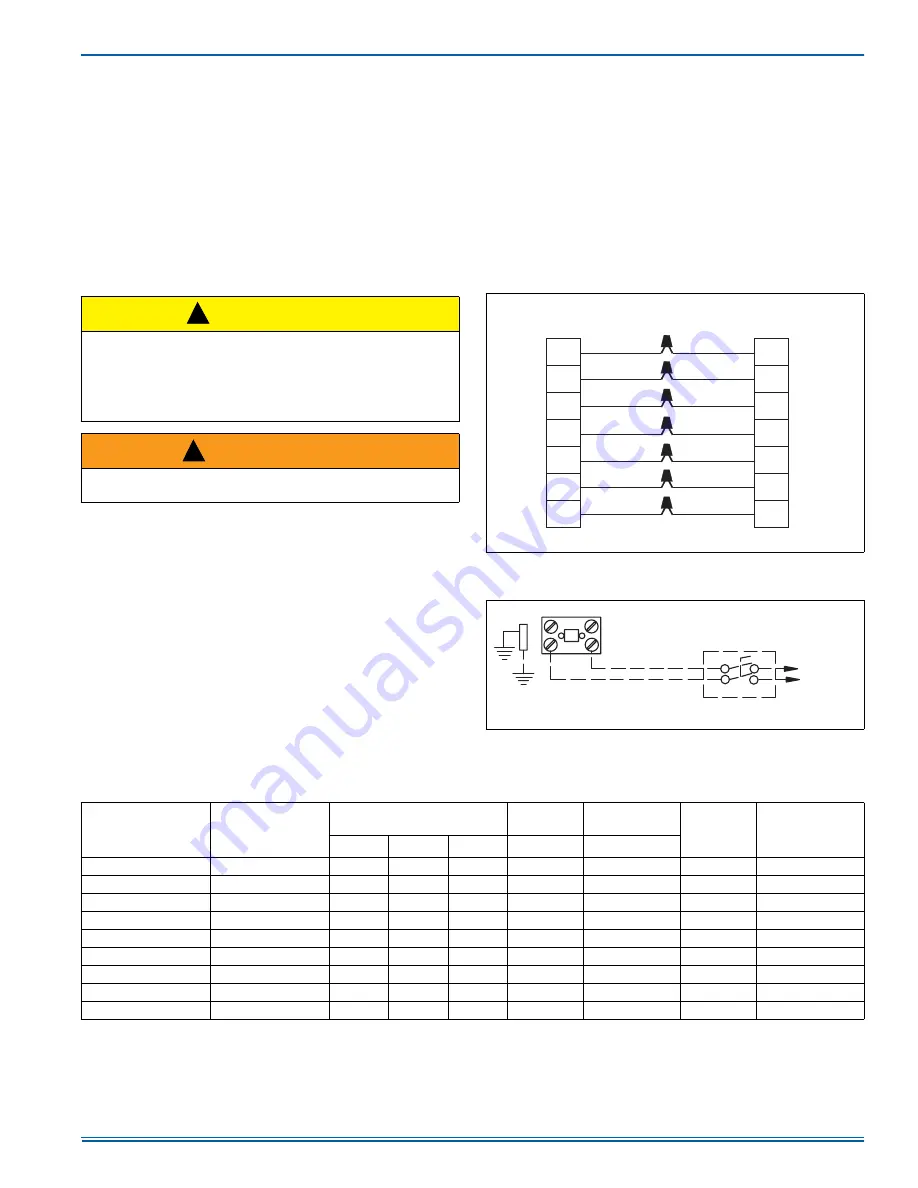
5132210-UIM-H-0916
Johnson Controls Unitary Products
7
SERVICE ACCESS
Access to all serviceable components is provided at the following loca-
tions:
• Coil guards
• Unit top panel
• Corner posts
• Blower access panel
• Control access panel
• Indoor coil access panel
• Compressor access panel
• Heat exchanger access panel
Refer to Figure 4 for location of these access locations and minimum
clearances in Table 4.
Refer to Figure 14 for the R-410A Quick Reference Guide.
THERMOSTAT
The room thermostat should be located on an inside wall approximately
60" above the floor where it will not be subject to drafts, sun exposure
or heat from electrical fixtures or appliances. Sealant should be used
behind thermostat to prevent air infiltration. Follow manufacturer's
instructions enclosed with the thermostat for general installation proce-
dure. Color coded insulated wires (minimum #18 AWG) should be used
to connect thermostat to unit. See Figure 6. Do not use power stealing
thermostats. Thermostat must be a heat pump thermostat able to con-
trol fossil fuel backup heat.
POWER AND CONTROL WIRING
Field wiring to the unit must conform to provisions of the current N.E.C.
ANSI/NFPA No. 70 or C.E.C. and/or local ordinances. The unit must be
electrically grounded in accordance with local codes or, in their
absence, with the N.E.C./C.E.C. Voltage tolerances which must be
maintained at the compressor terminals during starting and running
conditions are indicated on the unit Rating Plate and Table 1.
The wiring entering the cabinet must be provided with mechanical strain
relief.
A fused disconnect switch should be field provided for the unit. If any of
the wire supplied with the unit must be replaced, replacement wire must
be of the type shown on the wiring diagram.
Electrical service must be sized properly to carry the load. Each unit
must be wired with a separate branch circuit fed directly from the main
distribution panel and properly fused.
Refer to Figures 7 and 8 for typical field wiring and to the appropriate
unit wiring diagram for control circuit and power wiring information.
CAUTION
This system uses R-410A Refrigerant which operates at higher pres-
sures than R-22. No other refrigerant may be used in this system.
Gage sets, hoses, refrigerant containers and recovery systems must
be designed to handle R-410A. If you are unsure, consult the equip-
ment manufacturer. Failure to use R-410A compatible servicing
equipment may result in property damage or injury.
WARNING
Wear safety glasses and gloves when handling refrigerants. Failure
to follow this warning can cause serious personal injury.
!
!
FIGURE 6:
Typical Field Control Wiring Diagram For Gas Heat - AC
Models
FIGURE 7:
Typical Field Power Wiring Diagram
THERMOSTAT
NOTE:
Heat Anticipator should be set at 0.35 AMPS for all models
CONTROL HARNESS
Minimum wire size of 18 AWG wire should be used for all field
installed control wiring.
RED
ORANGE
YELLOW
BLUE
A0377-001
W
Y
O
R
C
W2
W
Y
O
R
C
W2
WHITE
BROWN
GREEN
G
G
CONTACTOR
FIELD SUPPLIED
DISCONNECT
GND
LUG
REFER TO ELECTRICAL
DATA TABLES TO SIZE
THE DISCONNECT
SINGLE
PHASE
POWER
SUPPLY
A0293-001
Table 5:
Electrical Data
Model
Voltage
Compressor
OD Fan
Motor
Supply
Blower Motor
MCA
1
(Amps)
1. Minimum Circuit Ampacity.
Max Fuse
2
/
Breaker
3
Size
(Amps)
2. Maximum Over Current Protection per standard UL 1995.
3. Fuse or HACR circuit breaker size installed at factory or field installed.
RLA
LRA
MCC
FLA
FLA
24050
208/230-1-60
10.0
62.0
16.0
0.7
2.6
15.8
25
24075
208/230-1-60
10.0
62.0
16.0
0.7
3.8
17.0
25
30050
208/230-1-60
14.0
73.0
22.0
0.6
2.6
20.7
30
30075
208/230-1-60
14.0
73.0
22.0
0.6
3.8
21.9
35
36065
208/230-1-60
17.0
79.0
26.0
1.7
3.8
26.8
40
36100
208/230-1-60
17.0
79.0
26.0
1.7
5.4
28.4
45
42065, 42100
208/230-1-60
18.0
112.0
28.0
1.7
5.4
29.6
45
48065, 48100, 48125
208/230-1-60
22.0
117.0
34.0
1.7
5.4
34.6
50
60065, 60100, 60125
208/230-1-60
24.0
144.0
38.0
1.7
7.0
38.7
60