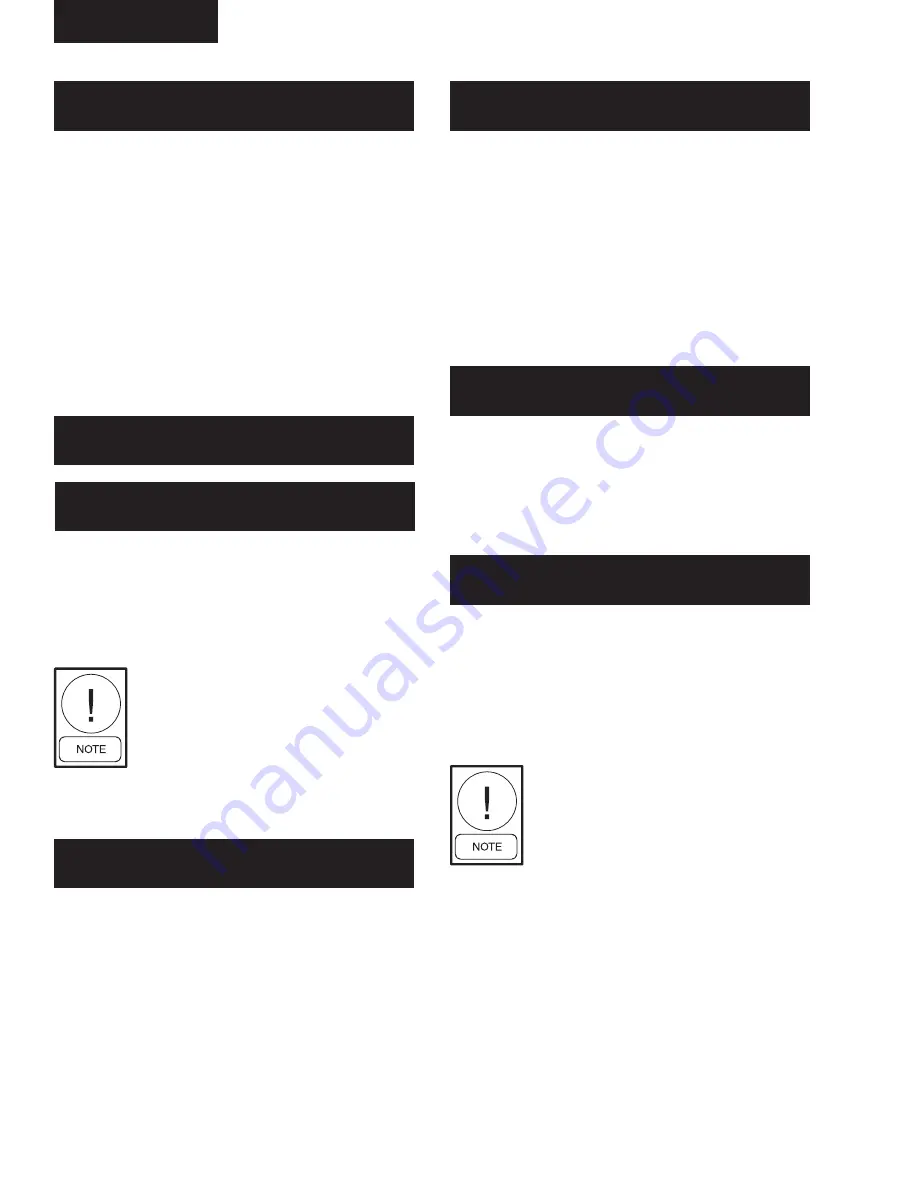
JOHNSON CONTROLS
136
FORM 150.67-NM2 (209)
Unit Controls
S Y S X S P = 7 2 . 1 P S I G
D
P =
2
2
7 . 0 P
S
I
G
These displays show suction and discharge pressures
for each system. The discharge pressure transducer is
optional on some models.
If the
optional
discharge transducer is not installed, the
discharge pressure would display 0 PSIG (0 barg).
The minimum limits for the display are:
Suction Pressure: 0 PSIG (0 barg)
Discharge Pressure: 0 PSIG (0 barg)
The maximum limits for the display are:
Suction Pressure: 400 PSIG (27.58 barg)
Discharge Pressure: 650 PSIG (44.82 barg)
The above two messages will appear sequentially for
each system. The first display shows accumulated
running hours of each compressor for the specific
system. The second message shows the number of starts
for each compressor on each system.
Run times and starts will only be dis-
played for the actual number of sys-
tems and compressors on the unit.
A total of 99,999 hours and starts can be logged before
the counter rolls over to “0”.
This display of the load and unload timers indicate
the time in seconds until the unit can load or unload.
Whether the systems loads or unloads is determined by
how far the actual liquid temperature is from setpoint.
A detailed description of unit loading and unloading is
covered under the topic of Capacity Control.
The display of COOLING DEMAND indicates the
current “step” in the capacity control scheme when in
Return Water Control Mode. The number of available
steps are determined by how many compressors are in
the unit. In the above display, the “2” does not mean
that two compressor are running but only indicates that
the capacity control scheme is on step 2 of 8. Capacity
Control is covered in more detail in this publication
which provides speci
fi
c information on compressor
staging (for Return Water Control only).
The COOLING DEMAND message will be replaced
with this message when Leaving Chilled liquid control
is selected. This message indicates the temperature
error and the rate of change of the chilled liquid
temperature.
This display indicates the current LEAD system. In this
example system 2 is the LEAD system, making system
1 the LAG system. The LEAD system can be manually
selected or automatic. Refer to the programming under
the “OPTIONS” key. The Lead System display will only
appear on a two system unit.
S
Y S X H O U R S 1 = X X X X X
2 = X X X X X, 3 = X X X X X
C O O L I N G D E M A N D
2 O F 8 S T E P S
L O A D T I M E R 5 8 S E C
U N L O A D
T I M E R 0 S E C
S Y S X S T A R T S 1 = X X X X X
2 = X X X X X, 3 = X X X X X
T E M P E R R O R X X X . X ° F
T E M P R A T E X X X . X ° F / M
L E A D S Y S T E M I S
S Y S T E M N U M B E R 2
A unit utilizing hot gas bypass should
be programmed for MANUAL with
system 1 as the lead system. Failure
to do so will prevent hot gas operation
if system 2 switches to the lead system
when programmed for AUTOMATIC
LEAD/LAG.
Summary of Contents for YCAL0019
Page 55: ...FORM 150 67 NM2 209 55 JOHNSON CONTROLS 5 5 ELEMENTARY WIRING DIAGRAM CON T LD12699D...
Page 57: ...FORM 150 67 NM2 209 57 JOHNSON CONTROLS 5 5 ELEMENTARY WIRING DIAGRAM CON T LD12693C...
Page 59: ...FORM 150 67 NM2 209 59 JOHNSON CONTROLS 5 5 ELEMENTARY WIRING DIAGRAM CON T LD 12198...
Page 61: ...FORM 150 67 NM2 209 61 JOHNSON CONTROLS 5 5 LD12702 ELEMENTARY WIRING DIAGRAM CON T...
Page 63: ...FORM 150 67 NM2 209 63 JOHNSON CONTROLS 5 5 LD12696 ELEMENTARY WIRING DIAGRAM CON T...
Page 65: ...FORM 150 67 NM2 209 65 JOHNSON CONTROLS 5 5 CONNECTION WIRING DIAGRAM CON T LD12703B...
Page 67: ...FORM 150 67 NM2 209 67 JOHNSON CONTROLS 5 5 CONNECTION WIRING DIAGRAM CON T LD12697B...