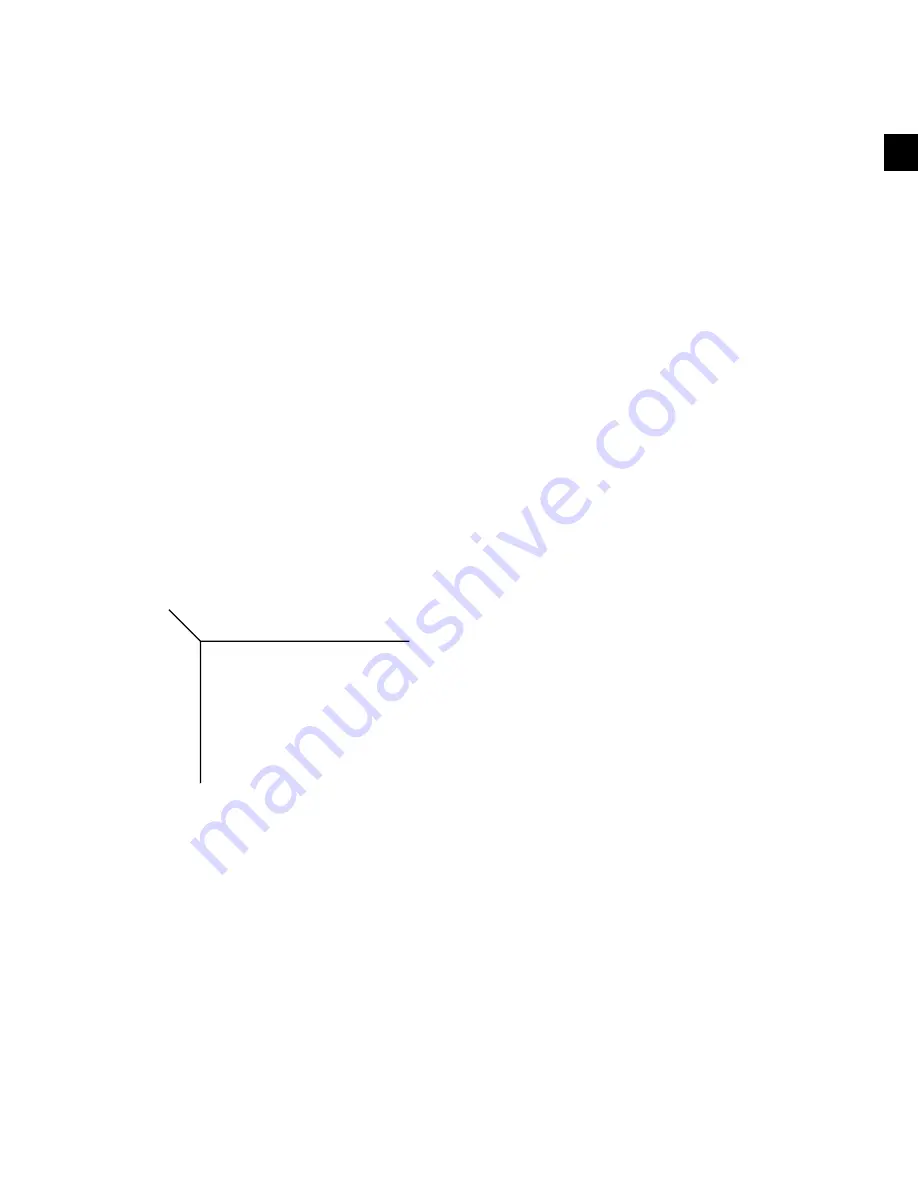
171
YORK INTERNATIONAL
FORM 201.19-NM6 (804)
8
Slide Valve Control
The slide valve of each compressor can be moved 75
steps, where “0” equals minimum capacity and fully
load ed equals 75 steps. The amount of movement that
occurs when the micro initiates changes may vary ac-
cord ing to the error or deviation from setpoint and the
rate of change of chilled liquid temperature. Each time a
change is made, the incremental change may vary from
1 to 10 steps as determined from the micro. In cases
where internal limiting is not in effect due to pos si ble
fault conditions, the micro will load the com pres sor with
the lowest number of steps, alternating loading back and
forth between compressors until both are fully load ed.
In some cases the micro will be required to make de-
ci sions regarding loading under conditions where the
temperature “er ror” and temperature “rate” confl ict. For
example, the micro may elect to unload a compressor
if the error is “0” (tem per a ture is at setpoint), while the
rate of change of chilled liquid temperature is negative
(falling). The micro may also elect to hold capacity when
error is “+” (tem per a ture is above setpoint) because the
rate of change of chilled liquid is “-”. Below is a chart
which illustrates these conditions.
Load Timers
Fixed timers are set to minimize undershoot and over-
shoot as a result of slide valve control.
• Load Timers are always set at 10 seconds be tween
changes.
• Unload Timers are set at 5 seconds between
changes.
Slide Valve Position
A slide valve position (S V STEP), under the keypad
system keys, of 75 indicates that the compressor is
ful ly loaded. However due to the non-exact movement
of the mechanism, a position less than 75, possibly 60,
could also mean that the compressor is fully loaded. A
compressor may also be fully unloaded at step 35 and
below. Keep this potential indicator error in mind when
attempting to de ter mine slide valve position versus actual
com pres sor capacity.
Compressor Starting & Loading Sequence
If no compressors are running, the Daily Schedule
per mits, all safeties and run permissives are satisfi ed,
the anti-recycle timers have timed out, and the leaving
liq uid temperature rises above the upper range limit of
the Con trol Range, the lead compressor will be started.
A 0VDC signal is sent to the compressor slide valve
con trol solenoid to allow the internal spring to push the
slide valve to a minimum loading position to assure it is
fully unloaded at start. At the same time, the micro will
energize (open) the pilot solenoid on the EEV. After
an ini tial period of 15 seconds, the micro will begin to
load up the lead com pres sor to bring the chilled liquid
tem per a ture to setpoint.
After 5 minutes of run time, if leaving chilled liquid
temperature is not within the Control Range, the micro
will start the lag compressor. This is not dependent on
slide valve position which after 5 minutes will typically
be fully loaded at a S V Step of “75”. The lead compres-
sor will be reduced in capacity to a slide valve step of
40. The lag compressor will then be load ed until it also
reaches a slide valve step of 40 while the lead compressor
is maintained at a constant load. At this point the com-
pressors will be alternately loaded with loading always
occurring on the compressor with the lowest slide valve
step until the leaving chilled liq uid is satisfi ed.
On 3 compressor chillers, if the two compressors can not
bring the load under control within 10 minutes, the
micro will maintain the lead compressor fully loaded
at S V Step 75, unload the fi rst lag compressor to Step
40, and bring on the 2nd lag compressor. The second
lag compressor will load until it reaches Step 40. From
this point the compressors will be alternately loaded,
al ways loading the compressor with the least step of
loading fi rst.
On 4 compressor chillers, loading will operate the same
as a 3 compressor chiller with another compressor
add ed to the sequence. If the load cannot be brought
under control in 15 minutes, the 3rd lag compressor
(com pres sor 4) will be started. Before starting the 3rd
lag compressor, the lead and 1st lag compressor will be
maintained at full load (S V Step 75) and the 2nd lag
compressor will be unloaded to S V Step 40. If load
continues to rise, the 2nd and 3rd lag compressor will
be alternately loaded until the leaving chilled liquid
temperature is satisfi ed.
ERROR
Negative Unload Unload Hold
Zero Unload Hold Load
Positive Hold Load Load
RATE
Negative Zero Positive
Summary of Contents for YCAS
Page 43: ...43 YORK INTERNATIONAL FORM 201 19 NM6 804 5 This page intentionally left blank...
Page 45: ...45 YORK INTERNATIONAL FORM 201 19 NM6 804 6 This page intentionally left blank...
Page 65: ...65 YORK INTERNATIONAL FORM 201 19 NM6 804 7 LD09359 Electronic Panel 035 19205 104 Rev A...
Page 81: ...81 YORK INTERNATIONAL FORM 201 19 NM6 804 LD09378 CONNECTION WIRING DIAGRAM Electronic Panel...
Page 91: ...91 YORK INTERNATIONAL FORM 201 19 NM6 804 This page intentionally left blank...
Page 147: ...147 YORK INTERNATIONAL FORM 201 19 NM6 804 8 This page intentionally left blank...
Page 205: ...205 YORK INTERNATIONAL FORM 201 19 NM6 804 8 This page intentionally left blank...