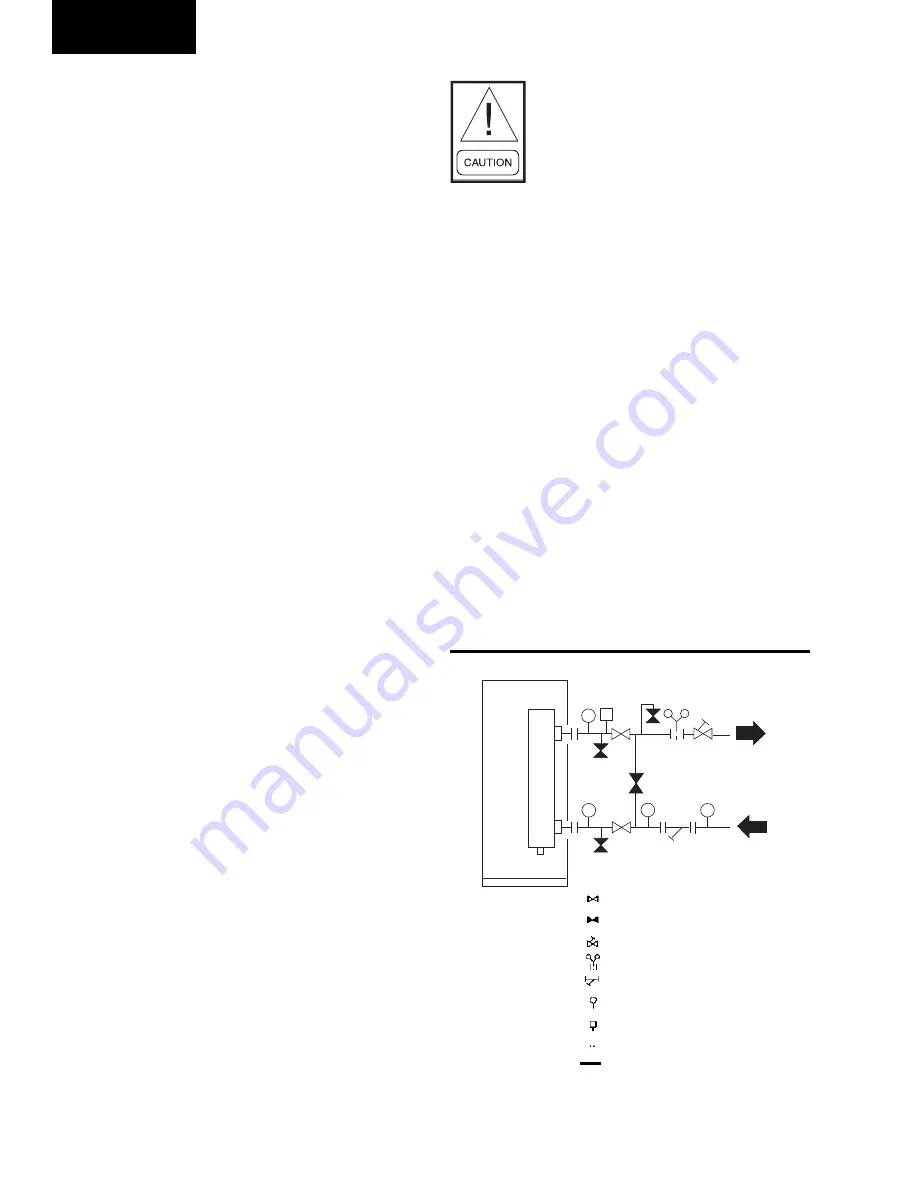
32
YORK INTERNATIONAL
FORM 201.19-NM1 (204)
FIG. 6 –
PIPEWORK ARRANGEMENT
Pipework and
fi
ttings must be separately supported to
prevent any loading on the evaporator. Flexible con-
nec tions are recommended which will also minimize
transmission of vibrations to the building.
Flexible
connections must be used if the unit is mounted on
anti-vibration mounts as some movement of the unit
can be ex pect ed in normal operation
.
Pipework and
fi
ttings immediately next to the evapora-
tor should be readily de-mountable to enable cleaning
be fore operation, and to facilitate visual inspection of
the exchanger nozzles.
The evaporator must be protected by a strainer, pref-
er a bly of 30 mesh,
fi
tted as close as possible to the
liq uid inlet connection, and provided with a means
of local isolation.
The evaporator must not be exposed to
fl
ushing veloci-
ties or debris released during
fl
ushing. It is recommended
that a suitably sized by-pass and valve arrangement is
in stalled to allow
fl
ushing of the pipework system. The
by-pass can be used during maintenance to isolate the
heat exchanger without disrupting
fl
ow to other units.
Thermometer and pressure gauge connections should
be provided on the inlet and outlet connections of each
evaporator.
Drain and air vent connections should be provided at all
low and high points in the pipework to permit drain age
of the system and to vent any air in the pipes.
Liquid systems at risk of freezing, due to low ambient
temperatures, should be protected using insulation and
heater tape and/or a suitable glycol solution. The liquid
pump(s) must also be used to ensure liquid is cir cu lat ed
when the ambient temperature approaches freez ing
point. Insulation should also be installed around the
evaporator noz zles. Heater tape of 21 watts per meter
un der the insulation is recommended, supplied in de -
pen dent ly and controlled by an ambient temperature
ther mo stat set to switch on at 37°F (21°C) above the
freez ing tem per a ture of the liquid.
The liquid circulation pump must be controlled by the
unit. This will ensure that when the liquid temperature
falls within 3° or 5°F (2° or 3°C) of freez ing, the pump
will start.
The evaporator is protected by heater mats un der the in-
su la tion which are supplied from the unit con trol system
pow er supply. Dur ing risk of freezing the control sys tem
should be powered to provide the freeze pro tec tion func-
tion un less the liq uid systems have been drained.
Any debris left in the water pipework
be tween the strain er and evaporator
could cause se ri ous damage to the
tubes in the evaporator and must be
avoided. The in stall er/user must also
en sure that the quality of the wa ter
in cir cu la tion is ad e quate, with out
any dis solved gas es which can cause
ox i da tion of steel parts within the
evaporator.
WATER TREATMENT
The unit performance given in the Design Guide is based
on a fouling factor of 0.00025 ft
2
hr°F/Btu (0.044m2/hr
°C/kW). Dirt, scale, grease and cer tain types of water
treat ment will ad verse ly affect the heat ex chang er sur-
fac es and there fore unit per for mance. Foreign mat ter
in the water system(s) can increase the heat ex chang er
pres sure drop, reducing the
fl
ow rate and caus ing po-
ten tial damage to the heat exchanger tubes.
Aerated, brackish or salt water is not recommended for
use in the water system(s). YORK recommends that a
wa ter treatment specialist is consulted to determine the
proposed water composition will not affect the evap o -
ra tor materials of carbon steel and copper. The pH val ue
of the water
fl
owing through the evaporator must be kept
be tween 7 and 8.5.
Installation
LD04739
Pipework
Isolating Valve - Normally Open
Isolating Valve - Normally Closed
Flow Regulating Valve
Flow Measurement Device
Strainer
Pressure Tapping
Flanged Connection
Flow Switch
Water
Out
Water
In
Summary of Contents for YCAS0130
Page 45: ...45 YORK INTERNATIONAL FORM 201 19 NM1 204 5 This page intentionally left blank...
Page 47: ...47 YORK INTERNATIONAL FORM 201 19 NM1 204 6 This page intentionally left blank...
Page 63: ...63 YORK INTERNATIONAL FORM 201 19 NM1 204 This page intentionally left blank 7...
Page 73: ...73 YORK INTERNATIONAL FORM 201 19 NM1 204 LD09239 FIG 22B CONTROL PANEL COMPONENT LOCATION 7...
Page 75: ...75 YORK INTERNATIONAL FORM 201 19 NM1 204 7 LEGEND LD09241...
Page 77: ...77 YORK INTERNATIONAL FORM 201 19 NM1 204 7 CONNECTION DIAGRAM SYSTEM WIRING LD09242...
Page 78: ...78 YORK INTERNATIONAL FORM 201 19 NM1 204 Technical Data COMPRESSOR TERMINAL BOX LD09243...
Page 79: ...79 YORK INTERNATIONAL FORM 201 19 NM1 204 7 LD09373 ELEMENTARY DIAGRAM CONTROL CIRCUIT...
Page 81: ...81 YORK INTERNATIONAL FORM 201 19 NM1 204 7 This page intentionally left blank...
Page 121: ...121 YORK INTERNATIONAL FORM 201 19 NM1 204 7 This page intentionally left blank...
Page 193: ...193 YORK INTERNATIONAL FORM 201 19 NM1 204 8 This page intentionally left blank...