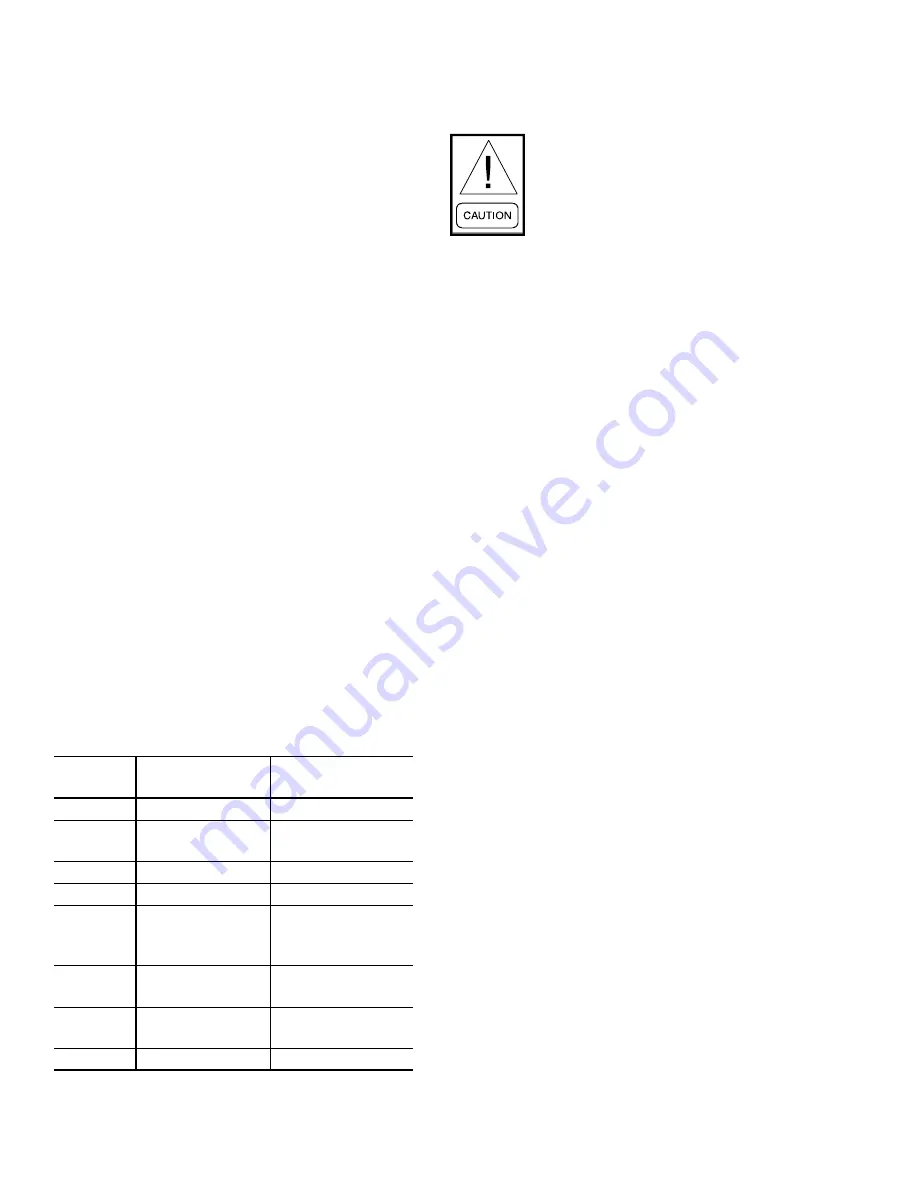
FORM 201.19-CL2 (309)
6
JOHNSON CONTROLS
13. Be certain all water temp sensors are inserted
completely in their respective wells and are
coated with heat conductive compound.
14.Assure that evaporator EEV bulbs are strapped
onto the suction lines at 4 or 8 o’clock posi-
tions.
15. Assure that the 15 ton economizer TXV
bulbs are strapped onto the compressor
economizer supply lines at 4 or 8 o’clock posi-
tions.
16. Assure that the Flow Switch is properly installed,
wired correctly, and working.
17. Assure bolts through compressor feet to bottom
frame rails are removed.
PAnEL CHECkS
(Power On – Both System Switches “OFF”)
1. Apply 3-phase power and verify its value.
2. Apply 115VAC and verify its value on the ter-
minal block in the lower left of the Power Panel.
Make the measurement between terminals 5 and
2. The voltage should be /- 10%.
3. Assure the heaters on each compressor are on.
Allow the compressor heaters to remain on a
minimum of 24 hours before start- up. This is
important to assure that no refrigerant is in the
compressor oil at start-up!
4. Program the dip switches on the microprocessor
board for the desired operating requirements.
OPEN = Left side of switch pushed down.
CLOSED = Right side of switch pushed down.
SwItCH
SwItCH "OPEn"
SEttIng
SwItCH "CLOSED"
SEttIng
1
Water Cooling
Glycol Cooling
2
Standard Ambient
Control
Low Ambient Control
3
Refrigerant R-407C
Refrigerant R-22
4
Do Not Use
YCAS
5
Do Not Use
Motor Current
Averaging (Start-Up)
Disabled
6
Heat Recovery
Disabled
Do Not Use
7
Expansion Valve
Thermostatic
Expansion Valve
Electronic*
8
Spare
Spare
*Expansion valve electronic should always be selected when an
EEV is installed.
Verify the selections by pressing the OPTIONS Key on
the control panel. Check them off in the chart above.
Damage to the chiller could result if
switches are improperly pro-
grammed.
5. Program the required operating values into the
micro for cut-outs, safeties, etc. and record them
in the chart below.
Record programmed values in the chart below.
PROgRAmmED VALUES
Display Language = _____________________________
Discharge Press Cutout = _______________ PSIG (kPa)
Discharge Press Unload = _______________ PSIG (kPa)
Suction Press Cutout = _________________ PSIG (kPa)
High Amb Cutout = ________________________°F (°C)
Low Amb Cutout = _________________________°F (°C)
Leaving Chilled Liquid Temp Cutout = __________°F (°C)
High Motor Current Unload = _________________ % FLA
Anti-Recycle Time = ________________________ Secs
Local / Remote Mode = __________________________
Display Units = _______________________________
Lead / Lag Control = ____________________________
Power Failure Restart = _________________________
Suction Superheat Setpoint = _______________°F (°C)
6. Program the Chilled Liquid Setpoint/Range and
record:
Setpoint = __________________ °F (°C)
Range =
+/-
________________ °F (°C)
Keep in mind that the setpoint temperature
displayed by the micro should equal the desired
leaving water temperature.
7. Assure that the CLK jumper J18 on the Micro-
processor Board is in the ON position (Top 2
pins).
8. Set the Time and Date.