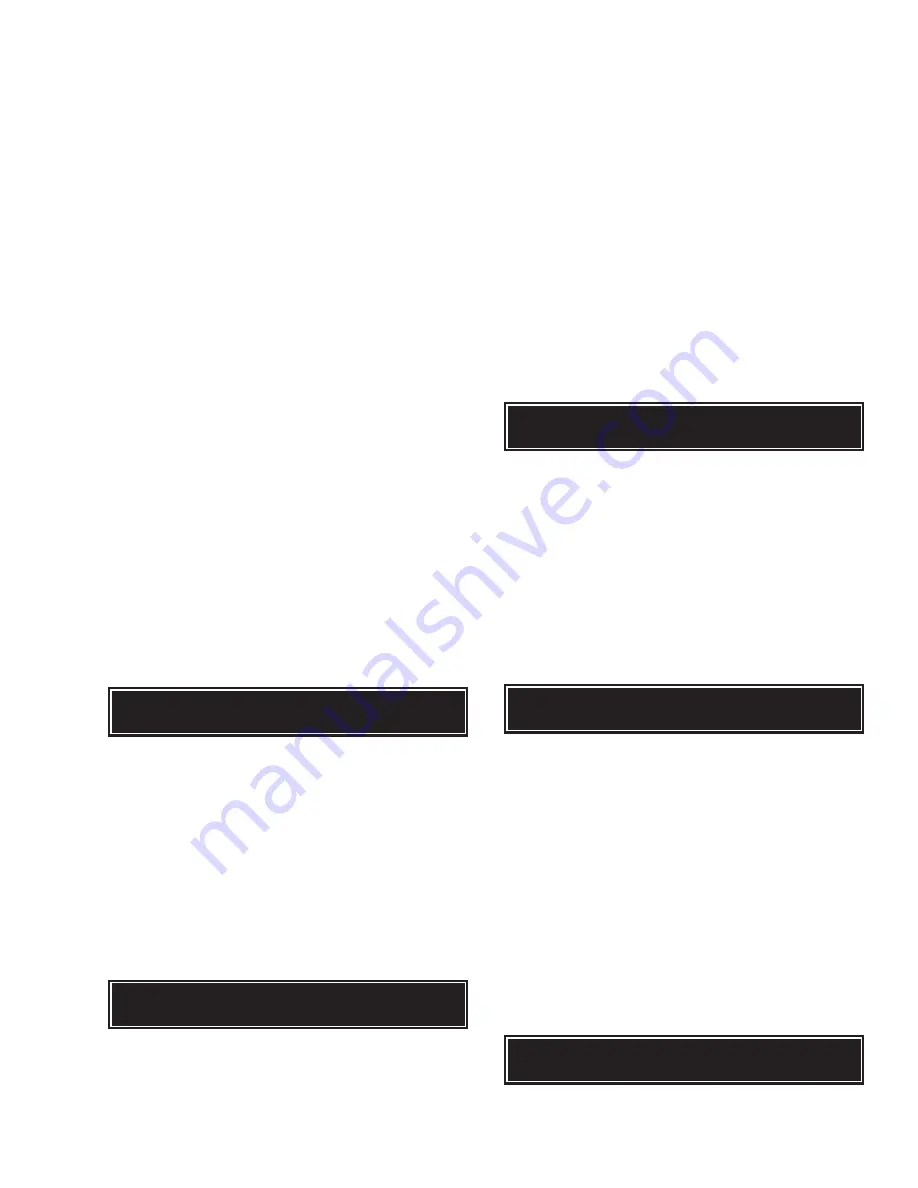
FORM 150.24-NM27
YORK INTERNATIONAL
69
plies 115VAC to the motor protector closing the MP con-
tact. A fault lock-out will result if safety thresholds are
exceeded three times in a 90 minute period.
Suction Pressure Safety
The Suction Pressure Safety assures that the system is
not run under low refrigerant conditions or due to a prob-
lem which will not allow proper refrigerant flow.
For the first 30 seconds of operation, the low suction
pressure bypass is in operation. After 30 seconds of
operation, the micro begins monitoring suction pressure
and continues to do so as long as the compressor runs.
For operation periods of 30 seconds to 240 seconds,
suction pressure must be greater than 50% of the Suc-
tion Pressure Cut-out. After 240 seconds, suction pres-
sure must be greater than the cut-out.
NOTE: A transient timer is built into software to assure
that short term fluctuations in suction pressure
due to fan cycling, loading, etc. do not cause
nuisance trips on low suction pressure.
After the system has pumped down and suction
pressure reaches cut-out plus 5 PSIG, the tran-
sient timer is readied for action. If suction pres-
sure drops below the cut-out point, the 120 sec-
ond transient timer begins timing. As long as
suction pressure doesnt drop below 50% of
cut-out during the 120 second period and rises
above cut-out before the timer times out, the
system will continue to run.
The Suction Pressure Safety Cut-out is programmable
by the user (page 54). An example of a suction pressure
fault message is shown below:
Discharge Pressure Safety
The Discharge Pressure Safety assures that the sys-
tem pressure does not exceed safe working limits which
could open a relief valve or other pressure relief device
causing refrigerant loss.
This safety is a back-up for the mechanical safety in the
system. Anytime the cut-out point is exceeded, the sys-
tem will shut down.
The Discharge Pressure Safety Cut-out is programma-
ble by the user (Page 51). An example of a discharge
pressure fault display message is shown below.
NOTE: This safety is only operable if optional discharge
pressure transducers are installed.
Oil Pressure Safety
The Oil Pressure Safety assures that the compressors
mechanical components receive proper lubrication. The
micro begins monitoring compressor oil pressure after 4
seconds of operation. For operating periods of 4 sec-
onds to 30 seconds, oil pressure must be greater than 5
PSID. From 30 seconds to 240 seconds, oil pressure
must be greater than 20 PSID. After 240 seconds, oil
pressure must be greater than 25 PSID for as long as
the compressor continues to run. If the required oil pres-
sure limits are not met, the system will shut down.
The micro computes differential oil pressure by meas-
uring oil pump pressure and subtracting suction pres-
sure (Oil - Suction = Oil PSID).
An example of an oil pressure fault display message is
shown below.
Pumpdown Safety *
The Pumpdown Safety assures that a compressor does
not run unless it completes a proper pumpdown. This
prevents operation of a refrigerant system which has a
leaking liquid line solenoid valve.
On start-up, the system must pump down to the Suction
Pressure Cut-out within 300 seconds or the system will
shut down.
An example of the Pump down fault display message is
shown below.
NOTE: LLSV refers to liquid line solenoid valve.
High Oil Temp Safety
* *
This safety protects the compressor from catastrophic
failure by sensing when an internal problem occurs that
causes high internal compressor temperatures. It also
protects the compressor from overheating due to improper
cooling from hot suction gas, high water temperatures,
or high discharge pressures.
The compressor will shut down whenever the sump tem-
perature exceeds 180°F for the first minute of operation
or 160°F after one minute of operation.
An example of Oil Temp Inhibit safety display is shown
below:
S Y S # 1
L O W
S U C T I O N
S Y S # 2
L O W
S U C T I O N
S Y S # 1
L O W
O I L
P R E S S
S Y S # 2
L O W
O I L
P R E S S
S Y S # 1
H I G H
D S C H
S Y S # 2
H I G H
D S C H
S Y S # 1
L L S V
N O T
O N
S Y S # 2
L L S V
N O T
O N
S Y S # 1
H I G H
O I L
T E M P
S Y S # 2
H I G H
O I L
T E M P
* This safety applies to chillers with 031-01096-001 and early versions of 031-01652-001 EPROMs.
** This safety applies to chillers with later versions of 031-01652-001 (CRCP Version) EPROMs, I/O Expansion Board, and Oil Temp Sensors.
Summary of Contents for YCRJ45E00
Page 29: ...FORM 150 24 NM27 YORK INTERNATIONAL 29 CONTROL CIRCUIT With I O Expansion Board LD02106 ...
Page 30: ...30 YORK INTERNATIONAL FIG 9 SYSTEM WIRING ...
Page 31: ...FORM 150 24 NM27 YORK INTERNATIONAL 31 LD02678 ...
Page 35: ...FORM 150 24 NM27 YORK INTERNATIONAL 35 LD02679 ...
Page 36: ...36 YORK INTERNATIONAL MICROPANEL CONNECTION DIAGRAM With I O Expansion Board LD02107 ...
Page 37: ...FORM 150 24 NM27 YORK INTERNATIONAL 37 LD02108 ...