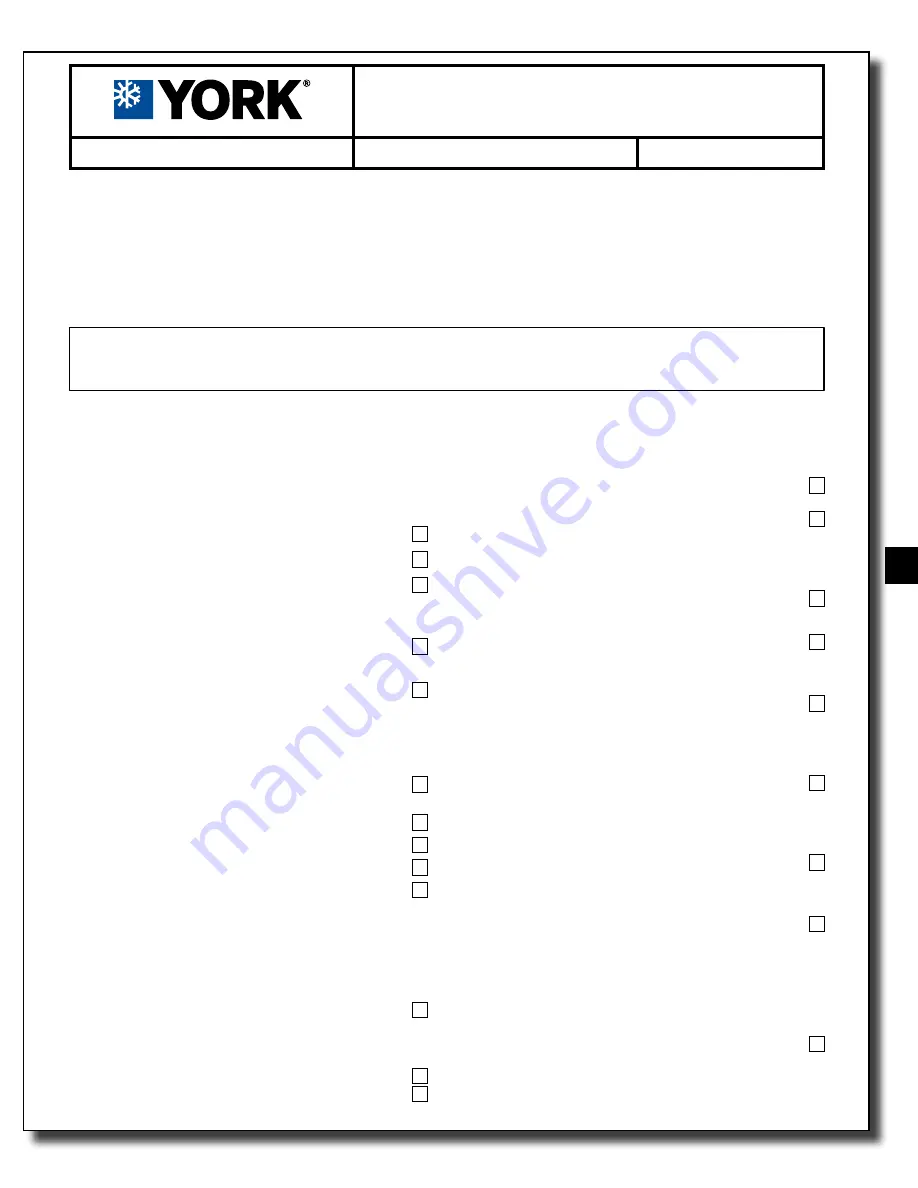
JOHNSON CONTROLS
119
SECTION 6 – COMMISSIONING
FORM 150.72-ICOM6
ISSUE DATE: 08/03/2022
6
c. Check the tightness of the power wiring inside
the power panel on both sides of the motor
contactors and overloads ....................................
d. Check that the BAS control is wired correctly
and operational ....................................................
9. Check for correct size fuses in main and control
circuits, and verify that the overload setting corre-
sponds with RLA and FLA values in electrical tables
(see Table 8 and Table) ...........................................
10. Ensure that the 120 VAC (110 VAC for 50 Hz units)
Control Power to TB1 has 15 A minimum capacity .....
11. Check that all water temperature sensors are in-
serted completely into their respective wells and
are coated with heat conductive compound .............
12. Check that the evaporator TXV bulbs are strapped
onto the suction lines at four or eight o'clock
positions or suction temperature sensors if EEVs
are installed ..............................................................
13. Check that all sides of the unit have the rec-
ommended amount of space for air ventila-
tion. Refer to
Section 4 - Installation (Form
150.72-ICOM6)
........................................................
14. Check that the cabinet edge clears the insulation
of the cable at the power entry to avoid slicing the
cable ........................................................................
B. COMPRESSOR HEATER
(Power On - 24 Hours Before Start)
Apply 120 VAC and verify its value between terminals
5 and 2 of XTBC2. The voltage should be 120 VAC
(110 VAC for 50 Hz units) plus or minus 10%. ..............
NOTE:
Power must be applied 24 hours before start-up.
Each heater should draw approximately 0.5 A to 1 A.
A. PRE-STARTUP
Unit Checks (No Power)
Turn off the customer power to the unit and perform the
following checks.
1. Inspect the unit for shipping or installation
damage ....................................................................
2. Ensure that all piping has been completed ..............
3. Visually check for refrigerant piping leaks ................
4. If available, open the suction line ball valve, dis-
charge line ball valve, and liquid line valve for each
system ......................................................................
5. At shutdown, check that the oil level is between the
bottom and middle of the oil equalizing sight glass ..
6. Are the water pumps on?
a.
Check and adjust the water pump fl ow rate and
pressure drop across the cooler. Refer to
Operat-
ing Limitations, Section 8 - Technical Data (Form
150.72-ICOM6)
. ...................................................
b.
Is the fl ow switch in place, wired correctly, and
operational? .........................................................
c. Are the chilled water pumps operational? ...........
d.
Is the water system fi lled with water?
..................
e. Is all air purged from the water system? ..............
NOTE:
Any air found in the water system must be
purged before the chiller can start up. Excessive
fl ow may cause catastrophic damage to the heat
exchanger (evaporator).
7. Check that the control panel is free of foreign materi-
al, for example, wires and metal chips .....................
8. Check that all power is wired to the chiller and meets
the following NEC and local codes.
a. High voltage .........................................................
b. Low voltage .........................................................
START-UP CHECKLIST
INSTALLATION CHECKLIST
YLAA
Supersedes 150.72-CL1 (320)
Form 150.72-CL1 (1220)
The following work must be completed in accordance with installation instructions:
CUSTOMER: ____________________________________
ADDRESS: _____________________________________
PHONE: ________________________________________
JCI TEL NO: _____________________
JCI ORDER NO: __________________ JCI CONTRACT NO: ______________
JOB NAME: ____________________________________
LOCATION: ____________________________________
CUSTOMER ORDER NO: _________________________
CHILLER MODEL NO
: ____________________________
The work (as checked below) is in process and will be completed by: _____________ / ____________ /
___________
UNIT SERIAL NO
: _______________________________
Month
Day
Year