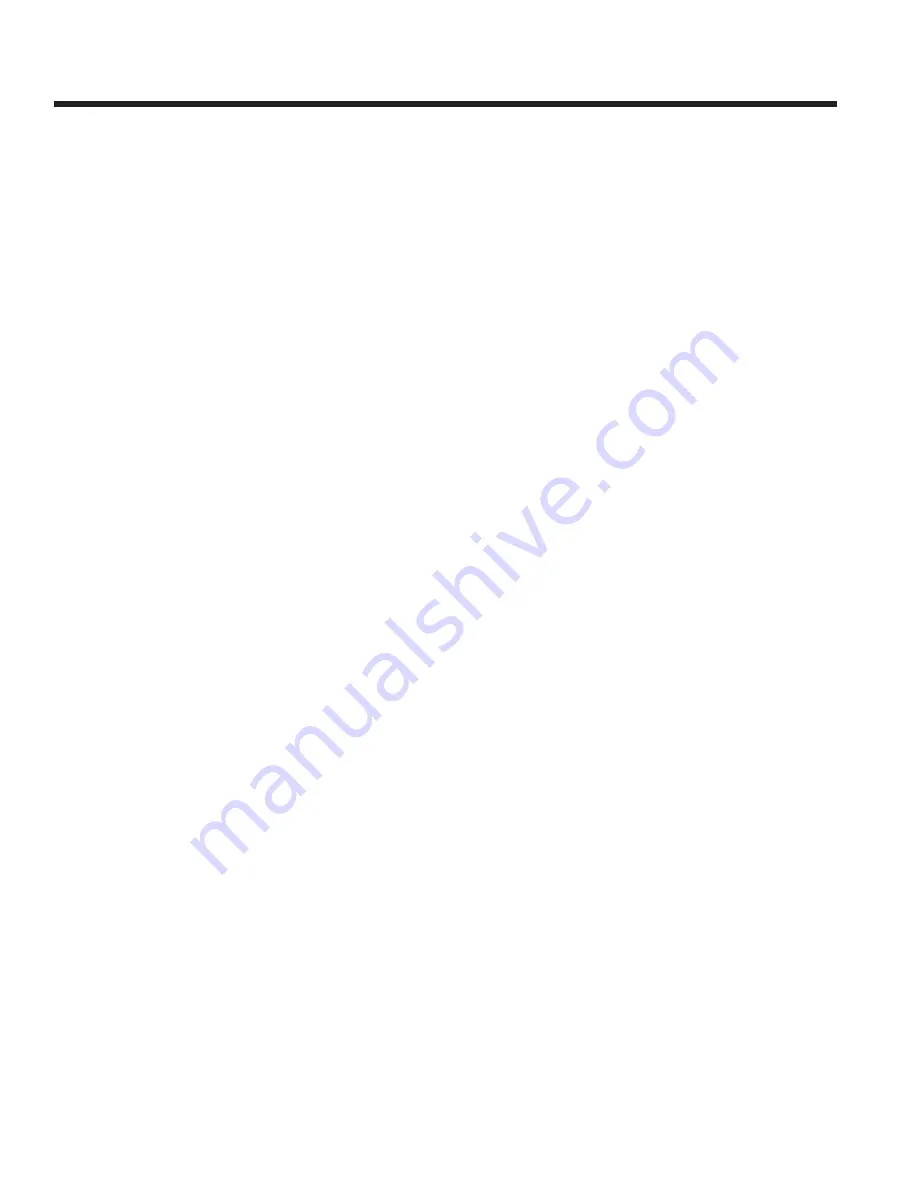
10
JOHNSON CONTROLS
FORM 155.19-EG3 (1011)
Mechanical Specifications - continued
hours, steam valve position and number of starts and
purges.
Warning Conditions
– The MicroComputer Control
Center provides a warning annunciation, when appro
-
priate, limits heat input under the following conditions:
low refrigerant temperature, high generator pressure or
temperature, high or low entering condenser water tem
-
perature, purge pump current overload, faulty solution
dilution temperature sensor.
Safety Controls
– The Control Center includes unique
safety logic designed to protect the Two-Stage chiller from
damaging malfunctions. Complete safety annunciation
is displayed for each shutdown by pressing the status
key. This information includes day, time and reason for
shutdown. These include: solution – or refrigerant – pump
thermal or current overload, low refrigerant temperature,
first-stage generator high pressure or temperature, loss of
chilled water flow, power failure, auxil iary safety shutdown,
incomplete dilution cycle and power failure if manual re
-
start after power failure is selected.
Operating Controls
– Background messages are
dis played while the unit is running to signal operator
of controlling conditions such as leaving chilled water
temperature control and noncritical sensor error. System
cycling messages display day, time, cause of cycling
shutdown, and autostart indication. These include loss of
condenser water (or hot water) flow, low-leaving chilled
water (or high leaving hot water) temperature, and power
failure (when autostart is selected).
Digital programming of operating setpoints from the key
-
pad include leaving chilled water (or hot water) tempera
-
ture, pulldown demand limiting, remote steam demand
limit, remote reset temperature range, and daily start/stop
scheduling of chiller and water pumps with separate holi
-
day schedule.
Security access code is provided for operator to pro gram
setpoints or to choose local, remote, or service modes
of operation. Manual control of the steam valve position
and all pumps is provided through separate buttons in the
service mode of operation.
Data Logging
– All operating and setpoint information
can be transmitted to a remote printer (by others) through
the RS232 port in the control center to obtain data logs.
This can be accomplished at any time by pressing the
“Print” button on the control center, or automatically at
predetermined intervals by program ming the panel’s
data logger. The printer will automat ically record time and
cause of any safety or cycling shutdown along with all
chiller operating data monitored by the panel just prior to
shutdown. A “History Print” button also allows the printout
of the last four causes of cycling or safety shutdowns plus
operating data for each shutdown.
BAS Interface – The MicroComputer Control Center is
compatible with remote Building Automation Systems
(BAS). The standard design allows remote start and
stop; leaving chilled-water temperature reset and steam
demand limit through PWM signal; and “ready-to-start,”
“unit running,” “safety” and “cycling” shutdown status
contact. For designed-in features and reliability, Johnson
Controls provides a full line of BAS controls.
FACTORY LEAK TEST
Each YPC unit is subjected to a series of four rigorous
leak tests, culminating in a vacuum leak test measured
by a mass spectrometer and conducted while the unit is
immersed in an atmosphere of low-density helium.
CODES AND STANDARDS
• ASME Boiler and Pressure Vessel Code - Section VIII
Division 1
• ARI 560-92
• NEC – National Electrical Code
• OSHA – Occupational Safety and Health Act
PAINT
Exterior surfaces are protected by an initial coat of red
oxide primer with a single finish coat of Caribbean-blue
air-drying, high-solids, enamel machinery paint.
SHIPMENT
Protective covering is furnished on the microprocessor
controls, burner and other electric devices. Water noz zles
are capped prior to shipment.