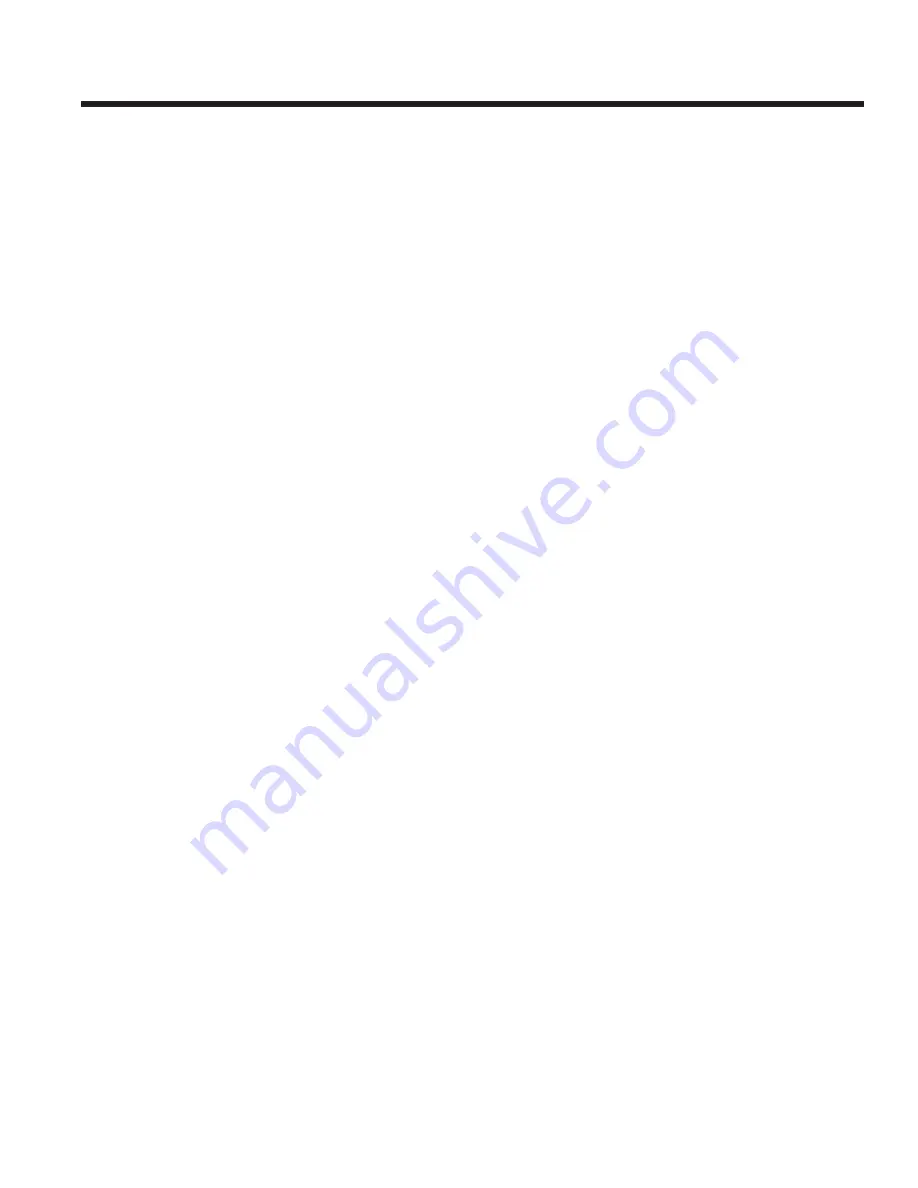
FORM 155.19-EG3 (1011)
23
JOHNSON CONTROLS
All major system components such as chilled water
pumps and condenser water pumps shall be able to be
controlled from the control center panel to start and stop
with the chiller (except as required for safety shutdowns)
to minimize system energy usage.
The pull down demand feature shall permit ramp loading of
input steam flow rate upon unit startup. Programma ble in
-
puts include initial input steam flow rate (30% to maximum)
final input steam flow rate (30% to maxi mum), and duration
of pull down demand period (0 to 255 minutes).
Remote Steam Limit Input
– The remote steam limit
input feature shall permit the limiting of input steam flow
rate when the unit is operating in the remote mode at any
time from 30% to maximum based upon a remote 1 to 11
second pulse width modulated (PWM) signal. An optional
field installed card file and card shall be available to per
-
mit the following remote pull down de mand signals to be
used in lieu of a 1 to 11 second PWM signal: 4-20mA DC;
0-10VDC; contact closure.
Concentration Calculator
– The micropanel shall
monitor the first-stage generator concentration to prevent
operation at an unsafe concentration. Concentration
shall be tied into both the Warning Conditions and Safety
Shutdown systems. Also included shall be an operator
interface concentration calculator. An operator shall be
able to use the concentration calculator to determine
concentration by inputting a set of conditions. When an
operator inputs any two of three parameters (bromide
solution temperature, saturation temperature, and pres
-
sure), the micropanel shall display the concentration. The
display shall also indicate if the input conditions are in the
crystallization zone.
Data Logging
– The MicroComputer Control Center
Panel shall contain an RS 232 port to enable the trans-
mission of all operating setpoint and shutdown informa-
tion to a remote printer (printer supplied by others). This
transmission can occur as needed or automatically on
predetermined intervals (0.1 to 25.5 hrs). In the case of a
safety or cycling shutdown, the RS-232 port shall transmit
all operating data detected prior to the shut down as well
as the time and cause of the shutdown to a remote printer
(printer supplied by others). In addition, a history of the
last four safety or cycling shutdowns and operating data,
with the exception of power failures, shall be retained in
memory and can be printed as well.
BAS REMOTE CONTROL
A communication interface permitting complete exchange
of chiller data with any BAS System is available with an
optional Metasys™ translator. The Metasys™ translator
also allows BAS System to issue commands to the chiller
to control its operation. Metasys™ translators come in
two models, controlling up to 4 chillers and 8 chillers
respectively.
The ParaFlow MicroComputer Control Center Panel shall
be able to communicate all data accessible from the
keypad to a remote integrated DDC processor through
a single shielded cable. This information will include all
unit temperatures, pressures, safety alarms, and status
readouts for complete integrated plant control, data log
-
ging, and local/remote display of operator information.
The single shielded cable shall also allow the remote
integrated DDC processor to issue operating commands
to the ParaFlow MicroComputer Control Center including
but not limited to the following:
• Remote unit start/stop
• Remote chilled-water temperature reset
• Remote hot-water temperature reset
The ParaFlow MicroComputer Control Center Panel shall
also be capable of providing a limited interface to other
building automation systems in order to permit the fol
-
lowing operations:
• Remote unit start/stop
• Remote chilled-water temperature reset
• Remote hot-water temperature reset
• Remote readout of status including
• Unit ready to start
• Unit operating
• Unit safety shutdown
• Unit cycling shutdown