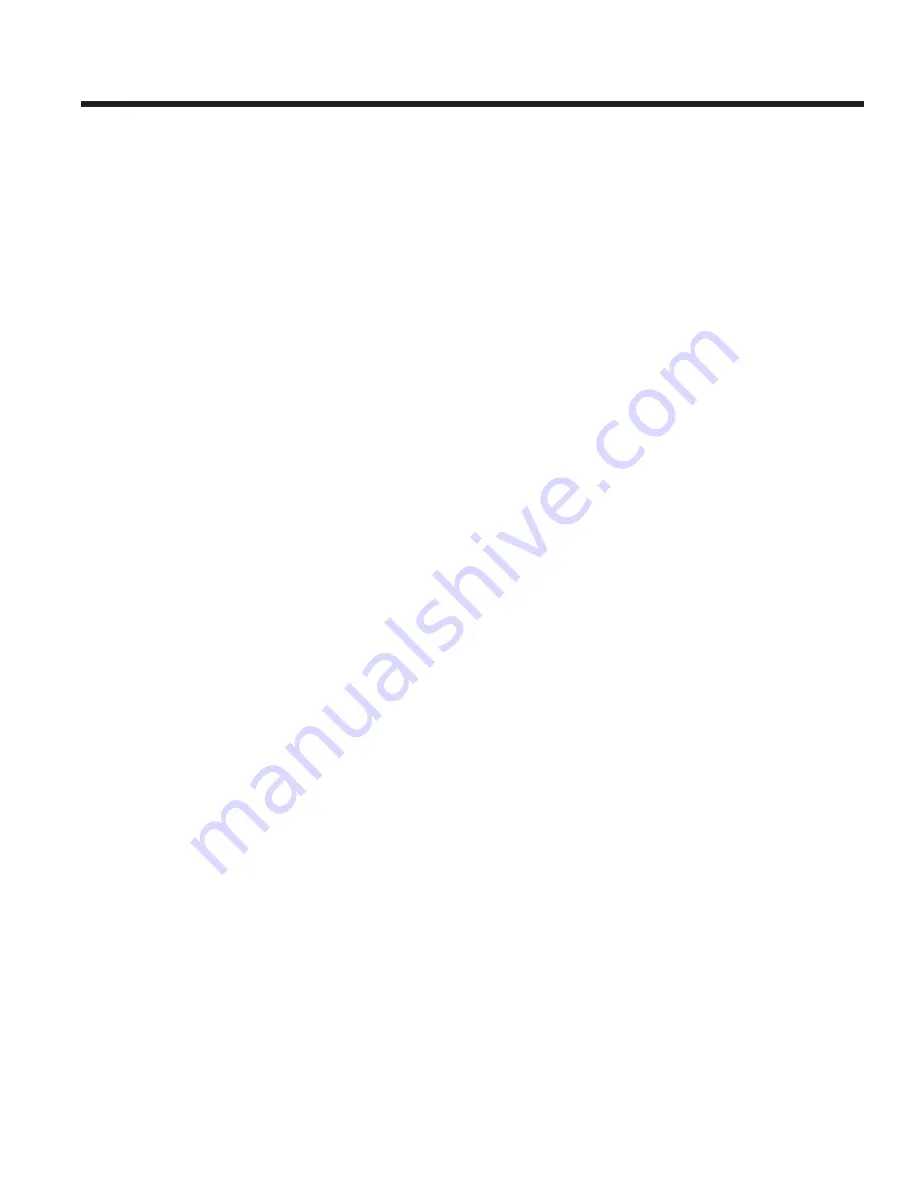
FORM 155.19-EG3 (1011)
7
JOHNSON CONTROLS
WARNING CONDITIONS/INHIBITED UNIT LOADING
The MicroComputer Control Center provides a warning
annunciation and, when beneficial to the machine, will
limit heat input to 30% to 60% when operating conditions
indicate the unit is moving towards a safety shutdown.
This gives the operator the opportunity to fix a problem
before it leads to a complete safety shutdown. Warnings
include the following:
• Low refrigerant temperature
• High generator pressure or temperature
• High or low entering condenser water temperature
• Purge pump current overload
• Faulty solution dilution temperature sensor
SAFETY SHUTDOWN CONTROLS
The following conditions will lead to unit shutdown. After
a shutdown, the reason for the shutdown is dis played in
English on the alphanumeric display. Each annunciation
details the day, time, reason for shutdown and the type
of restart required.
Cycling
– those controls which automatically reset and
permit auto restart of the system.
• Loss of condenser water flow
• Low leaving chilled water temperature
• Power failure (when automatic restart is selected)
Safety
– those controls which (when employed) require
a manual operation to restart the system.
• Solution pump thermal or current overload
• Refrigerant pump thermal or current overload
• Low refrigerant temperature
• First-stage generator high temperature
• First-stage generator high pressure
• Loss of chilled water flow
• Power failure (when automatic restart not used)
• Incomplete dilution cycle due to any of the following:
•
Power failure
•
Solution/refrigerant pump overloads
•
Low refrigerant temperature
•
Loss of chilled water flow
•
Auxiliary safety shutdown terminals for field sup
plied signals
CONCENTRATION CALCULATOR
The micropanel monitors the first-stage generator concen
-
tration to prevent operation at an unsafe concentration.
Concentration is tied into both the Warning Conditions and
Safety Shutdown systems discussed in this section. Also
included is an operator interface concentration calculator.
When in the
PROGRAM
mode, an operator can use the
concentration calculator to determine concentration by
inputting set of conditions. The operator must input any
two of three parameters (bromide solution temperature,
saturation temperature, and pressure) and the micropanel
will display the concentration. The display will also indicate
if the input are in the crystallization zone.
CONTROL MODE SELECTION
The Two-Stage Control Center includes secure program
and servicing capabilities. There are three keys for the
selection of the Control Center modes:
•
ACCESS CODE
permits access to the Control Center
PROGRAM
button when the proper password is given
•
PROGRAM
permits operator to program the set-points
and select desired
MODE
:
•
LOCAL
allows manual unit start and purging.
•
REMOTE
allows purging as well as remote start and
stop of the unit and remote reset of the chilled water
temperature and steam limit.
•
SERVICE
allows manual operation of the steam valve,
including
LOAD, UNLOAD, HOLD
, and
AUTO
keys.
Manual operation of all pumps is also included.
ENERGY MANAGEMENT INTERFACE
By connecting with the Metasys network, the MicroCom
-
puter Control Center can communicate all data accessible
from the keypad (including all temperatures, pressures,
alarms and operating data) to a remote DDC proces
-
sor through a single shielded cable. In
REMOTE
mode,
the DDC processor may issue all operating commands
available at the keypad to the Control Center through the
same shielded cable. With a Metasys network, other BAS
systems can receive this same information.
The MicroComputer Control Center also provides a
direct hard wire interface capability with other building
auto mation systems using a 1-11 PWM standard signal
(4-20mA, 0-10VCD or contact closure optional) includ ing
the following:
• Remote unit start/stop
• Remote chilled water temperature reset
• Remote steam limit input
• Remote read out of status including:
• Unit ready to start
• Unit operating
• Unit safety shutdown
• Unit cycling shutdown