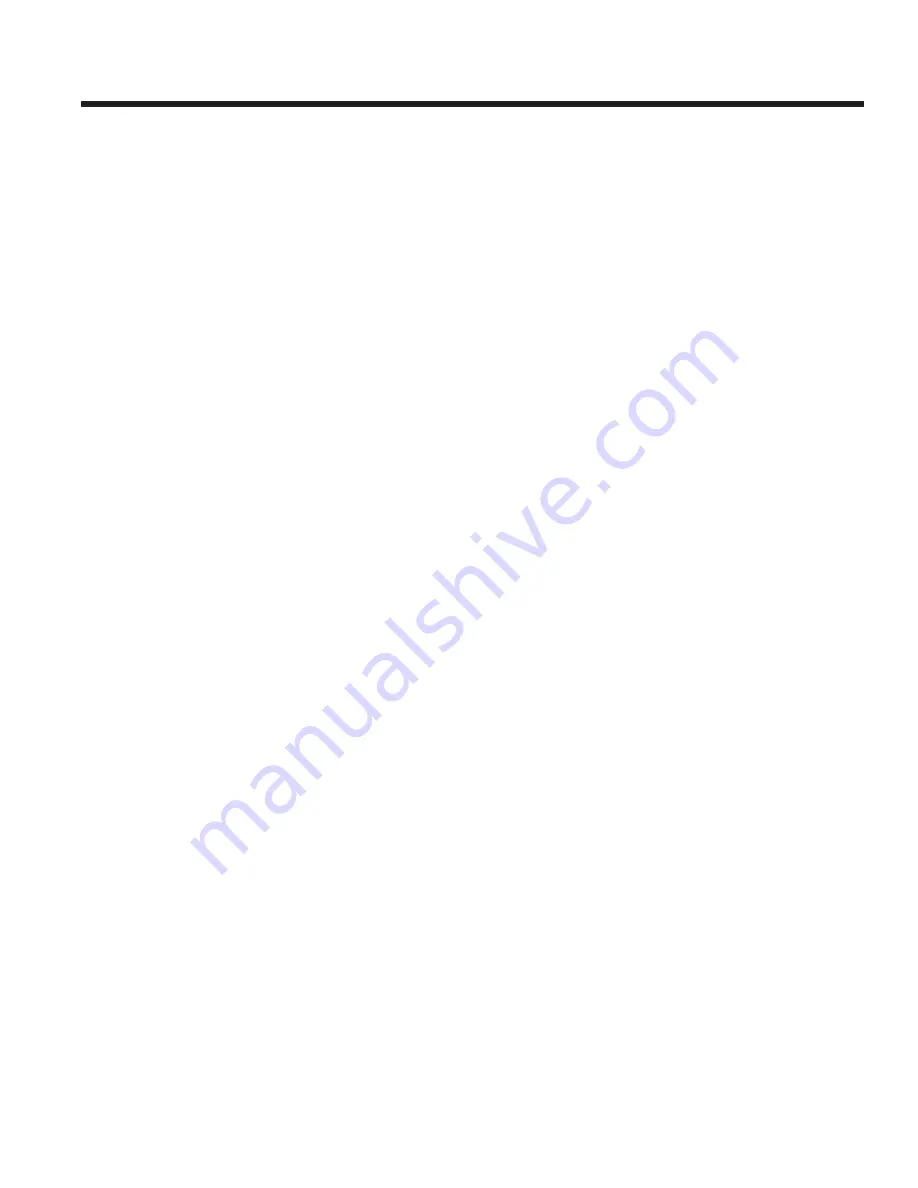
FORM 155.19-EG3 (1011)
9
JOHNSON CONTROLS
condensate cooler on the job site. Each drain cooler is a
shell and tube heat exchanger with a tube side DWP of
150 PSIG (10.3 bar) and a shell side DWP of 29 PSIG
(2 bar). The drain cooler is fabricated from rolled carbon
steel plate with welded seams. Tubes are 5/8” (16 mm)
OD, .030” (0.8 mm) wall, 90/10 cupro-nickel and are geo
-
metrically enhanced to minimize heat stress. Each tube
is roller expanded into a drilled and reamed carbon steel
tube sheet.
PUMPS
Solution and refrigerant pumps are hermetically sealed,
self-lubricating, totally enclosed, liquid cooled, facto
-
ry-mounted, wired and tested. Motor winding are not
exposed to LiBr or water. The suction and discharge
connections for each pump are fully welded to the joint
piping to minimize the opportunity for leaks. Suction and
discharge connections are also equipped with factory
installed isolation valves to permit quick and easy servic
-
ing of pumps. All YPC units include two solution pumps
and a refrigerant pump. Pumps are designed to operate
for a total of 55,000 operating hours between service
inspections.
VALVES
All valves used for adjusting the solution are fully welded
or brazed to prevent leakage of air into the unit. Valve
operators are covered with a seal cap to eliminate the
possibility of air leakage through the stem. Additionally, all
connections of valves to unit piping are fully welded.
SOLUTION AND REFRIGERANT
Each YPC unit is charged with LiBr solution with non-toxic
lithium molybdate (ADVAGuard™ 750) as a corrosion
inhibitor. Refrigerant is deionized water. A small amount
of 2-ethyl hexanol is added as a heat and mass transfer
enhancer.
ADVAGuard™ 750 Corrosion Inhibitor
– is an environ
-
mentally friendly inorganic corrosion inhibitor that provides
superior corrosion protection. Corrosion inhibitors promote
the formation of an oxide film on the surfaces of the
chiller that are in contact with LiBr solution. ADVAGuard
750 corrosion inhibitor creates a highly stable magnetite
layer resulting in lower hydrogen generation and only an
eighth of the corrosion as compared with other traditional
inhibitors.
PURGE SYSTEM
The purge system automatically and constantly removes
noncondensible vapors generated in the absorption pro
-
cess thorough the use of a eductor. Noncondensibles are
then stored in a purge chamber until they can be removed
through the use of a purge pump. The purge pump is an
oil, rotary, two-stage vacuum pump with a 1/4 HP, 3-Phase,
ODP motor.
The chiller control panel includes a SmartPurge system
that will automatically sense the amount of non-conden
-
sibles in the purge chamber and empty the tank whenever
necessary. The SmartPurge system eliminates the need
for an operator to ever manually empty the purge cham
-
ber. In addition, the control panel monitors the frequency
of purge cycles and alerts the chiller operator through a
unique control panel warning message if the number of
purges exceeds normal levels.
CAPACITY CONTROL
Capacity control is accomplished by modulating the steam
valve position. The YPC Steam-Fired unit is capable of
modulating capacity from 20% to 100%.
The YPC chiller design incorporates a float valve that
limits solution flow to the generator as the cooling load de
-
creases. This maintains optimum solution level throughout
the operating range. In addition, manual control valves are
used by Johnson Controls technicians in the factory and/
or at start-up to fine tune solution and refrigerant flows to
match the job site needs at peak efficiency.
POWER PANEL
The power panel enclosure includes the following: single
point wiring connection for the incoming power supply;
non-fused disconnect switch; motor starters, complete
with current and thermal-overload protection for solution
pump(s), refrigerant pump, and purge pump (current
overloads only); 115VAC 50/60 Hz control power trans
-
former.
MICROCOMPUTER CONTROL CENTER
The microprocessor-based control center is factory-mount
-
ed, wired and tested. The electronic panel automatically
controls the operation of the unit in meeting system cool
-
ing requirements while minimizing energy usage. Chiller
operating parameters are sensed by either thermistors
or transducers and displayed on the keypad. All pres
-
sures are taken as absolute to alleviate typical gauge
pressure inaccuracies. Temperatures and pressures can
be displayed in English (F, PSIA) or metric (C, KPa) units
depending on the application. Display of all information
is shown in the English language on a 40-character al
-
phanumeric display.
Available operating information includes return/leaving
chilled water temperatures, return/leaving tower water
temperatures, first-stage generator pressure and tem
-
perature, refrigerant and solution temperatures, operating