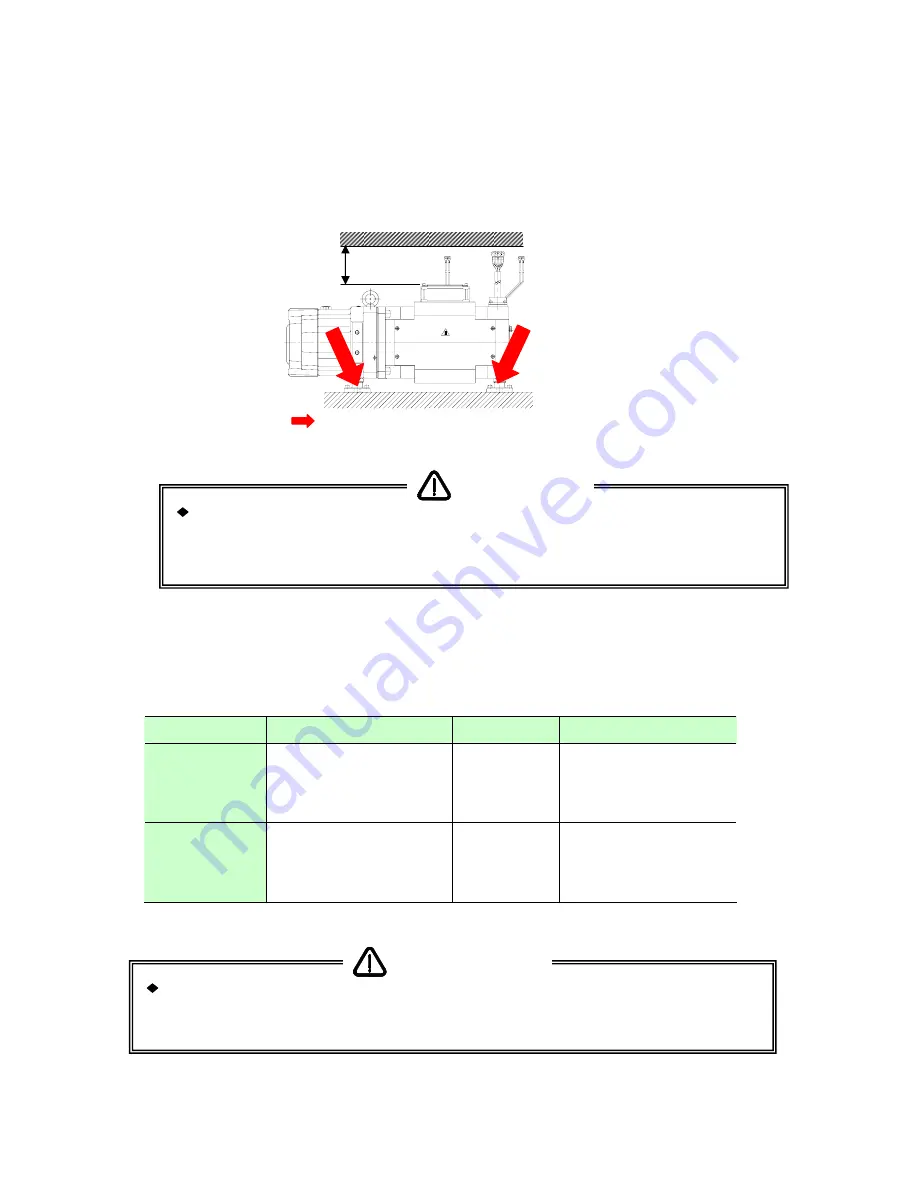
EM-0146-8
- -
21
3.4 Installation of the ASE pump unit
3.4.1 Installation position
- Install the unit with the filling port facing upward.
- Bolt the unit securely using the mounting holes on the bracket.
: Bolt/plain washer location
Fig. 3.4a Installation Example
3.4.2 Bolting
Screw in the bolts listed below gradually and evenly.
Note) Use the washers to prevent the bolts from loosening.
Table 3.4a Bolt Size and Tightening Torque
Use the specified number of bolts of the same material/strength grade and apply the specified
tightening torque. Failure to do so may cause damage to the bolts or outflow of hydraulic fluid,
resulting in a major accident.
150 mm
WARNING
Model
Bolt Size
Quantity
Tightening Torque N•m
ASE3/5-
JIS B1180
Hexagon Head Bolt
M12 (Strength Grade: 6.8
or more)
4
50 to 55
ASE10-
JIS B 1180
Hexagon Head Bolt
M20 (Strength Grade: 6.8
or more)
4
232 to 256
Improper mounting condition of foot blacket, may increase noise level during operation.In
such case, use the anti-vibration rubber or acoustic absorbent to cover the foot blacket and
take apporpriate measures.Continuing the operation under such condition may result in
human injury.
CAUTION