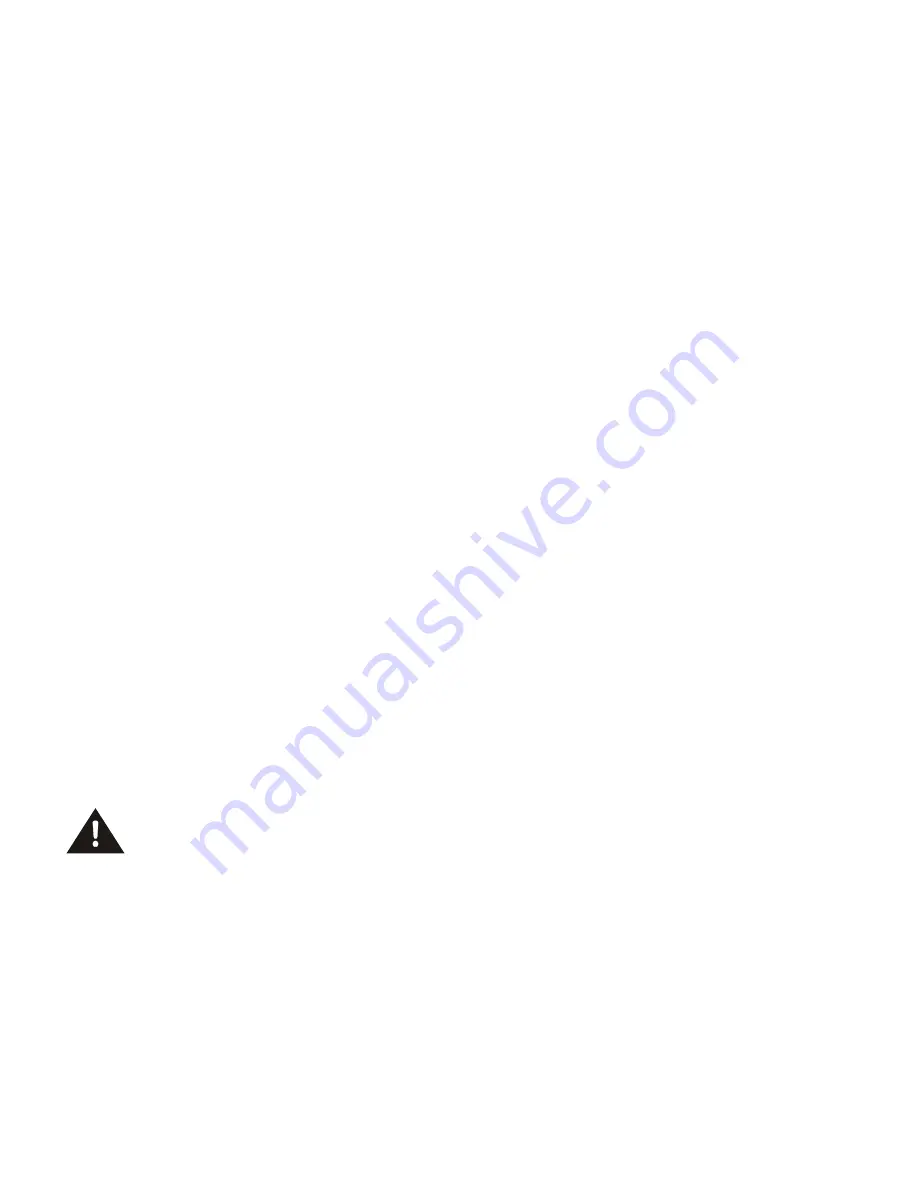
OPERATION INSTRUCTIONS
PRE-STARTUP INSPECTION AND CHECK LIST
After the installation is completed in all respect, the following points should be covered before the system is switched on
for operation.
1. Remove straps & wooden pieces that hold the compressor in place during transportation.
2. Make sure all electrical fasteners/connections are tight and secure.
3. Make sure circuit breakers/fused disconnect switches are properly installed.
4. Make sure all controls are set according to instructions (low & high pressure switch, pump down pressure switch, fan
cycling switch, etc.).
5. Make sure all valves are open (compressor suction and discharge service valves, liquid line valve, etc.).
6. Make sure expansion valve bulb is strapped properly at correct location.
7. Make sure thermostat is installed properly.
8. Follow all the instructions from the warning tags and stickers.
9. Energize compressor crankcase heater for a minimum of 12 hours prior to the system start-up. To energize crankcase
heater only, set thermostat to OFF position and close electrical disconnect switch of the outdoor unit.
10. Inspect condenser coil and other components for any physical damage.
11. Make sure condenser fans are free to turn without wobbling and their mountings are properly tightened.
12. Make sure all refrigerant service valve caps are installed.
13. Make sure all piping, piping insulation and piping supports are properly installed.
14. Connect the manifold gauge to suction and discharge line service valves.
15. Prepare instruments required for checking voltage, Amps, fan RPM etc.
16. Start the unit and observe compressor discharge and suction pressures.
CONTROLS AND SEQUENCE OF OPERATION
The details of the controls and sequence of operation can be found in the corresponding indoor unit catalog.
MAINTENANCE
GENERAL
As with all mechanical equipment, a program of regular inspection, cleaning and preventing maintenance by trained
personnel will contribute greatly to the long satisfactory service life of this product.
Electric shock warning:
Before servicing the unit, make sure that electric power supply is OFF and all
remote disconnects are open. Turning the unit OFF does not mean it is disconnected. Failure to do so might
result in severe injury/death.
MONTHLY INSPECTION
Shut unit down and open main disconnect, wipe down external surfaces of unit, inspect control panel, checking for loose
wires, burned contacts, signs of overheated wires, etc. Restart unit and check performance of controls. Check sight
glasses for proper refrigerant charge.
COIL CLEANING
Dirty coils can be cleaned using a soft brush or by flushing with cool water or commercially available coil cleaners.
DO
NOT USE HOT WATER OR STEAM
in cleaning the coil.
COMPRESSOR MAINTENANCE
Maintenance is limited to visual checking for oil leakage and electrical connections. In case of failure contact Zamil sales/
dealer office.
15