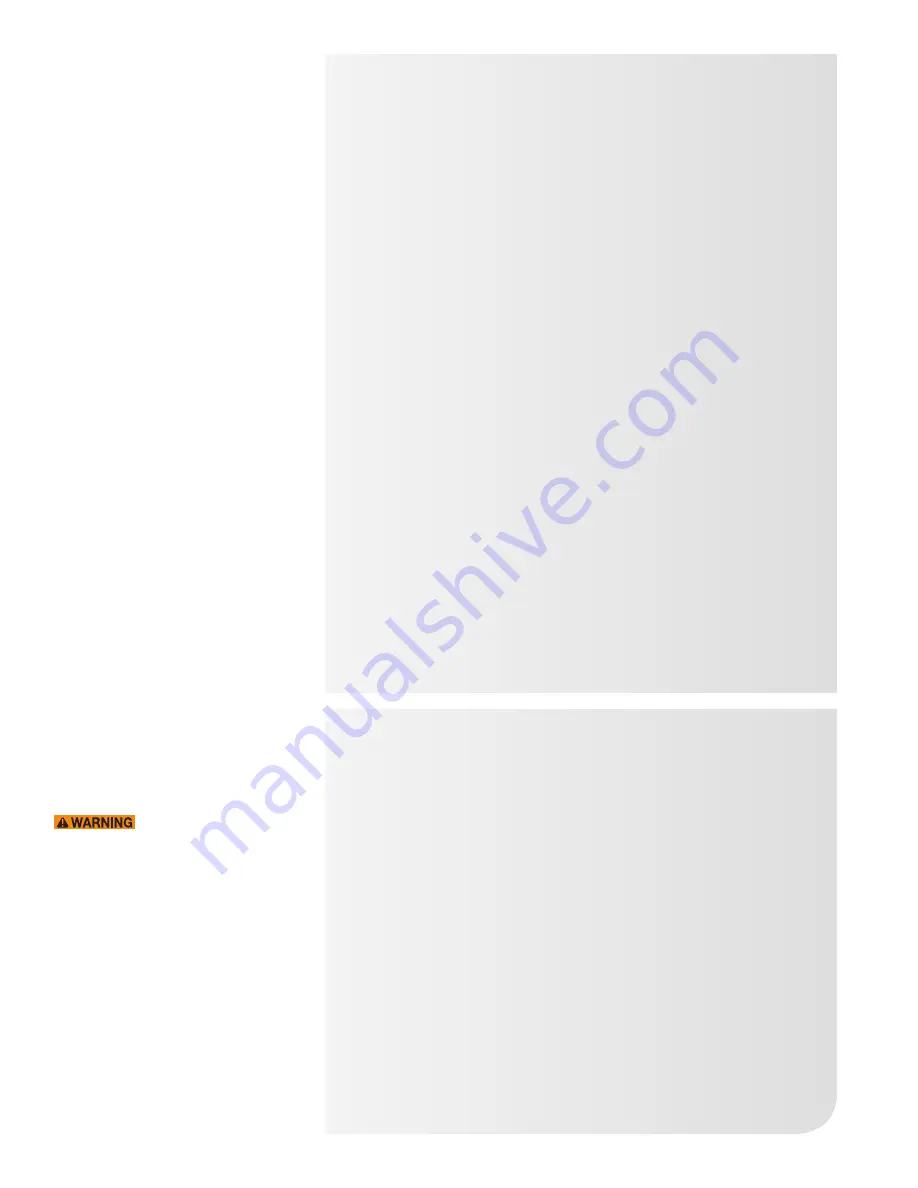
38
3-speed control
card
The unit has been factory
configured to produce the same
airflow as the standard PSC
motor on all speeds when using
the 3-speed control card with a
maximum of 10% higher than the
high speed setting available on
most units during readjustment.
If these settings are acceptable,
then no further configuring is
required.
If alternative airflows are
desired, use board mounted
potentiometers, marked as FL01,
FL02, FL03, to adjust the airflow
associated with each input. Each
output can be adjusted from 0
to 100% of the motor’s factory
programmed operating range
using an instrument screwdriver.
Insert the screwdriver into
the white center of the
potentiometer and turn clockwise
for an increase in airflow or
counterclockwise for a decrease
in airflow.
0-10 VDC control
card
The 0-10 VDC control card is
not configured at the factory
and needs to be used in
conjunction with a field installed/
provided thermostat and/or DDC
controller.
EC Motor
If the unit is equipped with an EC
motor, additional steps may be
required during the air balancing
process. Review project submittals
or order acknowledgment to
determine what type of EC motor
control is provided. Alternatively,
match the control board to the
illustrations.
The unit has been factory configured
to produce the same airflow as the
standard PSC motor on all speeds
when using the 3-speed control card
for vertical units and a maximum
of 10% higher than the high speed
setting when using the 0-10 VDC
control card. If these settings
are acceptable, then no further
configuring is required.
EC motor nameplate amperage
indicates the motor hardware peak
amperage while the motor full
load amperage (FLA) is limited by
the motor’s factory programmed
operating range, programmed
specifically for each unit size. The
programmed operating range is
generally only a portion of the motor
hardware full potential resulting in
the motor FLA being lower than the
nameplate FLA. Motor FLA will be
reflected on the Fan Coil serial tag
and should be used when sizing
building electrical requirements.
The control box needs to be powered
while adjustments are made. Line
voltage components are concealed
within a covered junction box.
However, the installer should take
all necessary precautions to avoid
contact with live voltage wires.
Controls operation
Before proper control operation
can be verified, all other systems
must be operating properly.
The correct water and air
temperatures must be present
to determine if the control
function is operating to design.
Some controls and features are
designed to not operate under
certain conditions. For example,
a 2-pipe cooling/heating system
with auxiliary electric heat, the
electric heat will not energize
when hot water is present.
A wide range of controls,
electrical options and
accessories may be used
with the units covered in this
manual. Review the approved
project submittals or order
acknowledgment for detailed
information regarding each
individual unit and its controls.
Since controls may vary from
one unit to another, care should
be taken to identify the controls
being used with each individual
unit and its proper control
sequence.
Controls