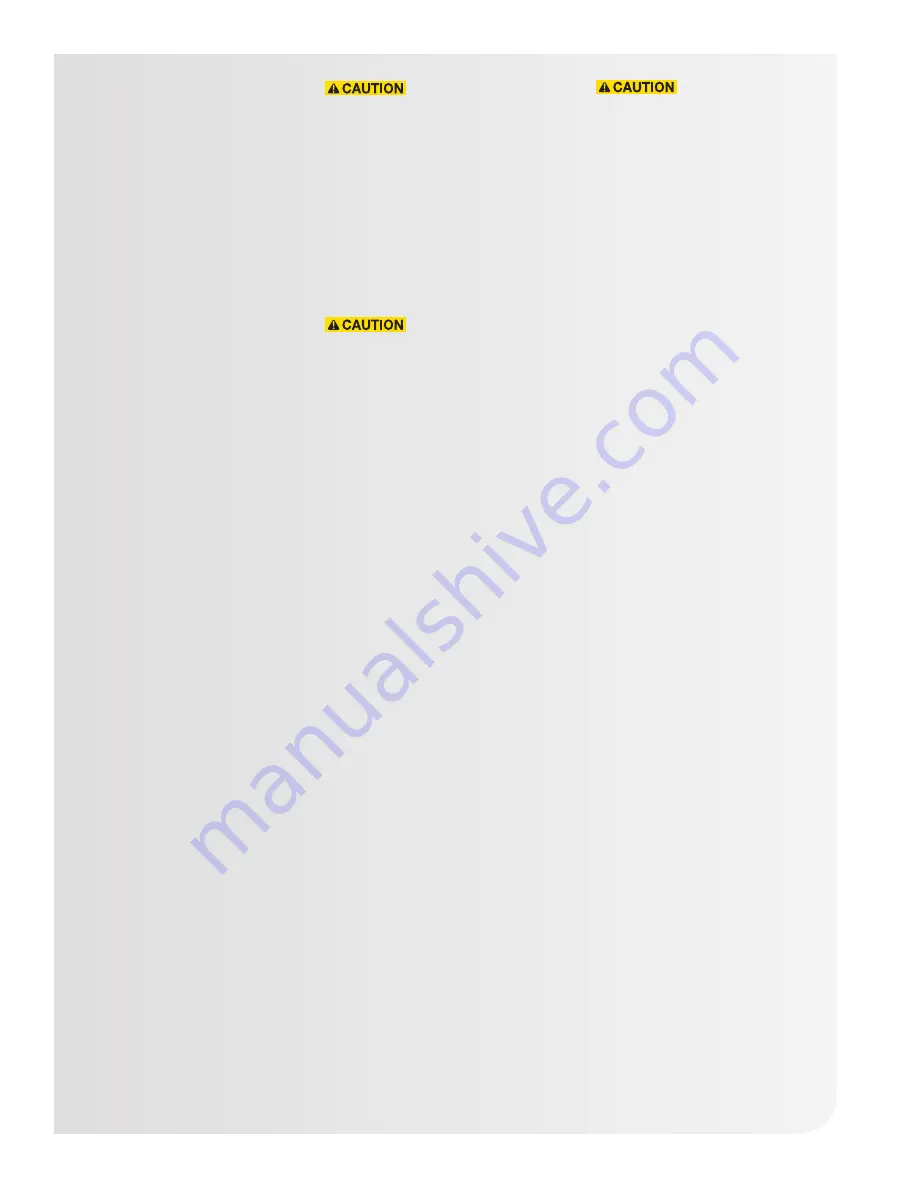
20
Enclosing unit
All wall framing is the
responsibility of others.
Normally the units are enclosed
in the field-furnished drywall
enclosure. The enclosure can
be furred out from the unit with
studs or the drywall can be
attached directly to the sheet-
metal cabinet. For maximum
sound attenuation, units should
be furred out and insulated. If
the riser pipes and electrical
conduit face the room interior,
then an enclosure must be furred
out from the unit to provide
proper clearance. If the drywall
is attached directly to the sheet
metal cabinet, use sheet metal
low-profile pan-head or drywall
screws, no longer than is
required to provide proper grip
to secure drywall to the sheet
metal cabinet. The front of the
unit is designed to have
drywall flush against the front of
the sheet metal cabinet. Either
1⁄2" or 5⁄8" drywall may be
used. Be sure to keep drywall
dust out of the unit. Drywall
dust is hard on motors, and coil
efficiency is reduced if drywall
dust is allowed to collect on the
coil fins. The manufacturer will
not be responsible for damaged
components due to drywall dust.
Do not apply sheet metal screws
or nails where they are subject to
penetrating the coil, riser pipes,
electrical junction boxes, and
raceways or where they may
impede the removal of internal
components.
Extreme care is necessary when
driving screws in the vicinity of
the control box, heat exchange
coils and drain pan to prevent
electrical shorts and water leaks.
The drywall material should not
be screwed to either the drain
pan edges or to the control-box
enclosure.
This unit is not intended for
direct attachment of wood,
chipboard, or similar paneling.
All wall finishes must be
preceded with drywall.
When cutting out supply and
return holes for grilles, be sure
to clean all drywall dust from
coils, drain pans, and blower
discharge plenum. After drywall
is in place and rooms are
prepared for final wall treatment,
the supply and return air
openings and control component
opening should be securely
covered to prevent introduction
of foreign material. If the wall
texture and/or color are to be
sprayed, cover the coil, fan, or
other unit parts. Unit warranties
are voided if paint or foreign
materials of any kind are present
on coil, fan, piping, wiring, or
other internal components.
A return air grille/access door
and discharge grille (if ordered)
are typically furnished with
each unit. These items are
usually shipped at time of finish
to the contractor’s specified
destination.
The units should not be operated
at anytime without complete
enclosure, supply grille, return
air grille, and filter in place.
Operation in any other condition
could result in motor overloading
or burnout, clogging of coil
surface, fan blade damage, or all
of the above.
Prior to installation of the return
grille, the following final checks
should be made:
1. Rotate the fan wheel by
hand to ensure that it is
free and does not rub the
housing. Rough handling
during shipment may have
caused the wheel to shift.
Adjust, if necessary.
2. Check to see that the
service valves are opened
and that the motorized
control valve (if supplied) is
set for automatic operation,
if of such type.
3. Vent all air from the coil and
related piping.
4. Check the drain line to see
that it is not clogged and
that it is properly positioned
with a downward pitch and
secured. Ensure that all
hose clamps are properly
connected and tightened
down. These connections
can come loose during
shipment and/or installation.
5. If the unit is equipped with
a combination stop and
balance valve in the return
line, the proper flow should
be set at this time.