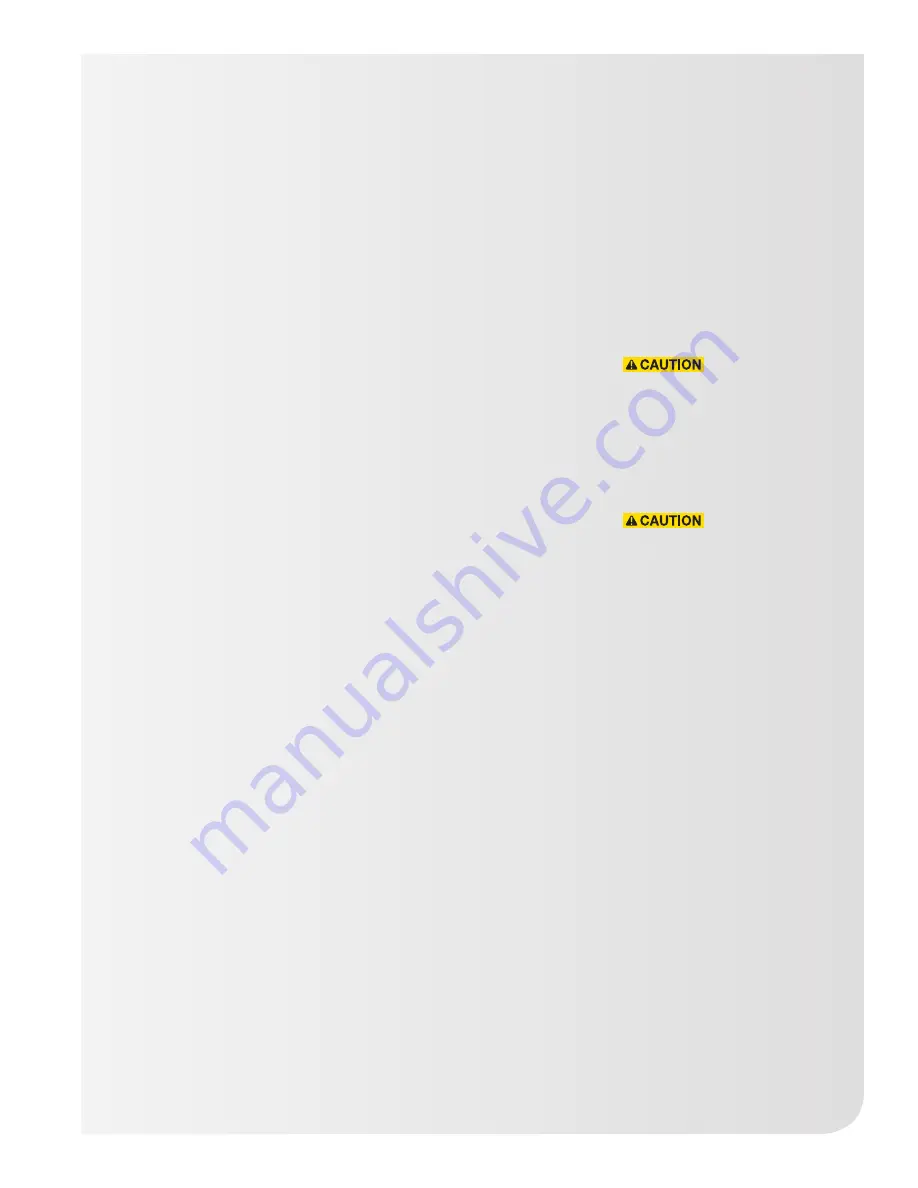
Unit and system checkout: Before powering
Unit checkout
■
■
Filter
Clean or replace filter, if
required.
■
■
Balancing/shut-off valves
Ensure that all isolation valves
are open and water control
valves are wired.
■
■
P-trap connections
Ensure all condensate P-trap
connections are secure.
Failure to do so could cause
extensive damage to drywall
and flooring.
■
■
Drain pan
Ensure drain hose from air coil
is properly positioned over
drain pan. Failure to do so
could cause extensive damage
to drywall and flooring.
■
■
Line voltage and wiring
Verify that voltage is within an
acceptable range for the unit.
Verify wiring and fuses/breakers
are properly sized. Verify that
low voltage wiring is complete.
■
■
Unit controls
Verify that the microprocessor
dip switches are set for
proper operation and system
configuration and the thermostat
is properly configured.
■
■
Entering water and air
Ensure that entering water and
air temperatures are within
operating limits of Tables 12
and 13.
■
■
Unit fan
Manually rotate fan to verify
free rotation and ensure that
blower wheel is secured to
the motor shaft. Be sure to
remove any shipping supports
if needed. Do not oil motors
upon start-up. Fan motors are
permanently lubricated from
the factory. Check unit fan
speed selection and compare
to design requirements.
■
■
Condensate line
Verify that condensate line is open
and properly pitched toward drain.
■
■
Water flow balancing
Record inlet and outlet water
temperatures for each heat pump
upon startup. This check can
eliminate nuisance lock outs and
high velocity water flow that could
erode heat exchangers.
System checkout
■
■
System water temperature
Check water temperature for
proper range and also verify
heating and cooling set points for
proper operation.
■
■
System pH
Check & adjust water pH if necessary
to maintain levels indicated in
Table 5. Proper pH promotes
longevity of hoses & fittings.
■
■
System flushing
Verify that all hoses are connected
end to end when flushing to ensure
that debris bypasses the unit heat
exchanger, water valves and other
components. Water used in the
system must be potable quality
initially and clean of dirt, piping
slag and strong chemical cleaning
agents. Verify that all air is purged
from the system. Air in the system
can cause poor operation and/or
system corrosion.
■
■
Cooling tower/boiler
Check equipment for proper set
points and operation.
■
■
Standby pumps
Verify that the standby pump is
properly installed and in operating
condition.
■
■
System controls
Verify that system controls
function and operate in the proper
sequence.
■
■
Low water temperature cut-out
Verify that low water
temperature cut-out controls
are provided for the outdoor
portion of the loop. Otherwise,
operating problems may occur.
n
System control center
If applicable, verify that the
control center and alarm panel
have appropriate set points
and are operating as designed.
Verify that ALL water control
valves are open and allow
water flow prior to engaging the
compressor. Freezing of the coax
or water lines can permanently
damage the heat pump.
To avoid equipment damage,
DO NOT leave system filled in
a building without heat during
the winter unless antifreeze is
added to the water loop. Heat
exchangers never fully drain by
themselves and will freeze unless
winterized with antifreeze.
47
Start-up